Winco 1B40 User Manual
Page 16
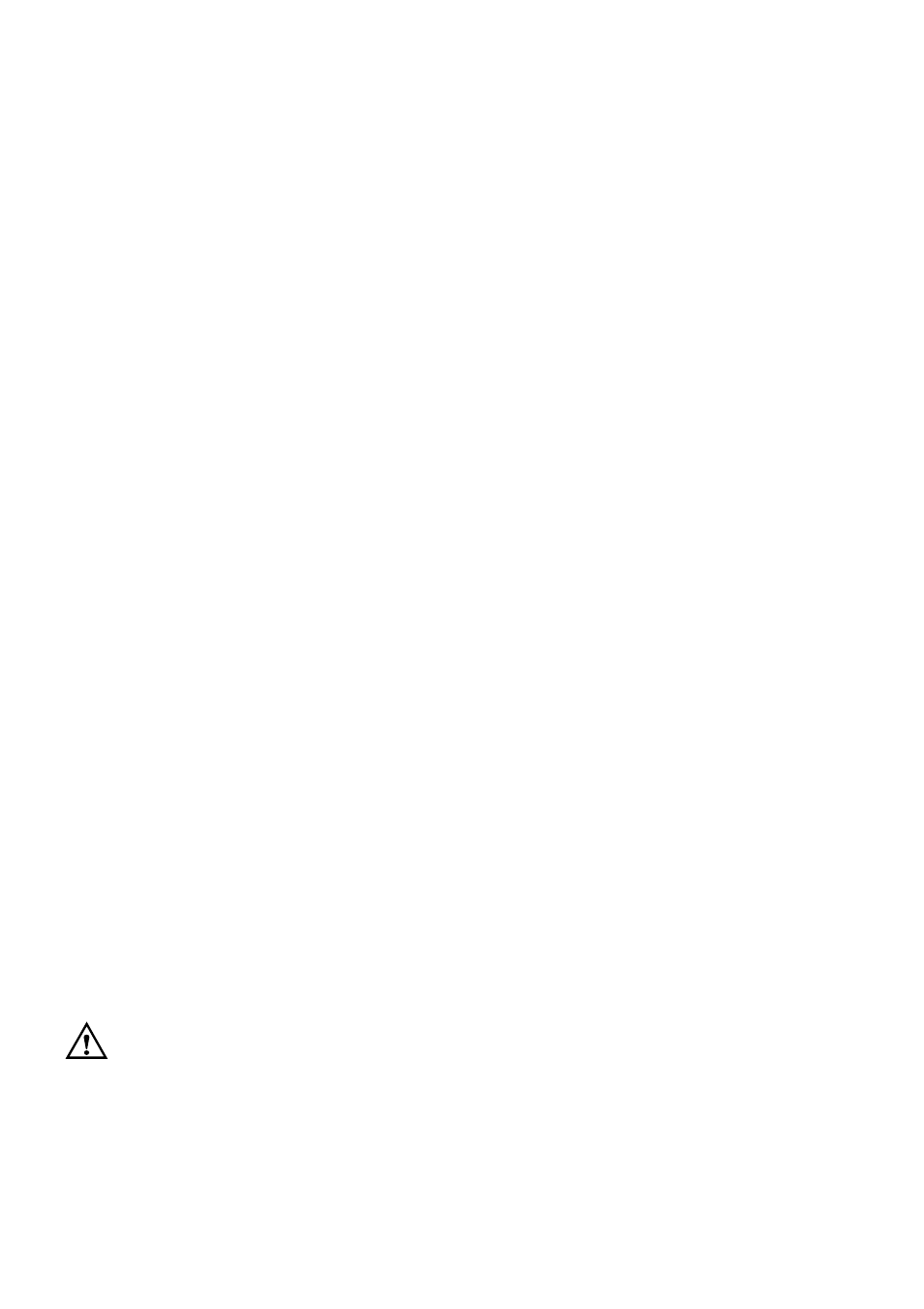
5.3.
Maintenance every 250
operating hours
5.3.1. Oilbath air cleaner maintenance
– Take off oil reservoir „1“ and clean it, Fig. 27.
– Rinse out filter element „2“ in diesel oil; allow
it to drip thoroughly and wipe it down before
re-assembling the air cleaner.
– If severely contaminated, clean filter
housing „3“.
Never attempt to repair the oilbath air cleaner by
welding, brazing etc., as this could damage the
filter beyond repair and cause engine damage.
– Re-attach parts previously removed from the
air cleaner and add oil so that it is ready for
use, Chapter 4.1.2.
Version with cyclone-type dust trap
– Take off dust collector „1“, empty it and
wipe clean (dust collector must remain dry),
Fig. 28.
– Clean intake aperture „2“ (also keeping it dry).
Important:
Do not add any oil to the dust collector.
– Attach the cyclone-type dust trap and secure
with the wing nut.
5.3.2. Changing engine oil
The engine must be standing level and be
switched off.
Only change the oil when the engine is warm.
Danger of scalding from hot oil !
Trap the old oil and dispose of it in
accordance with local legislation.
– Take out oil drain plug „1“ and allow the oil to
drain out, Fig. 29.
– Clean the oil drain plug „1“, fit a new washer
„2“, insert and tighten.
Tightening torque: 50 Nm.
– Add engine oil, Chapter 4.1.1.
5.3.3. Checking and adjusting valve
clearances
Only carry out adjustments when the engine is
cold (10 - 30 °C).
– Remove air cleaner cover, fig. 30 and noise-
insulating hood, Fig. 31.
– On version with oilbath air cleaner, remove
screw „2“ and take off cover plate with noise-
insulating hood, Fig. 32.
– Remove any contamination adhering to the
cover for the cylinder head.
– Remove screws „1“ (two screws on 1B20 and
1B30 engines, three screws on 1B40 engines)
and take off the cylinder head cover with gas-
ket „2“, Fig. 33.
– Remove rubber cap from the inspection hole
cover, Fig. 34.
– Turn the engine over in the normal direction of
rotation until the valves are in the overlap po-
sition (exhaust valve not yet closed, inlet valve
starts to open).
– Turn the crankshaft through 360° in the
normal direction of rotation and align exactly
to the • • •-marking, Figure 34.
– Check valve clearances with feeler gauge „1“
(0.10 mm), Fig. 35.
– If valve clearances require adjusting, slacken
off screw „2“ and turn hex nut „3“ until feeler
gauge „1“ can be pulled through with just
slight resistance when screw „2“ is retight-
ened.
– Fit cover for cylinder head and tighten evenly,
always using a new gasket.
15