Exide Technologies Section 92.80 User Manual
Page 15
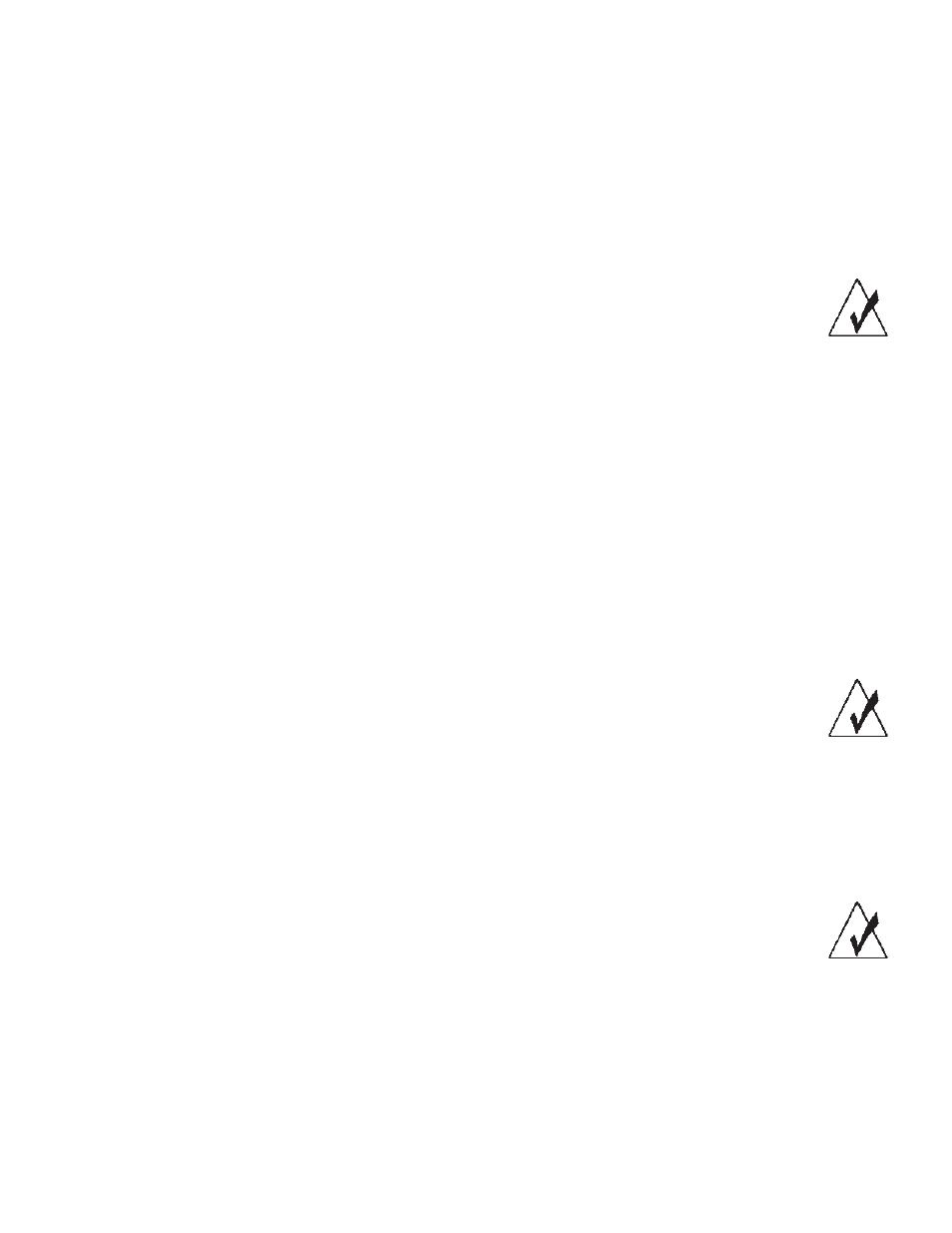
Also measure the total open circuit voltage from terminal plate to
terminal plate. This should be approximately equal to 2.14 volts
times the number of cells in the system, e.g., a 24 cell system
would read: 24 x 2.14v = 51.4 volts. An incorrect voltage reading
may mean connectors were installed incorrectly.
