A caution, A warning, Caution – Carrier 61SW User Manual
Page 7: Warning
Attention! The text in this document has been recognized automatically. To view the original document, you can use the "Original mode".
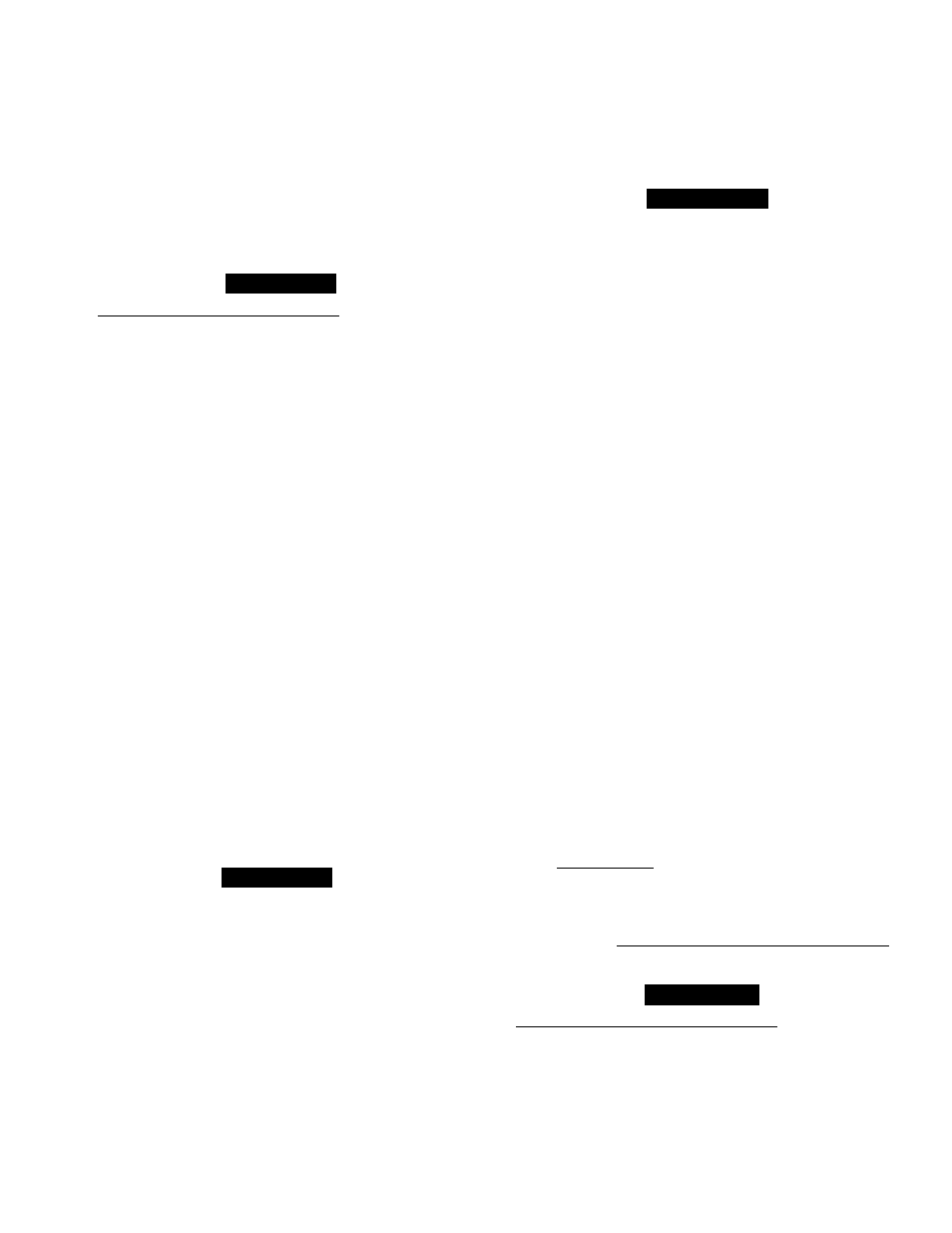
If a manual disconnect switch is to be mounted on the appliance,
select a location where a drill or fastener will not contact electrical
or gas components.
NOTE:
Use only copper wire between the disconnect switch and
the unit.
Check all electrical connections (both factory and field) for
tightness. Recheck tightness of electrical connections after the unit
has reached operating temperatures.
Step 1—Filling The Boiler
Check to be sure that all connections have been made. Before
atternpting any operations, fill the system with water.
