Doepfer MTC64 Output Board (transistor driver board) User Manual
Page 2
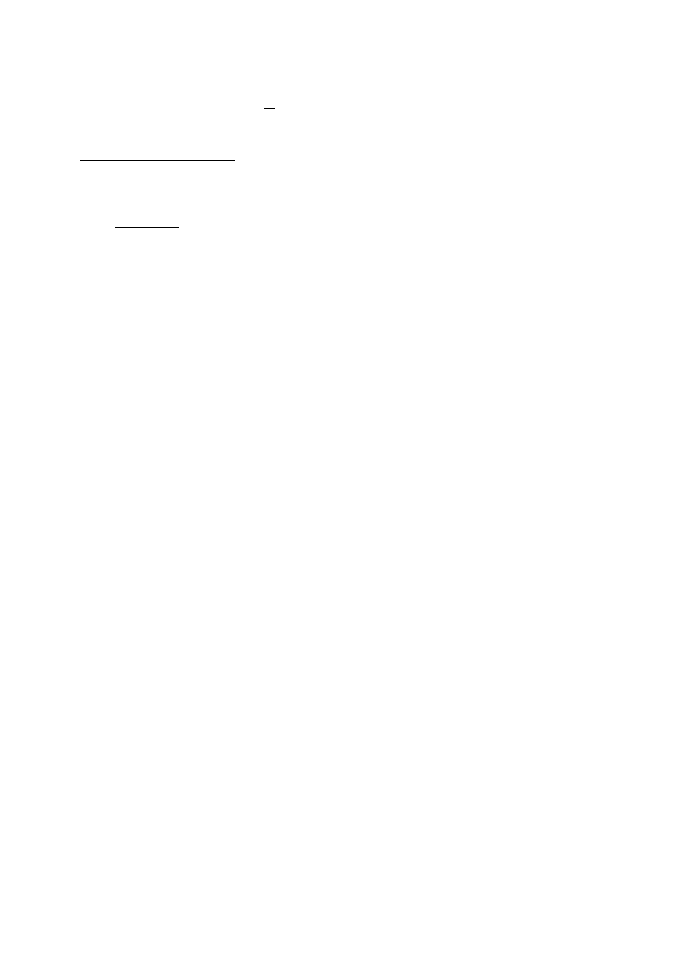
The sketch on the next page shows the wiring of the MTC64 driver board and the loads (relays,
magnets, motors or similar) to be controlled by the MTC64 driver board. As mentioned a suitable
power supply has to be used for the loads. Only if the loads can be driven with 5V (e.g. LEDs or 5V
reed relays) and the total current for all loads (i.e. the sum of the currents of all loads) is less than
100mA, the internal +5V of the MTC64 main board can be used. In this case the +5V are available at
the solder terminal labelled JP20/+5V on the MTC64 driver board.
Notes for the wiring procedure:
• Connect the pin header JP18 of the driver board to the pin header JP5 of the main board with a 10
pin ribbon cable with 10 pin female connectors on both ends. Pay attention to the correct
alignment of both connectors (GND and +5V are printed on both boards).
→
→
→
→ ATTENTION ! If two or more driver boards are used a special 10 pin ribbon cable with the
corresponding number of female connectors has to be used (one for JP5 of the main boards one
for each JP18 of the driver boards). The maximum assembly is one main board and 4 driver
boards. For this version a ribbon cable with 5 female connectors is required. You can order a
suitable ribbon cable from Doepfer if you are not able to built the cable by your own. In this case
please specify the cable: number of female connectors and the distances between the connectors.
• Connect the pin header JP17 of the driver board to one of the pin headers JP1, JP2, JP3 or JP4
of the MTC64 main board with a 16 pin ribbon cable with 16 pin female connectors on both ends.
• Connect the GND terminal of the power supply used for the loads with the terminal GND/JP19 of
the driver board.
→
→
→
→ not applicable if the internal +5V are used as power supply for the loads
• Connect the positive terminal of the power supply used for the loads with the positive terminals of
all loads. Some loads are not polarized, i.e. it does not matter which terminal is connected to the
positive terminal of the power supply. Lamps, magnets or relays are normally not polarized,
motors are normally polarized. But in every case you have to look at the specifications of the
loads to find out if they are polarized.
→
→
→
→ not applicable if the internal +5V are used as load power supply. In this case the terminal
labelled +5V/JP20 of the driver board is used as positive power supply terminal.
• Connect the second terminal of each load with one of the outputs of the MTC64 driver board
(JP1...JP16). For polarized loads these are the negative or GND terminals.
• In case that inductive loads (e.g. magnets, relays, motors) have to be switched, then one of the
protecting diodes (marked with an asterisk in the schematics) is required. The best solution is to
solder the diode in parallel to the load as the load has to be soldered in any case. For relays with
built-in diode the diode is not necessary.
• In case that loads above 500mA have to be switched the following modifications have to be
carried out: The 2k2 base resistors of the switching transistors have to be reduced to about 270
Ohm. It is not necessary to remove the 2k2 resistors. The best solution is to solder 270 Ohm
resistors in parallel to the 2k2 resistors. The shift register circuits CD4094 on the MTC64 main
board have to replaced by 74HC4094 as these are able to deliver a higher current. You could
order a modified version for the driver and main board if you know in advance that the loads will
exceed 500 mA.
• Power up the MTC64 main board (i.e. insert the wall outlet power supply)
• Power up the power supply for the loads
• If the loads behave inverse the polarity has to be changed (jumper 5 / JP7 on the main board)