9.6 Connection Resistance
Electrical integrity of connections can be objectively established
by measuring the resistance of each connection. These resis-
tances are typically in the microhm range. Meters are available
which determine connection resistance in microhms. Be sure
that the probes are touching only the posts to ensure that the
contact resistance of connector to post is included in the
reading.
Resistance measurements or microhm measurements should
be taken at the time of installation and annually thereafter. Initial
measurements at installation become the benchmark values
and should be recorded for future monitoring of electrical
integrity.
It is important that the benchmark value for all similar connec-
tions be no greater than 10% over the average. If any connection
resistance exceeds the average by more than 10%, the connec-
tion should be remade so that an acceptable benchmark value
is established.
Benchmark values for connection resistances should also be
established for terminal plates, where used, as well as cable
connections. Benchmark values should preferably be estab-
lished upon installation.
All benchmark values should be recorded. Annually, all connec-
tion resistances should be re-measured. Any connection which
has a resistance value 20% above its benchmark value should
be corrected.
SECTION 10: IDENTIFICATION LABELS
10.0
Surfaces
Make sure surfaces are free of dirt and grease by wiping with
clean, dry wipers (isopropyl alcohol may be used) to ensure
proper label adhesion.
10.1
Cell Numerals
A
set
of
pressure
sensitive
cell
numerals
and
system
polarity labels are supplied and should be applied at this time. Cell
numerals should be applied to the cell being identified. Designate
the positive terminal cell as #1 with succeeding cells in series in
ascending order.
10.2
System Polarity Labels
The system polarity labels should be applied next to the positive
and negative system terminals.
10.3
Warning Label
Apply pressure sensitive warning label provided on a promi-
nently visible module side or end.
10.4
Battery Nameplate
For
future
reference
and
warranty
protection,
apply
pressure sensitive nameplate on a prominently visible module.
Fill in date of installation and the specified capacity and rate.
SECTION 11: PROTECTIVE MODULE COVERS
11.0 General
Each module is provided with a transparent protective cover to help
prevent accidental contact with live electrical connections, and to
provide easy visual access to the system.
When all system assembly has been completed, as well as ini-
tial testing, including initial charge and cell float voltage read-
ings, all covers should be installed. Covers should remain in
place at all times during normal operation of the battery system.
11.1
Module Clear Cover Installation
Refer to Figure 21 for Module Clear Cover installation. Install
standoff legs and standoff keys first, as shown.
The cover is then installed by grasping it so that the GNB logo is
upright. Locate slots at bottom of cover to the bottom standoff
legs and slide in place. Locate holes at top of cover and install to
top standoff legs. Refer to Figure 21.
SECTION 12: BATTERY CHARGING
12.0
Initial Charge
Batteries lose some charge during shipment as well as during
the period prior to installation. A battery should be installed and
given its initial charge as soon after receipt as possible. Battery
positive (+) terminal should be connected to charger positive (+)
terminal and battery negative (-) terminal to charger negative
(-) terminal.
Failure to perform the initial charge within the
time limits stated in section 4.2 will affect the performance
and life of the battery and may void the warranty.
12.1
Constant Voltage Method
Constant voltage is the only charging method allowed. Most
modern chargers are of the constant voltage type. Determine the
maximum voltage that may be applied to the system equipment.
This voltage, divided by the number of cells connected in series,
will establish the maximum volts per cell (VPC) that is available.
Table C lists recommended voltages and charge times for the
initial charge. Select the highest voltage the system allows to
perform the initial charge in the shortest time period.
Temperature Correction of Charger Voltage
V corrected = V25°C - ((T actual -25°C) x (.0055 V/°C))
15