Weller WQB2000 User Manual
Wqb2000 qfp and bga repair and assembly system
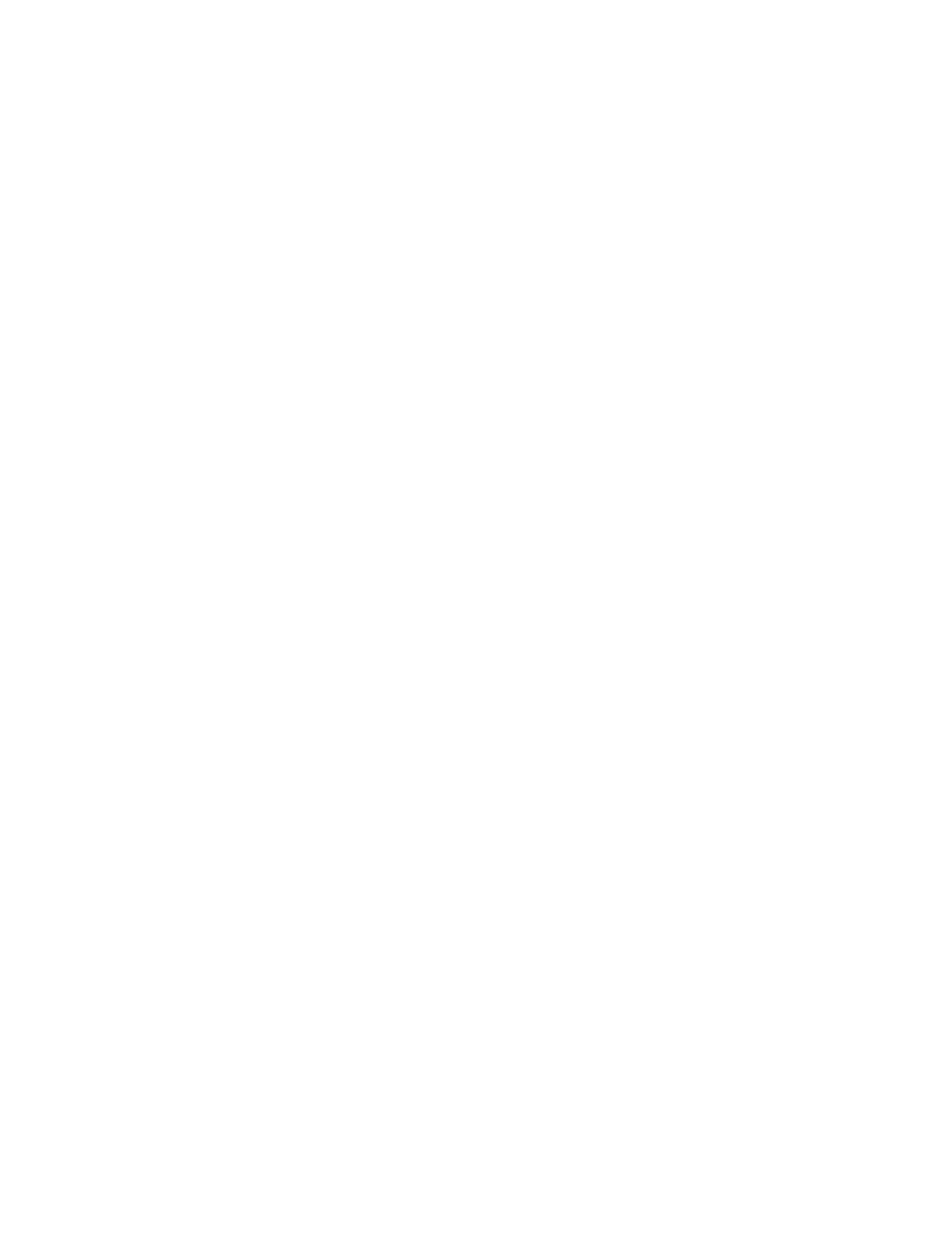
1
WQB2000 QFP AND BGA REPAIR AND ASSEMBLY SYSTEM
INTRODUCTION
Congratulations! Youve just purchased the most accurate and economical solder re-flow; solder paste printing and component placement machine
on the market! Weller, a company well known for its hand soldering and desoldering tools has developed the WQB2000 to meet a growing need
for accurate removal, solder printing and placement of fine pitch SMDs including BGA components, on prototype and low volume production
PCBs.