A
CAUTION
I Never light a burner under an empty boiler.___________________ |
1. Close air vents on all radiation units,
2. Open water supply valve on each radiation unit.
3. Close drain cock and air bleed screw on boiler expansion tank.
4. Open valve in line from boiler to expansion tank.
5. Open water inlet valve to boiler and leave open.
6. Starting with lowest radiation unit, open air vent.
7. Working from the lowest to the highest radiation unit, repeat
item 6 until you have vented every radiation unit in the
system.
NOTE:
Systems with an automatic vent on each radiation unit
will not require manual venting.
8. Check temperature/pressure gage. It should read between 10
and 15 psig.
9. Check system piping connections for leaks.
START-UP AND ADJUSTMENTS
NOTE:
Safe lighting and other performance criteria were met
with the gas manifold and control assembly provided with the
boiler when it underwent testing as specified in ANSI Z21.13b-
1991.
Check to be sure that all connections have been made. Before
attempting any operation, fill thé system with water. For steam
boilers, fill to the water line. Never light a burner under an empty
boiler.
CHECK PILOT TO BE SURE THAT ALL CONNECTIONS
HAVE BEEN PROPERLY MADE.
Light the pilot, using the procedure outlined on the lighting
instruction plate attached to the boiler.
A
CAUTION
The boiler is equipped with an intermittent-type ignition
device that functions during each thermostat on cycle. DO
NOT USE MATCH OR OTHER OPEN FLAME TO LIGHT
-
pilot
:
1. If the gas supply line was not purged before connecting the
^^=^boilerrit‘will“be~full'of'aii77'is'it"would'talce^long time to vent
this air through the small pilot port, it is recommended that
pilot supply line be disconnected and be allowed to purge until
the odor of gas is detected. Never purge gas lines into the
combustion chamber. Iinmediately upon detection of gas
odor, reconnect pilot supply tube. Allow 5 minutes to elapse,
then light pilot using the procedure outlined on the lighting
instruction plate attached to the boiler.
2. The pilot flame should be soft blue in color and should be
checked periodically. The flame lies under the carryover ports
■ of burners and merges with the carryover flames. The pilot
flame should not touch the boiler section. If the pilot flame
does not have the appearance as described, it can be adjusted.
a. The gas valve is equipped with an adjustable screw.
Remove capscrew to expose adjustable screw. Turn screw
until flame has desired appearance.
b. Replace capscrew.
A
WARNING
The boiler is equipped with an intermittent ignition device
(IID). Check the safety pilot operation as follows; Attach a
low-voltage test light to the electrical leads of the gas valve at
terminals marked 1 (or TH) and 2 (or TR). With the
thermostat set above room temperature (pilot and main
burners operating), turn OFF the gas supply to burners and
pilot with main shutoff valve. If the test light goes out within
45 sec, the safety pilot is functioning properly. If the light
, does not go out within 60 sec, replace the safety pilot. Place
the boiler in normal operation by following the lighting
instructions on the boiler.
GAS INPUT-DETERMINE THE GAS INPUT
1. Natural gas
a. Turn off all other gas appliances and pilots.
b. Measure time (in sec) for gas meter test dial to complete 1
revolution.
c. Refer to Table 5 for cu ft of gas per hr.
d. Multiply cu ft/hr X heating valve' of gas. Obtain heating
valve of gas from local gas utility.
EXAMPLE: .
Btu heating input = Btu/cu ft x cu ft/hr
Heating value of gas = 1070 Btu/cu ft
Time for 1 revolution of 2-cu ft dial = 72 sec
Gas rate = 100 x 1070 = 107,000 Btuh
e. The measured gas input should not exceed the gas input
shown on the unit rating plate.
f. Observe manifold pressure. It should be adjusted to read
3.5- ±0.3-in. wc. Adjust pressure by using an adjusting
screw in the gas pressure regulator stem. (This screw is
concealed under the regulator sealing cap.) Turn screw
clockwise to increase pressure and counterclockwise to
decrease pressure.___________________________
-Small-changes~ihHnput-can-be-made--by-changing-the-manifold“
pressure as previously described. However, the manifold pressure
should not vary more than 0.3-in. wc from the rated pressure.
A further change in gas rate can be accomplished, if necessary due
to high altitude, by changing the fixed orifice at the burners.
A
CAUTION
I Do not under any circumstances redrill orifices.________________
2. Propane gas models
a. These units are equipped with pressure regulators. The
burner orifices are sized to give rated input at a manifold
pressure of 10-in. wc. Check manifold pressure and, if
necessary, adjust pressure.
3. High altitude ratings are approved for altitudes to 2000 cu ft
for all gases. Ratings for altitudes over 2000 ft are 4 percent
less for each 1000 ft above sea level.