Weller WQB2000 User Manual
Page 3
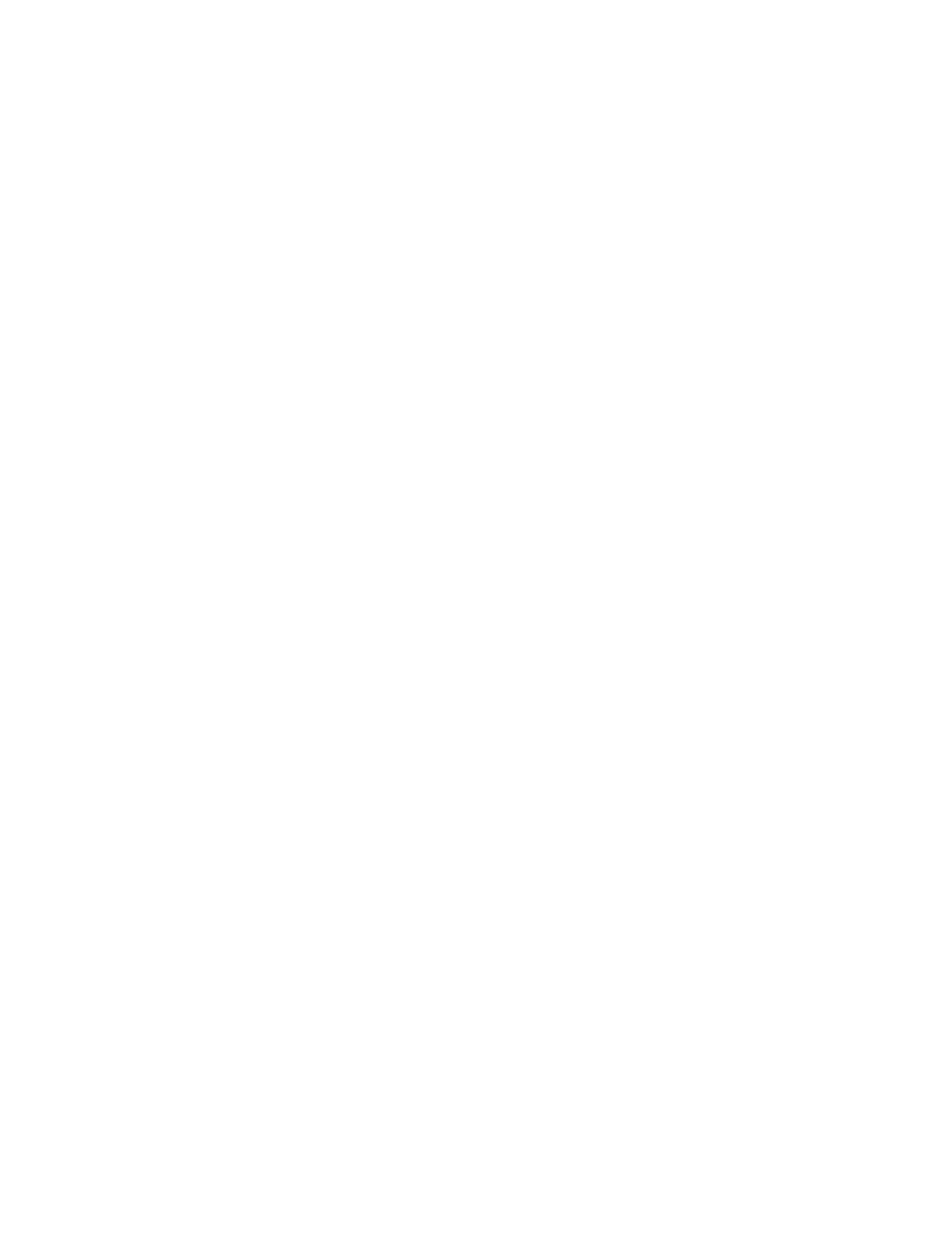
3
MACHINE OPERATION AND TEST
1. Turn on air supply with toggle switch at the top center of housing (see Figure 1). If no air pressure is evident, check air supply for
closed valves.
2. Adjust air regulator (see Figure 1) by pulling out the locking ring and turning the knob (clockwise to increase) until the gauge reads 60
psi. Push the locking ring back to lock the regulator.
3. Test both vacuum pick-ups for vacuum by placing your finger over the pick-up opening, vacuum should be evident. The vacuum levels
are fixed for each pick-up and can only be changed by adjusting the system air pressure. Adjust slide tension screws to prevent
nozzles from slipping down under their own weight when released.
