Tjernlund SS2 SideShot with UC1 Universal Control (Version X.06) 8504105 Rev C 07/05 User Manual
Page 12
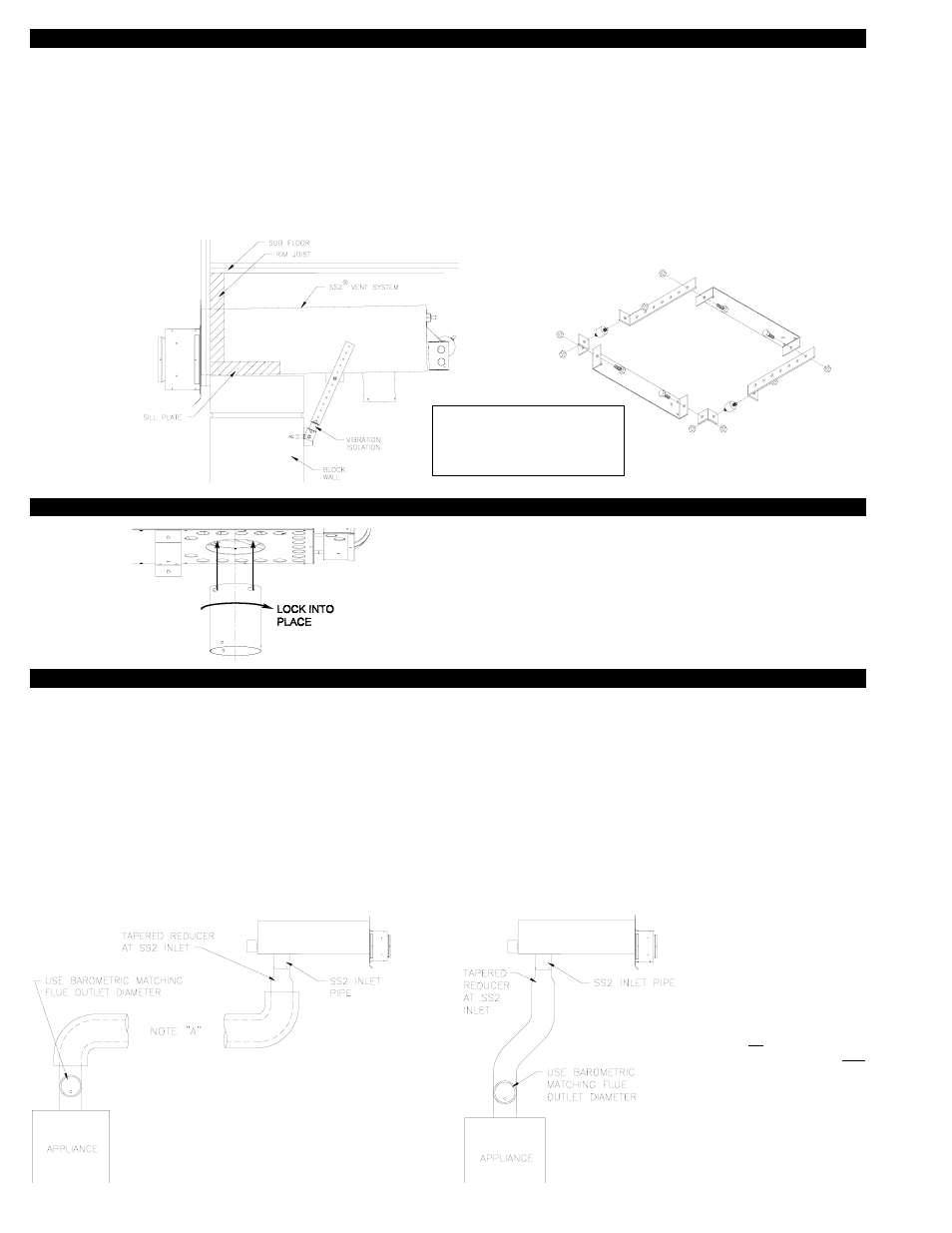
INSTALLATION OF WALL SUPPORT BRACKET
1. To prevent damage to the SS2, temporarily support the bottom of the SS2 cabinet (prop on ladder top) while assembling the wall support bracket.
Assemble the wall support bracket as shown, (See Diagram H).
2. Connect mounting bracket to SS2 using (4) #8 x 3/8” sheet metal screws. Line up holes on bottom of SS2 with mounting bracket to ensure proper
placement, (See Diagram H).
3. Adjust the wall support bracket so that a slight pitch is maintained for moisture drainage and vibration isolation. Use the prepunched holes on
the wall bracket as a template to mark holes to be drilled into the side wall for mounting screws, (See Diagram H).
4. a) If installing the bracket into a wood wall, drill 2 pilot holes at each point established in step 3 with a 1/8" drill bit approximately 1" deep and
install the screws provided to secure the bracket to the wall.
b) If installing the bracket into a masonry wall, drill 2 holes at each point established in step 3 with a 1/4" masonry drill bit. Tap the masonry
anchors into the 2 holes drilled and screw the wall bracket onto the wall.
INLET PIPE INSTALLATION
INSTALLATION OF VENT PIPE
When installing the SS2 Vent System on an oil appliance, a full size barometric draft control must be used. Install the barometric draft control as shown,
(See Diagram J). The SS2 may only be installed on gas appliances equipped with a draft hood, draft diverter or barometric draft control. The SS2 inlet
pipe is designed to accept 4" vent pipe. Choose type of vent pipe based upon fuel and heater manufacturer’s recommendations. The vent pipe used
must be in compliance with local codes and the listing of the vent pipe manufacturer. When necessary, install tapered reducers and increasers as
shown below.
Determine vent pipe layout which will allow for the least amount of elbows to the appliance. Calculate the equivalent vent pipe length from the appli-
ance to the SS2 Vent System by adding the straight vent pipe length and the equivalent elbow lengths together. Each 90 degree elbow is equal to 10
feet (3 meters) of straight vent pipe, each 45 degree elbow is equal to 5 feet (1.5 meters) of straight pipe. The equivalent vent pipe length must not
exceed 50 feet (15 meters) from the appliance to the SS2 Vent System. Vent runs of over 15 linear feet (4.5 meters) require the use of an approved,
insulated vent connector to prevent problems related to condensation. It is not necessary to maintain a 1/4" rise per foot of horizontal when Side Wall
Venting.
NOTE: Installing a vent pipe “jog” on vertical vent pipe layouts allows for easier dismantling if servicing is necessary, (See Diagram J).
9
DIAGRAM H
IMPORTANT:
Adjust SS2 mounting bracket for
a slight downward pitch towards
exit terminal.
DIAGRAM I
1. Remove 4” round inlet pipe from box.
2. Align the 4 slots of the inlet pipe to the 3 pins and proving switch
sensing tube, push pipe up until it bottoms out in the SS2 inlet.
3. Turn the inlet collar clockwise to lock in place, (See Diagram I).
IMPORTANT: After vent pipe is installed verify inlet pipe is locked
tightly in place.
NOTE “A”
Any vent pipe run that exceeds 15 linear feet
(4.5 meters) in length must use an approved,
insulated vent pipe. DO NOT EXCEED 50
EQUIVALENT FEET (15 METERS).
IMPORTANT: Oil installations must
have a barometric draft control. Gas
installations must have a draft hood,
diverter or barometric draft control
installed. Always use a vent pipe /
connector of the same diameter as the
appliance flue outlet. Use a tapered
reducer near the SS2 inlet pipe if the
appliance flue outlet is larger than 4”.
Typical short vent
pipe installation.
DIAGRAM J