LAARS Mighty Therm VW (Sizes 2000-5000) - Installation, Operation and Maintenance Instructions User Manual
Page 14
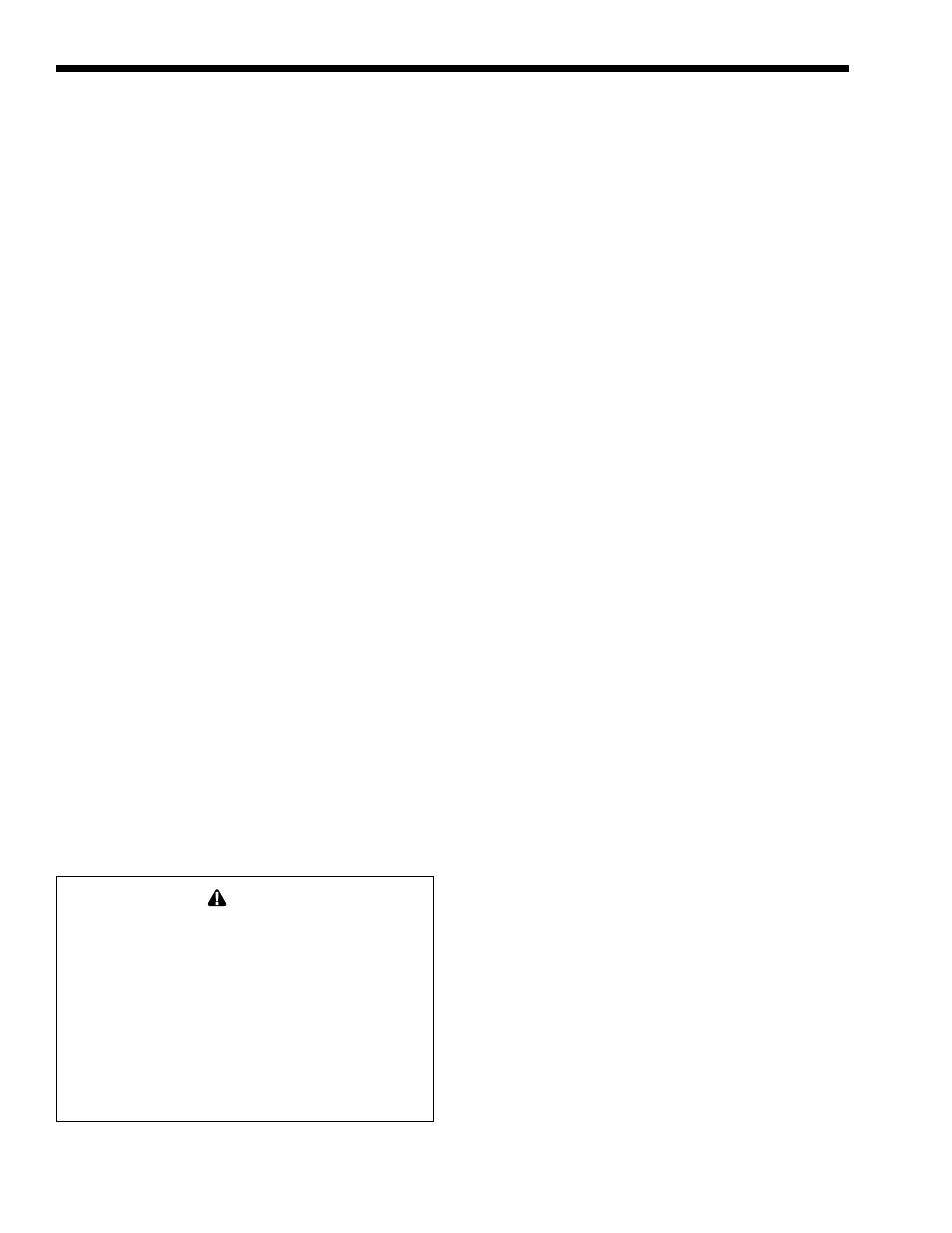
LAARS Heating Systems
Page 14
instructions for proper pilot flame pattern). If
flame has the appearance of “sooting” tips,
check for debris near orifices. Call service
technician.
3.
Inspect the venting system for obstruction,
leakage, and corrosion at least once a year.
4.
Keep heater area clear and free from
combustible material, gasoline and other
flammable liquids and vapors. Heater surfaces
are hot and could ignite combustible material.
5.
Be certain all combustion air and ventilation
openings are unobstructed.
6.
Check for fouling on the external surfaces of the
heat exchanger every six months.
Note: After installation and first start-up, check
the heat exchanger for fouling after the following
periods of operation: 24 hours, 7 days, 30 days, 90
days, and once every six months thereafter.
Fouling on the external surfaces of the heat
exchanger is caused by incomplete combustion, and is
a sign of combustion air and/or venting problems. As
soon as any fouling is observed, the cause of the
fouling should be corrected (see Section 5
Troubleshooting). The heat exchanger can be checked
with a flashlight by locating a mirror under the
burners. An alternate method is to remove the venting
and top panel as necessary to inspect from above.
Also, check the vent system for defects at the same
time.
a.
If cleaning is required, shut off all
electrical and gas supply to the heater.
b.
To expose the heat exchanger:
Remove top panel covers located at the base of
the front and rear flue collector panels. Remove
all but the top screws on each side of the front
and rear flue collector panels. The panels can be
swung outward and propped up to reveal the heat
exchanger. Remove all heat exchanger baffles.
c.
Remove all burners:
Caution
Black carbon or green soot on a dirty heat
exchanger can, under certain conditions, be ignited
by a random spark or open flame. To prevent this
unlikely occurrence, dampen the soot deposits with
a wet brush or fine water spray before servicing or
cleaning the heat exchanger.
With a wire brush, remove soot and loose scale
from the heat exchanger. Do not use water or
compressed air for cleaning. Clean fallen debris
from the bottom of the heater. Check that burner
ports are clear and pilot assembly is free of debris.
d.
Reassemble in reverse order:
Be sure to replace the heat exchanger baffles.
7.
The gas and electric controls installed on the
heaters are designed for both dependable
operation and long life. But the safety of this
equipment depends completely on their proper
functioning. It is strongly recommended that the
basic items be checked by a competent service
technician every year, and replaced when
necessary. The basic controls are:
a.
Water temperature controls.
b.
Pilot safety system.
c.
Automatic electric gas valve(s).
d.
Flow sensing safety device.
8.
Low water cutoffs should be inspected every six
(6) months, including flushing or float types.
Note: Warranty does not cover any damage
caused by lack of required maintenance or improper
operating practices.
9.
Both modulating and staged valves are adjusted
at the factory for minimum permissible rates,
and should not be readjusted.
SECTION 5.
Troubleshooting and Analysis of
Service Problems
1.
For proper service and problem diagnosis of the
heater and heater system, the following tools are
required:
a.
Gas pressure test kit with range from zero
to 14" W.C. Either a slack tub manometer
or an accurate gas pressure gauge is
acceptable with proper adaptors which will
connect to the available fittings in the line
and on the gas valve.
b.
Electric meter(s) with the following ranges:
0 to 500 volts A.C.
0 to 1000 ohms continuity.
c.
Millivolt meter with the following ranges:
0 to 50 millivolts
0 to 500 millivolts
0 to 1000 millivolts
d.
Tube cleaning kit consisting of reamer,
stainless steel brush, speed handle and
handle extensions.
e.
Heater thermometer (with 1/2" NPT well)
100-240° F.
2.
In addition, the heater should be equipped with a
system pressure gauge and a thermometer with
proper ranges for heater operation.