CAUTION: Do not exceed 85 psi.
4. Test the component vacuum nozzle for component pick-up by placing a clear test board on the tabletop. Place a BGA component onto
the test board centered to the nozzle. Manually lower the nozzle until it makes contact with the component, slightly compress the
compliant nozzle and then lift. If the part does not lift, check to see if the nozzle has its O-ring seated at the tip. If it does, then the nozzle
will need to be checked and adjusted for to be square to the tabletop. (See note below)
The slides were adjusted to be perpendicular to the tabletop at the factory, and should not need re-adjustment. If you are having trouble
picking up components or stencils you need to check the perpendicularly and adjust if necessary, use the square provided.
NOTE:
Nozzle perpendicularly can be adjusted side-to-side by slightly loosening two screws on the vacuum pick-up bracket, square
nozzle by placing square provided on tabletop and aligning one side of nozzle to square then re-tighten screws. Front-to-back
squaring can be accomplished by loosening two mounting screws at rear of boom plate, then adjusting 4 leveling screws at
the top and bottom of the plate to square nozzle to table top. We recommend the front-to-back adjustment be made on the
stencil nozzle with the nozzle centered on the tabletop.
5. Test the vacuum break switch (see Figure 1) and component release by picking up the BGA part with the compliant nozzle. When the
slide is in its UP position (place your hand underneath the part to catch it as it falls), depress the vacuum break switch. The part should
fall off the moment you depress the switch. If it hangs or delays, reduce the vacuum by adjusting the air pressure regulator. Depending
on solder paste tackiness, a release delay should not affect the placement operation accuracy or acceptability.
One (1) roll of Kapton
®
tape
Tooling Square for slide alignment
Knife (Spatula) Handle
Spatula Blades (3)
MACHINE SETUP
1. Remove boxes from top of shipping carton and unpack components.
2. Remove machine from carton packing and place on solid table. We recommend setting the machine up at its permanent workstation,
preferably a static-safe (ESD) workstation. Unlock slides by loosening slide tension spring adjustment screw for each slide (two
screws on hot air nozzle slide).
3. Position WQB-A hot air power supply and WQB-P hot plate power supply to left side of machine; they can be stacked if desired. Position
timer to right side of machine. The location of the WQB-A must be to the left side of the machine platform; the other components can be
placed to suit the workbench layout.
4. Plug WQB-C TIMER connectors into sockets as indicated on connector bodies.
Connect 6-pin connector marked WQB-P to WQB-P 6-pin power supply connector in rear of unit.
Connect 7-pin connector marked WQB-A to WQB-A 7-pin power supply connector in rear of unit.
Connect 7-pin connector marked WQB-T to 7-pin connector in rear of machine table cabinet.
5. Plug rectangular radiant heater plate connector into WQB-P socket in front of unit.
6. Plug nozzle air temperature control nozzle sensor into REAR of WQB-A power supply.
CAUTION:
DO NOT PLUG NOZZLE SENSOR INTO FRONT OF WQB-P, if connected, the hot air nozzle temperature will
exceed the temperature control setting and component and/or board damage may occur.
7. Attach filter/air hose to the air input port, filter next to unit, a swivel fitting is provided so that the filter can be turned to
position the liquid bleed valve pointing downward.
NOTE:
Check the air filter and empty daily.
8. Connect the short air supply tube from the quick-connect fitting on the rear of the machine platform enclosure to the quick-
connect fitting on the rear of the WQB-A hot air power supply.
9. Screw the hot air heater into the nozzle manifold (see Figure 1). Plug the hot air connector into the WQB-A socket and screw locking
shell to connector. Attach clear air tubing for hot air heater to air port and black vacuum tubing to vacuum port. Plug static grounding plug
into socket provided. Attach black vacuum tube to component vacuum pick-up stem, route and secure tube so that it will not interfere
with nozzle slide travel. Adjust slide tension screws to prevent nozzle from slipping down under its own weight when released.
10. Remove nozzle by turning locking knob to left (see Figure 1). Check and seat red vacuum cup to the vacuum stem in the nozzle
manifold and then re-attach the hot air nozzle to the quick mount connector by sliding the nozzle up over the vacuum cup, aligning the
nozzle mount and the connector keys and locking the nozzle mount into the connector by turning the locking handle to the right.
11. Attach retractable air hose to shop air.
12. Connect WQB-P and WQB-A to 120VAC power supply.
Your machine is now ready for operation!