Sw-100, Din-rail speed switch, Description – Dynalco SW-100 Speed Switch User Manual
Page 2: Safety summary, Specifications, Dimensions in inches (mm)
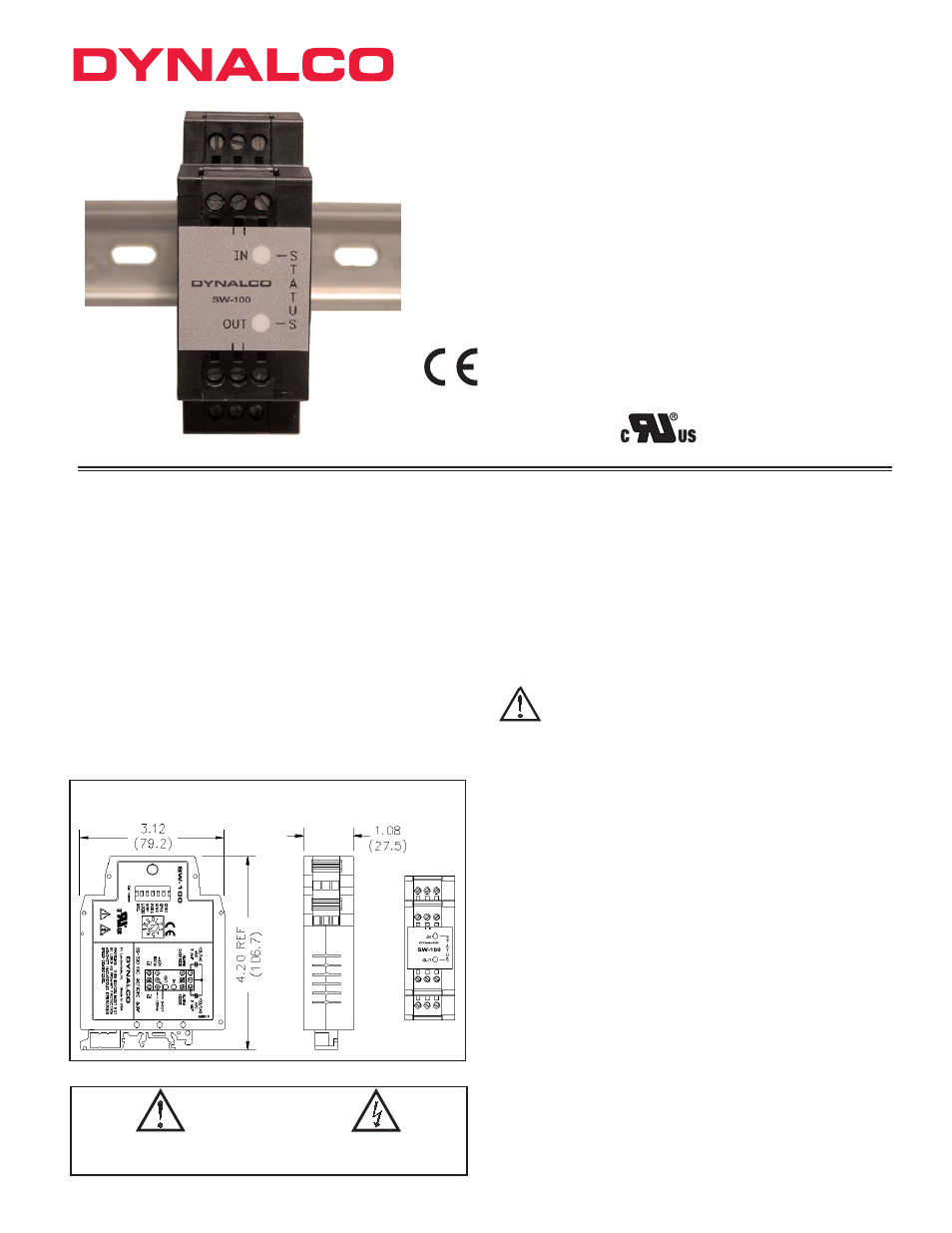
1
z
z
Simple on-line trip frequency setting (using actual
input signal or frequency generator)
z
z
User settable trip frquency from 0.1 Hz to 25 KHz
z
z
Over-speed, under-speed, and zero-speed detection
z
z
Relay latching, alarm override, and alarm reset
functions
z
z
Programmable input circuit accepts outputs from a
variety of sensors
z
z
Hysteresis and offset functions available
z
z
9 to 32 VDC input power
z
z
Input and relay status indication LED’s
SW-100
DIN-RAIL SPEED SWITCH
DESCRIPTION
The SW-100 accepts a frequency input, and controls a single relay (SPDT)
based on the value of the input frequency. The Trip frequency can be set to any
value from 0.1 Hz to 25 KHz. The SW-100 can be set to trip on overspeed, or
underspeed (including zero speed). Offset and hysteresis values can be
incorporated into the trip setting to eliminate output chatter. LED indicators for
both the Input signal and the Relay status are provided. Two separate input
connections for external push-buttons are also provided. One external input
overrides the trip detection function, and holds the relay in the release state as
long as the input is pulled to common. The other external input clears a latched
trip condition when pulled to common.