With the WQB2000, you will be able to remove fine pitch and ultra-fine pitch surface-mount devices and then screen-print and place these same
devices onto your PC boards with very high yields. The patented templates and solder printing stencils provide a simple, effective, accurate and
repeatable method of solder paste printing and placing of surface-mount devices.
WQB2000 - FEATURES
Requires shop air only 60 psi at 0.70 scfm
Quiet operation - less than 35 db(A) @ 1 meter
Air pressure on-off switch, regulator and gauge
Easy and flexible set-ups, will place components on boards up to
8" x 15"
Portable Vacuum pencil to aid in component pick-up and location
Compliant component vacuum pick-up nozzle
Stencil vacuum pick-up nozzle
Compact design - 12" x 18" footprint
One year limited warranty
Placement and removal of fine pitch components including BGAs
Soldering and desoldering of fine pitch components including BGAs
Temperature controlled hot air and radiant bottom heat
Timer with 20 user programmable cycles to control component/
board heat-up profile
Solder paste stenciling of individual components
Placement accuracy of 0.001"
Repeatability of 0.002" allowing for board to board variation
Patented, reusable templates and stencils
Test/Training Kit includes: 1 QFP and 1 BGA component, 2 clear test
boards, 2 copper test boards, templates, stencils, and hot air nozzle
for test components, plastic kit box
WARNING: This product, when used for soldering and similar applications, produces chemicals known to the State of
California to cause cancer and birth defects or other reproductive harm.
The unique features of this machine are its placement accuracy and repeatability. Its accuracy is achieved with precision ball slides and precision
vacuum nozzles, combined with the unique component templates and solder paste stencils. These components keep the placement accuracy
within 0.001".
DESCRIPTION OF MACHINE COMPONENTS
WQB-A HOT AIR UNIT
This unit provides electronic temperature controlled hot air or if desired hot inert gas (such as nitrogen).
The temperature is variable from 250°F to 1000°F. Oil and water free compressed air (30 - 100 psi) must be provided. To meet this requirement a
filter has been provided that will filter oil and water down to 2 PPM. However, as your filter removes oil and water contaminants from the air, the
filter may start to clog and you may notice a pressure drop on the machines air gauge. This may also indicate an air compressor failure. In the
event that the filter clogs call your distributor for a new one.
The hot air will be free of static charge. A static ground is provided at the front of the unit for this purpose.
The unit also provides vacuum source required for component removal during desoldering as well as a hot air flow control adjustment.
WQB-P HOT PLATE UNIT FOR CIRCUIT BOARD BOTTOM HEAT
This unit provides electronic temperature control of the low voltage radiant hot plate heater.
The analog temperature control is variable between 125°F to 825°F. Temperatures can be pre-set and then viewed in real time on a digital display
by switching from pre-set to actual on the selection slide switch provided.
The unit is provided with an external sensor connector for alternatively controlling the bottom temperature of the PC board directly. This sensor is
not included with the WQB2000.
A static ground connector is provided at the rear of the unit.
WQB-C TIMER FOR CYCLE CONTROL
Microprocessor control guarantees reproducible soldering or desoldering time cycles. Optimum results are achieved due to a three stage ramp-up
heating cycle followed by a cool down interval. The microprocessor can store process parameters for up to 10 user programmable cycles, which
can be called up for use or edited and re-stored. There are also 10 preprogrammed cycles in memory. As the Timer is controlling the soldering
process, the time to complete each stage is displayed on a digital count down timer.