Checkline ZF2 User Manual
Page 6
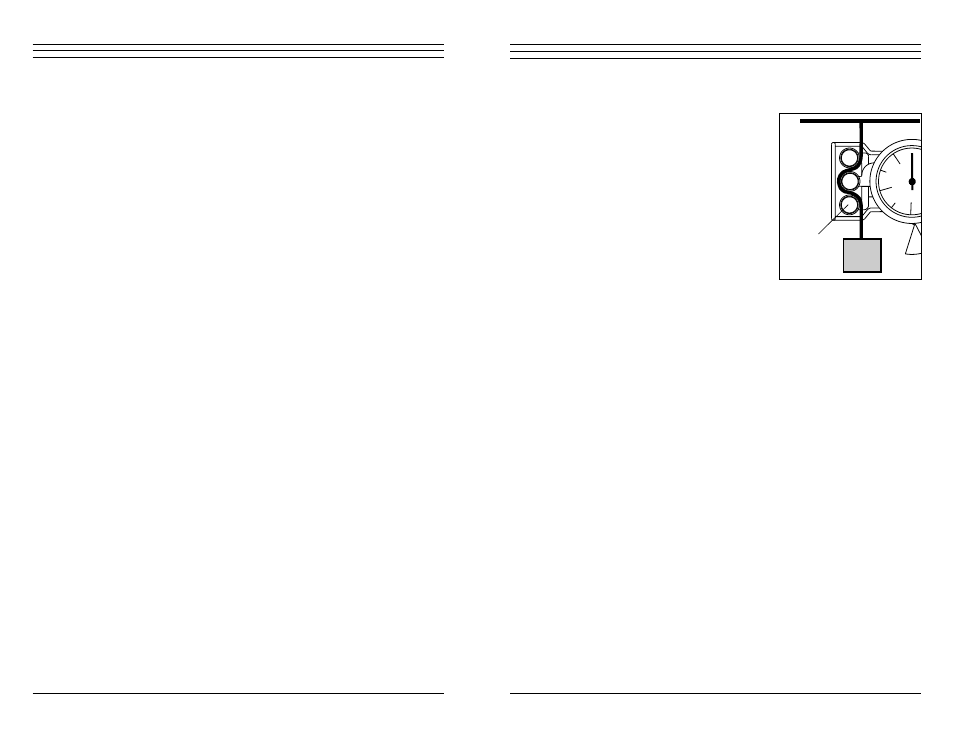
8
5
4.0 CALIBRATION
NOTES
The calibration process involves hanging laboratory
weights from a fixed point, engaging the vertical
line material which holds the weights with the
tension meter 3-roller system, marking a blank dial
face where the scale pointer comes to rest for each
weight used, dividing the spaces between load
“reading” marks and finish marking and numbering
to show calibration marks and “readings” on the dial
face.
The procedure requires specialized skills
and the following material:
1. A load stand to simulate the setup shown here.
2. A set of precision laboratory weights to cover the tension range of the instrument.
3. Factory “standard” nylon monofilaments as shown in the Table on page 6.
4. A Special Calibration Fixture and Metric Wrench.
A full, detailed calibration procedure is available upon request.
determination is best made by the user’s Quality Assurance Department based on the
user’s experience. However, a quick calibration check near the anticipated process ten-
sion levels should be done to confirm the integrity of the instrument, as follows:
1. At the beginning of each work session
2. Every time a unit is dropped
3. Whenever process readings seem to be out of
tolerance for no apparent reason
The quick check can be made with a simple load stand, as shown in 4.0, using a sam-
ple of the process material and weights that are close to the tensions encountered in the
process. Be sure to move the tension meter up and down slowly to simulate the motion
of the running process material. This will check the condition of the guide roller ball
bearings and remove any inertia effect of the movement. Readings that change with
this motion reversal may indicate the possibility of a guide roller ball bearing problem.
In the case of wire, which might be slightly deformed by the action of the 3-roller sys-
tem during static measurement, always move to a fresh portion of the wire each time a
measurement is made. (In production, the instrument always “sees” a fresh portion.)
W
Roller
Vertical
Material
Path