1 dismantling the slide-in unit, 4 dismantling the drive unit oil bath lubrication, Dismantling the slide-in unit – Richter MNK Series User Manual
Page 17: Lubrication, Grease lubrication, Dismantling the drive unit oil bath lubrication17, Series mnk
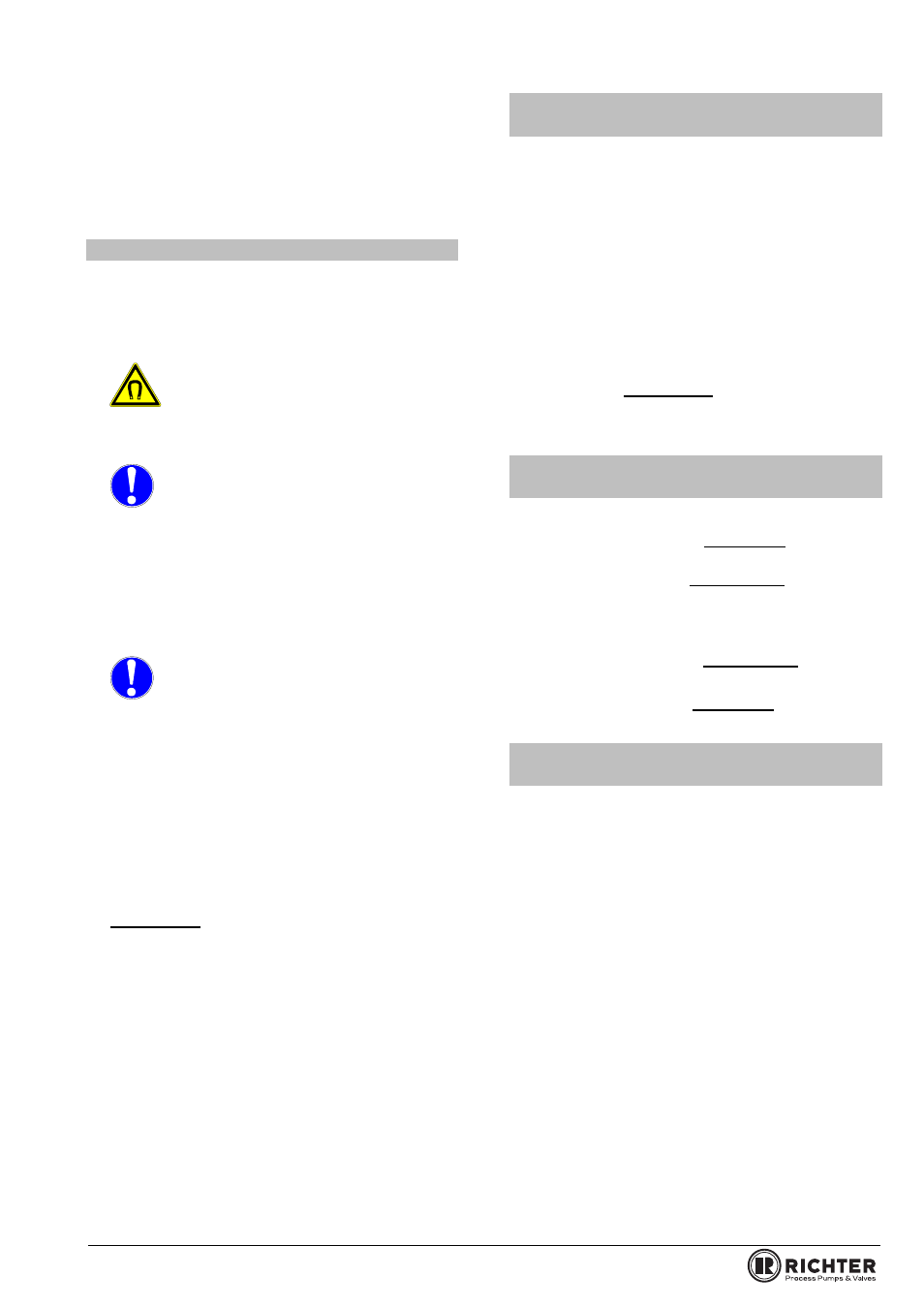
Series MNK
Page 17
9230-050-en
Revision 11
TM 7903
Edition 07/2010
Axial forces
are produced when the plain bearing
pedestal is pulled out of the bearing pedestal. These
forces diminish again abruptly after it has been
removed.
