Specifications (cont’d) – Dynalco SW-100 Speed Switch User Manual
Page 3
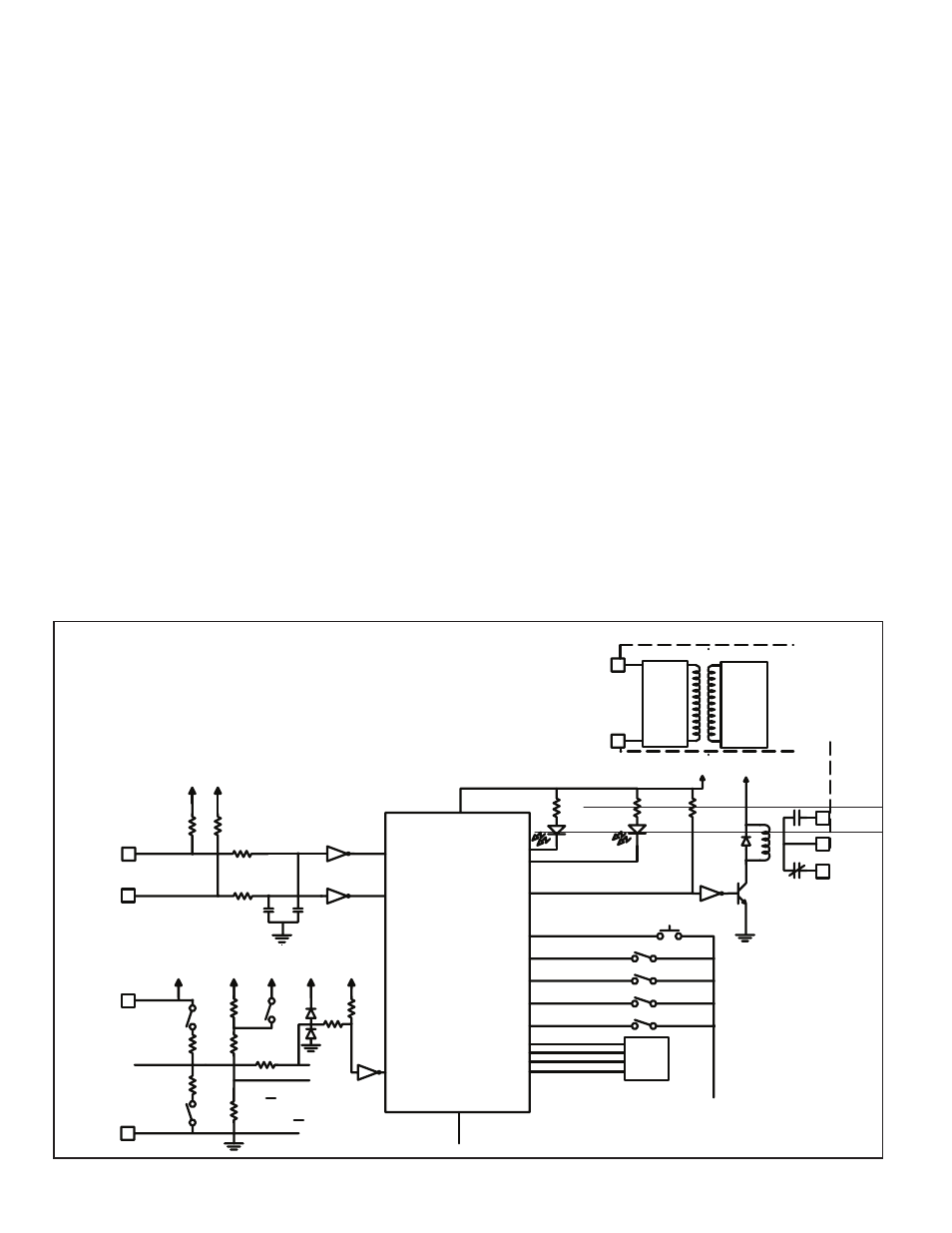
SPECIFICATIONS (Cont’d)
5. CONTROL INPUTS: Active low (V
IL
= 0.5 V max.) internally pulled up to 5
VDC through a 100 K
Ω resistor (I
SNK
= 50 μA). Response Time = 1 msec.
Alarm Reset: Unlatches the relay when pulled to common while the input
frequency is in the release region.
Alarm Override: Causes the SW-100 to unconditionally release the relay
when pulled to common.
6. RELAY CONTACT OUTPUT: FORM “C” (SPDT) contacts max. rating.
5 A @ 120/240 VAC or 28 VDC (resistive load), 1/8 H.P. @ 120 VAC
(inductive load). The operate time is 5 msec nominal and the release time is
3 msec nominal.