The SW-100 utilizes a seven position DIP switch, a rotary switch, a push-
button and two indication LEDs to accomplish input circuit configuration,
operational parameter set-up, input signal, and relay status indication. The input
circuitry is DIP switch selectable for a variety of sources.
The indication LEDs are used during normal operation to display the input
signal and relay status of the SW-100. These LEDs are also used to provide
visual feedback to the user of the current parameter settings during parameter
set-up.
The SW-100 operates in one of six output modes, as selected by the user. The
programmable Minimum Response Time provides optimum response vs. input
filtering for any input frequency. The offset and hysteresis settings provide
flexible adjustment of the relay trip and release points.
The unit is equipped with a universal mounting foot for attachment to
standard DIN style mounting rails, including top hat profile rail according to EN
50 022 - 35 x 7.5 and 35 x 15, and G profile rail according to EN 50 035 - G32.
SAFETY SUMMARY
All safety related regulations, local codes and instructions that appear in the
manual or on equipment must be observed to ensure personal safety and to
prevent damage to either the instrument or equipment connected to it. If
equipment is used in a manner not specified by the manufacturer, the protection
provided by the equipment may be impaired.
WARNING: SPEED SWITCHES MUST NEVER BE USED AS
PRIMARY PROTECTION AGAINST HAZARDOUS OPERATING
CONDITIONS. Machinery must first be made safe by inherent design,
or the installation of guards, shields, or other devices to protect personnel in
the event of a hazardous machine speed condition. The speed switch may be
installed to help prevent the machine from entering the unsafe speed.
SPECIFICATIONS
1. POWER:
DC Power: 9 to 32 VDC; 2.0 W
Power Up Current: Ip = 600 mA for 50 msec max.
2. OPERATING FREQUENCY RANGE: 0 Hz to 25 KHz
3. SIGNAL INPUT: DIP switch selectable to accept signals from a variety of
sources, including switch contacts, outputs from CMOS or TTL circuits,
and magnetic pickups.
Current Sourcing: Internal 1 K
Ω pull-down resistor for sensors with current
sourcing output. (Max. sensor output current = 24 mA @ 24 V output.)
Current Sinking: Internal 3.9 K
Ω pull-up resistor for sensors with current
sinking output. (Max. sensor current = 3 mA.)
Low Bias: Input trigger levers V
IL
= 0.25 V, V
IH
= 0.75 V; for increased
sensitivity when used with magnetic pickups.
Hi Bias: Input trigger levels V
IL
= 2.5 V, V
IH
= 3.0 V; for logic level signals.
Max. Input Signal: ±90 V; 2.75 mA max. (with both Current Sourcing and
Current Sinking resistors switched off).
DIMENSIONS In inches (mm)
UL Recognized Component,
File # E137808
CAUTION: Risk of Danger.
Read complete instructions prior to
installation and operation of the unit.
CAUTION: Risk of electric shock. P/N #: 145F-12810.R2.072309