The operating torque of the magnetic coupling
installed is specified on the
type plate
.
7.6.1 Dismantling the slide-in unit
Secure slide-in unit on the work bench or a work
top.
Pull the plain bearing pedestal
339
out of the
bearing pedestal.
Caution!
Magnetic forces!
Risk of accident !
If necessary loosen the centering of the plain
bearing pedestal using a rust dissolver and levers.
It is imperative to use clamping jaws with
a rubber surface.
Clamp the plain bearing pedestal
339
with the
sealing surfaces in a vice.
Undo the impeller
230
and inner magnet
assembly
859
with a strap wrench.
Right-hand
thread !
Pull parts out of the plain bearing pedestal
339
or
off the pump shaft
211
.
Make sure that no parts of the plain
bearing fall. Silicon carbide is easy to
break.
Keep bearing sleeves
529
and bearing bushes
545
in pairs which belong together.
Clamp pump shaft
211
with the flat pivot point in a
vice. Use
smooth clamping jaws
.
Undo impeller
230
or inner magnet assembly
859
(depending on which part has remained on the
pump shaft).
If the bearing bushes
545
have to be removed
from the plain bearing pedestal, a Richter jig is
best suited for this purpose. See assembly aids in
Section 10.3
.
To dismantle the can
159
, can insert
158
,
intermediate ring
509
and support ring
518,
loosen the centering of the support ring
518
on
the side recesses in the bearing pedestal
330
.
Pull parts out of the bearing pedestal
330
.
Only separate can
159
and can insert
158
if one
part has to be replaced. If separation is not
possible, the unit must be cooled to approx. 5 °C.
In the case of a vacuum-proof design the can
insert is glued to the can. Separation is not
possible without destroying the can.
In the case of a can with a can monitor using a
flexible p.c. board, dismantling is possible. We
recommend you, to have the reassembly be
performed at the manufacturer's.
7.6.2 Dismantling the drive unit
Long life grease lubrication
Remove circlip
932/3
on the motor side.
Remove rear bearing cover
361
. Use groove for
dismantling.
Remove circlip
932/2
.
Press drive shaft
213
with drive magnet assembly
858
out of the bearing pedestal.
Remove radial ball bearings
321/1
.
Remove second circlip
932/1
.
Remove distance sleeve
525
and second radial
ball bearing
321/2
.
Dismantling can be checked using the sectional
drawing in
Section 9.2
and the components
available.
7.6.3 Changing the radial ball bearings
Long life grease lubrication
To change the radial ball bearings
321,
perform
dismantling as described in
Section 7.6
.
Pull the plain bearing pedestal
339
out of the
bearing pedestal. See
Section 7.6.1
.
The plain bearing pedestal with impeller, inner
magnet assembly and pump shaft need not be
dismantled.
The rest dismantheling see
Section 7.6.2
.
Change radial ball bearings
321
.
Assembly as described in
Section 7.8
.
7.6.4 Dismantling the drive unit
Oil bath lubrication
Remove hex. screw
901/4
and drain oil.
Remove hex. socket screw
914/1
with spring
washer
934/2
for the bearing cover. For this
purpose assembly bores are provided in the drive
shaft
213
for a hex. socket screw key.
Remove circlip
932/3
on the motor side.
Remove rear bearing cover
361
with shaft seal
421/1
and O-ring
412/1
. Use groove for
dismantling.
Remove circlip
932/2
.
Press the drive shaft
213
with drive magnet
assembly
858
out of the bearing pedestal.
Remove radial ball bearings
321/2
from the
bearing pedestal.
Remove circlip
932/1
.
Remove distance sleeve
525
, radial ball bearings
321/1
, O-ring
412/5
and bearing cover
360
using
an extractor.
Dismantle drive magnet assembly
858
and drive
shaft
213
.