7. RELAY LIFE EXPECTANCY: 100,000 cycles at max. rating. (As load
level decreases, life expectancy increases.)
8. ACCURACY:
±0.1% of the trip frequency setting.
9. INPUT IMPEDANCE: 33 K
Ω min. with the sink and source DIP switches
in the OFF positions.
10. MINIMUM RESPONSE TIME: From 5 msec. +1 period to 10 sec. +1
period in ten steps (excluding relay operate time).
11. HYSTERESIS AND OFFSET: From 0.25% to 33.33% of Trip Frequency
in nine steps. Hysteresis and/or Offset can also be set to 0 (Disabled).
12. INPUT AND POWER CONNECTIONS: Screw in terminal blocks
13. ISOLATION BREAKDOWN VOLTAGE (Dielectric Withstand):
2200 V between power & input, and power & output; 500 V between input
& output for 1 minute.
14. CERTIFICATIONS AND COMPLIANCES:
SAFETY
UL Recognized Component, File #E137808, UL508, CSA 22.2 No. 14
Recognized to U.S. and Canadian requirements under the Component
Recognition Program of Underwriters Laboratories, Inc.
IECEE CB Scheme Test Certificate # UL1683A-176645/USA,
CB Scheme Test Report # 97ME50135-042297
Issued by Underwriters Laboratories, Inc.
IEC 61010-1, EN 61010-1: Safety requirements for electrical
equipment for measurement, control, and laboratory use, Part 1.
ELECTROMAGNETIC COMPATIBILITY
Notes:
1. This device was designed for installation in an enclosure. To avoid
electrostatic discharge, precautions should be taken when the device is
mounted outside an enclosure. When working in an enclosure (ex. making
adjustments, setting switches, etc.) typical anti-static precautions should
be observed before touching the unit.
2. For operation without loss of performance:
Unit is mounted on a rail in a metal enclosure (Buckeye SM7013-0 or
equivalent) and I/O cables are routed in metal conduit connected to
earth ground.
Refer to the EMC Installation Guidelines section of this bulletin for
additional information.
15. ENVIRONMENTAL CONDITIONS:
Operating Temperature: 0 to 50°C
Storage Temperature: -40 to 80°C
Operating and Storage Humidity: 85% max. (non-condensing) from 0°C to
50°C.
Altitude: Up to 2000 meters
16. CONSTRUCTION: Case body is black, high impact plastic. Installation
Category II, Pollution Degree 2
17. WEIGHT: 6 oz. (0.17 Kg)
Level 3; 8 Kv air
Power frequency magnetic fields
Immunity to EN 50082-2
EN 61000-4-8
Level 4; 30 A/m
Electrostatic discharge
EN 61000-4-2
Level 2; 4 Kv contact
1
Electromagnetic RF fields
EN 61000-4-3
Level 3; 10 V/m
2
80 MHz - 1 GHz
Fast transients (burst)
EN 61000-4-4
Level 4; 2 Kv I/O
Level 3; 2 Kv power
RF conducted interference
EN 61000-4-6
Level 3; 10 V/rms
150 KHz - 80 MHz
Emissions to EN 50081-2
RF interference
EN 55011
Enclosure class A
Power mains class A
DC VERSION
12
10
INPUT
(GREEN)
RELAY
(RED)
+5V
INPUT LED
RELAY LED
S4
S5
S6
S7
MODE
CFG2
CFG1
CFG0
BCD
SWITCH
BCD
INPUTS
PUSH
BUTTON
BUTTON
INPUT
DIP
SWITCH
INPUTS
PROCESS
CIRCUITRY
8
7
9
S3
SINK
3.9K
1K
S1
SRC
+
-
10.0K
0.1µf
470pf
33.2K
8.06K
54.9K
392K
10K
S2
LOGIC
+12V
+5V
+5V
+12V
+12V
INPUT
SIGNAL
9 to 32 VDC
1 N.O.
COMM.
2
3
N.C.
+12V
POWER
SUPPLY
4
6
+5V
+5V
ALARM
OVERRIDE
ALARM
RESET
SUPPLY
12 VDC
SIGNAL
INPUT
COMMON
ALARM
OVERRIDE
ALARM
RESET
SENSOR
INPUT
PUSH
SWITCHING
CIRCUIT
DC
(60 mA)
10K
10K
100K
100K
0.1µf
0.1µf
(AC VERSION ONLY)
+
-
RELAY
BLOCK DIAGRAM
2