LAARS Mighty Therm VW-PW (Sizes 175-400) - Installation, Operation and Maintenance Instructions User Manual
Page 15
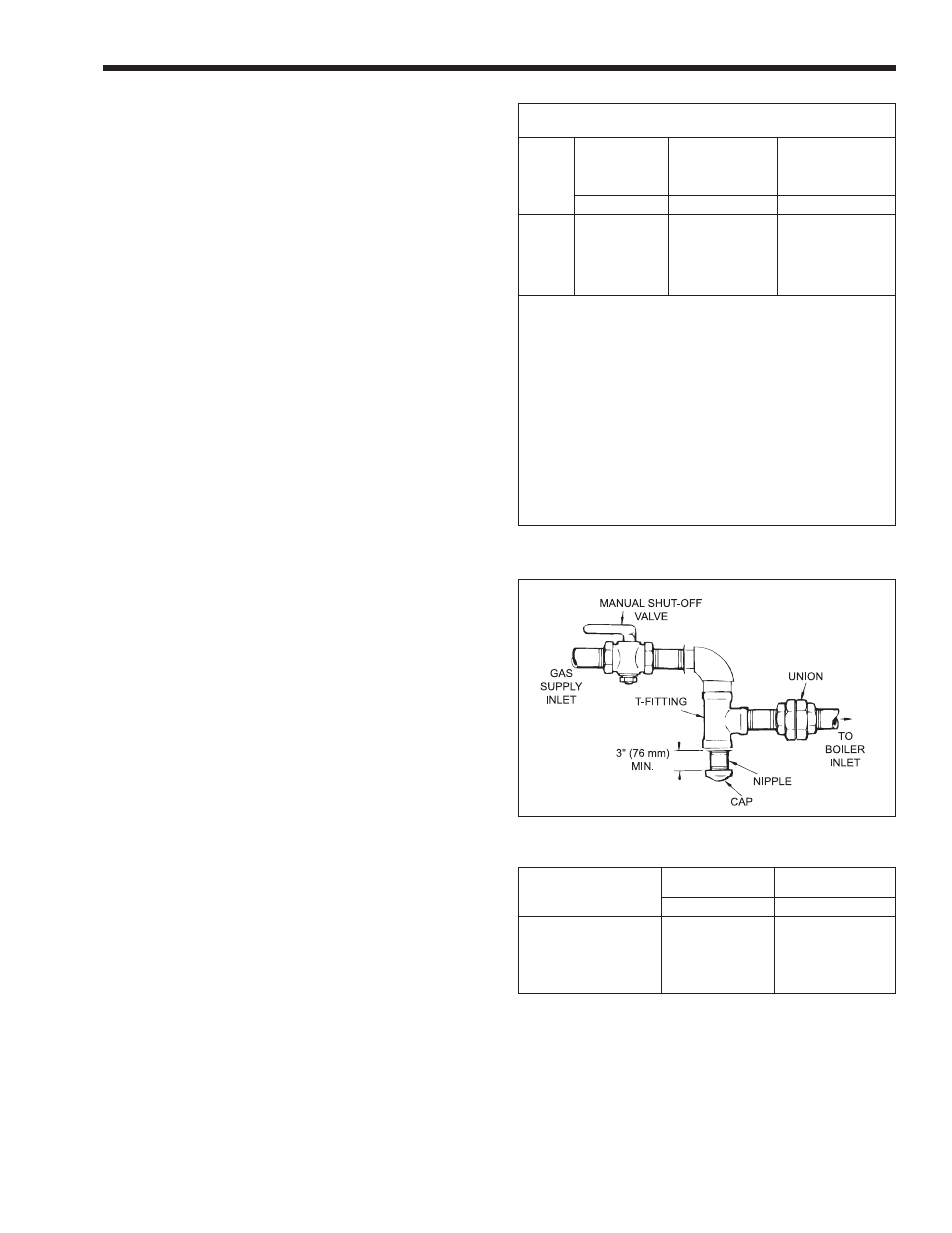
Mighty Therm Volume Water Heaters
Page 15
7.
