Weller WQB2000 User Manual
Page 6
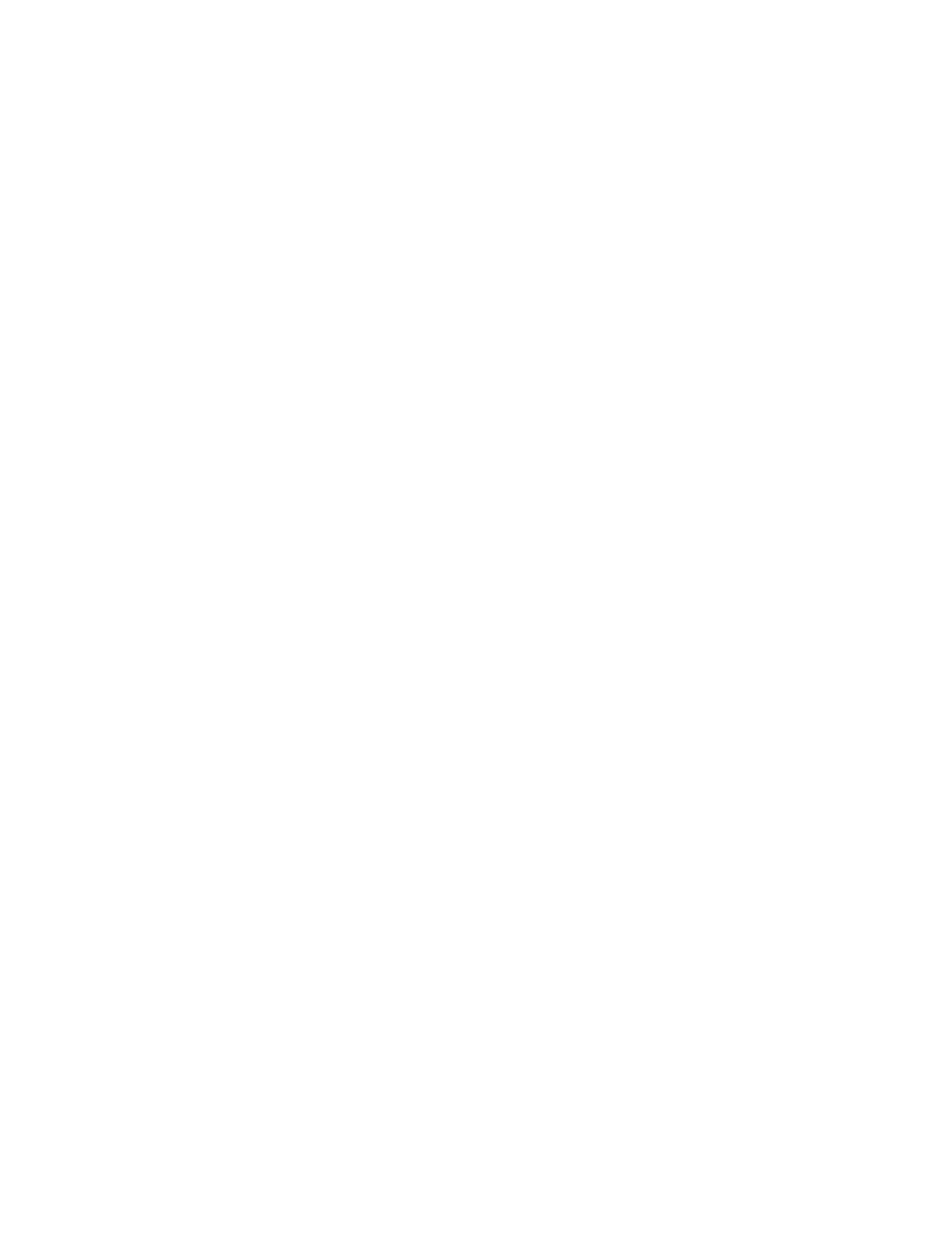
6
ALIGNMENT METHOD - COMPONENT TO CIRCUIT BOARD
1.
Return the circuit board to the registration pins; seat board to pin shoulders, level board with spacer blocks and standoff pins. Place the
part on the template (see Figure 5) be sure to use the manual vacuum pen provided for QFP parts. Be sure to check two opposite
corners on leaded parts for correct engagement of leads in template depressions. BGA parts can be checked by looking for uniform
clearance between the component and the template edges on four sides. Both QFP and BGA components will nest in the templates and
will not slide out of the depressions when properly aligned.
2.