Check the oil level in the pump before starting
the heater. Oil the pump every three months. Oil
pumps located in excessively hot or dusty
locations once a month. Self-lubricating pumps
do not require oiling.
8.
Fill the bearing assembly to the lower level of the
overflow vent.
9.
Add 5 or 6 drops of oil to the front and rear of
the motor. Use 20W non-detergent oil.
2.6.10 Storage Tank Installation
1.
Be sure the floor is structurally capable of
supporting the tank when it is filled with water,
and is waterproof.
2.
Place the tank so that manholes, inspection
covers, nameplates and drain valves are
accessible.
3.
Be sure the tank is suitable for the water in the
system. Some water is corrosive and requires a
protected tank. Most tanks are available with
glass, plastic, or galvanized linings.
4.
If the tank is glass-lined, it should be equipped
with a suitable magnesium anode. It is a good
practice to replace the anode when it is
approximately 50 percent used. The factory
warranty on a glass-lined tank may be void if a
satisfactory anode is not in place at the time of a
failure or if it is consumed by cathodic action.
5.
The tank must be lined if a water softener is
installed in the system.
6.
Make sure the tank connections in the heater-
tank circulating loop are the proper size (see
Section 2F-5). If tappings are smaller than the
recommended pipe size, a larger pump may be
required. Consult the factory if in doubt.
7.
Install a pipe in the tank drain fitting that goes to
a floor sink, and install a drain valve. If a floor
sink is not available, install a hose bib.
8.
Hot water tanks in an existing installation are
likely to have silt deposits on the bottom.
Therefore, it is important to extend the pump
suction pipe in the tank to a position near the top.
Pipe the return from the heater to the bottom of
the tank.
Incorrect installation can cause rapid failure of
water tanks due to electrolysis. Tanks must be
installed with dialectric connections to
electrically isolate the tank from stray current.
Note that use of brass or bronze connectors does
not replace the need for dialectric connections.
2.6.11 Thermal Circulation of Hot Water
in Cold Water Supply Lines
Under certain circumstances, thermal circulation
will occur in the cold water pipe supplying the water
to the heating system. This happens in a multi-story
building when the cold water pipe rises from its
Figure 24. T-Fitting and sediment trap.
connection to the system. To correct the problem, a
check valve in the cold water line supplying the heater
will prevent thermal circulation, and a small expansion
tank will permit heated water to expand without
popping off the relief valve.
Distance from Gas Meter or Last Stage Regulator
0-100 feet
100-200 feet
200-300 feet
0-30 m
30-60 m
60-90 m
Boiler
Nat.
Nat.
Nat.
Size
in.
mm
in.
mm
in.
mm
175
1
25
1¼
32
1¼
32
250
1¼
32
1¼
32
1½
38
325
1¼
32
1½
38
1½
38
400
1¼
32
1½
38
2
51
Notes:
1. These numbers are for natural gas (0.65 Sp. Gr.) and
are based on ½ inch (13mm) water column pressure
drop. Check supply pressure with a manometer, and
local code requirements for variations. For liquefied
petroleum gas, reduce pipe diameter one size, but
maintain a ½ inch (13mm) minimum diameter.
2. Check supply pressure and local code requirements
before preceding with work.
3. Pipe fittings must be considered when determining gas
pipe sizing.
4. For propane gas: Reduce pipe diameter one size, but
maintain a ¾ inch (19mm) minimum diameter.
Table 5. Natural Gas and Propane,
Pipe Size Requirements.
Supply Pressure
Natural Gas
Propane Gas
Water Column
in.
mm
in.
mm
Minimum
6.5
165
11
279
See Rating Plate
Maximum
9
229
14
356
Table 6. Gas Supply Pressure Requirements.