Position component pick-up nozzle in the center of the table by moving the horizontal slide to middle position over component. Lower the
complaint nozzle and pick up the part. Raise the nozzle to maximum height. Avoid touching component during all of the following steps.
ALIGNMENT METHOD - STENCIL TO CIRCUIT BOARD
1.
Position the stencil pick-up nozzle in the center of the table by moving the horizontal slide to left-hand position. Place the solder stencil
onto the template (see Figure 5) engaging the tabs and notches. Lower the stencil nozzle and pick up the stencil. Raise the nozzle to
maximum height.
2.
Remove the circuit board with the template from the registration pins and replace with the board that will receive the solder paste and/or
component (Do not use clear test board with adhesive for solder stenciling practice or training).
CAUTION:
Follow all of the manufacturers recommendations and heed all warnings when handling solder paste. The use of latex
protective gloves is recommended.
NOTE:
Due to limited shelf life, solder paste is not included with the WQB2000. We recommend using a SN63 or SN62 (2% Ag) alloy
with RMA flux for best results.
3.
Lower the stencil to the surface of the circuit board, apply positive downward pressure 2-3 lbs., and lock stencil slide in down position
with cam lock (see Figure 1). Spread solder paste over stencil openings with spatula blade then squeegee paste into openings with
the edge of spatula blade. Work the paste into openings moving the spatula blade in opposite directions to assure that openings are
completely filled. Remove excessive solder paste from stencil surface leveling the paste in the openings to the top of the stencil.
Release cam lock and raise stencil to upper position. Examine solder paste print for full and complete pattern. The circuit board can be
removed from registration pins for inspection and returned for component placement.
NOTE:
If solder print is not complete or satisfactory, paste can be removed, the circuit board cleaned and then re-pasted. If the print is
off registration, then the stencil needs to be removed and the board with template returned and the stencil repositioned and
picked up as previously. Be sure the stencil is completely seated into the template tabs, any slight out-of-level will cause a shift
in the printing.
4.
Reposition the component over the solder pasted circuit board pattern, horizontal slide to right hand position. Lower component into
solder paste and slightly compress compliant nozzle to seat component leads or balls into paste. Release component by depressing
vacuum break button (see Figure 1) and then raise nozzle to upper position.
5.
The green test circuit board is now ready for re-flow. If using clear test boards the component and solder paste can be viewed from
both sides of the board for placement accuracy.
CAUTION: Do not try to reflow clear test boards, they will not withstand soldering temperatures.
Additional test boards may be solder printed and assembled by repeating the above steps. The number of boards that can be assembled without
cleaning the stencil will depend on the print quality required, the solder paste used, the room humidity and room temperature. When print quality
falls below acceptable levels the stencil must be cleaned using typical cleaning methods. If you are unfamiliar with cleaning methods or do not
have cleaning equipment, we recommend using a shallow depth of alcohol in a small container, immersing the stencil in the alcohol and brushing
the stencil inside and out with a small paint brush to loosen the solder paste from the stencil. Additional clean up can be accomplished by manually
wiping the stencil with a LINT FREE WIPE.
It is a good idea to do several dry runs before you apply paste to a test board. To check the placement accuracy, use a magnification aid. The
clear test board with clear adhesive provides am excellent means for operator training and as test of placement accuracy. It is a very useful tool
for practice and can be reused over and over. If the clear test board with adhesive is being used the component can be removed from the test
board by slowly lifting the component from the adhesive with a pointed probe starting from one corner. These clear boards are especially useful
when training for BGA placement accuracy, in that after the BGA is placed on the clear adhesive board, the board can be turned over and the
alignment of BGA balls can be easily viewed through the back of the clear board.
When ready to place components on your production or repair circuit boards review the positioning and stenciling steps above. If you only have
one production or prototype circuit board, follow the above steps until the stencil is lifted from the template, then remove the template from the
board and proceed with the remaining steps. The tape holding the template to the board can be released without damage to the template by sliding
the edge of a registration pin plate between the tape and the board.
You will find that the set-ups are quite simple, and you can EASILY obtain acceptable low volume placement rates.
MAINTENANCE
Check air filter weekly, drain if necessary.
Lubricate V bar felt wiper (see Figure 1) monthly.
Replace vacuum air filters yearly.
SUMMARY
We hope youll agree that the WQB2000 is everything we said it would be a truly remarkable product in terms of its accuracy and cost. As stated
before, it should give you years of satisfaction. If, however, you run into any problems, please dont hesitate to call the Weller factory for
technical support.