Watts M1115-2 User Manual
Page 7
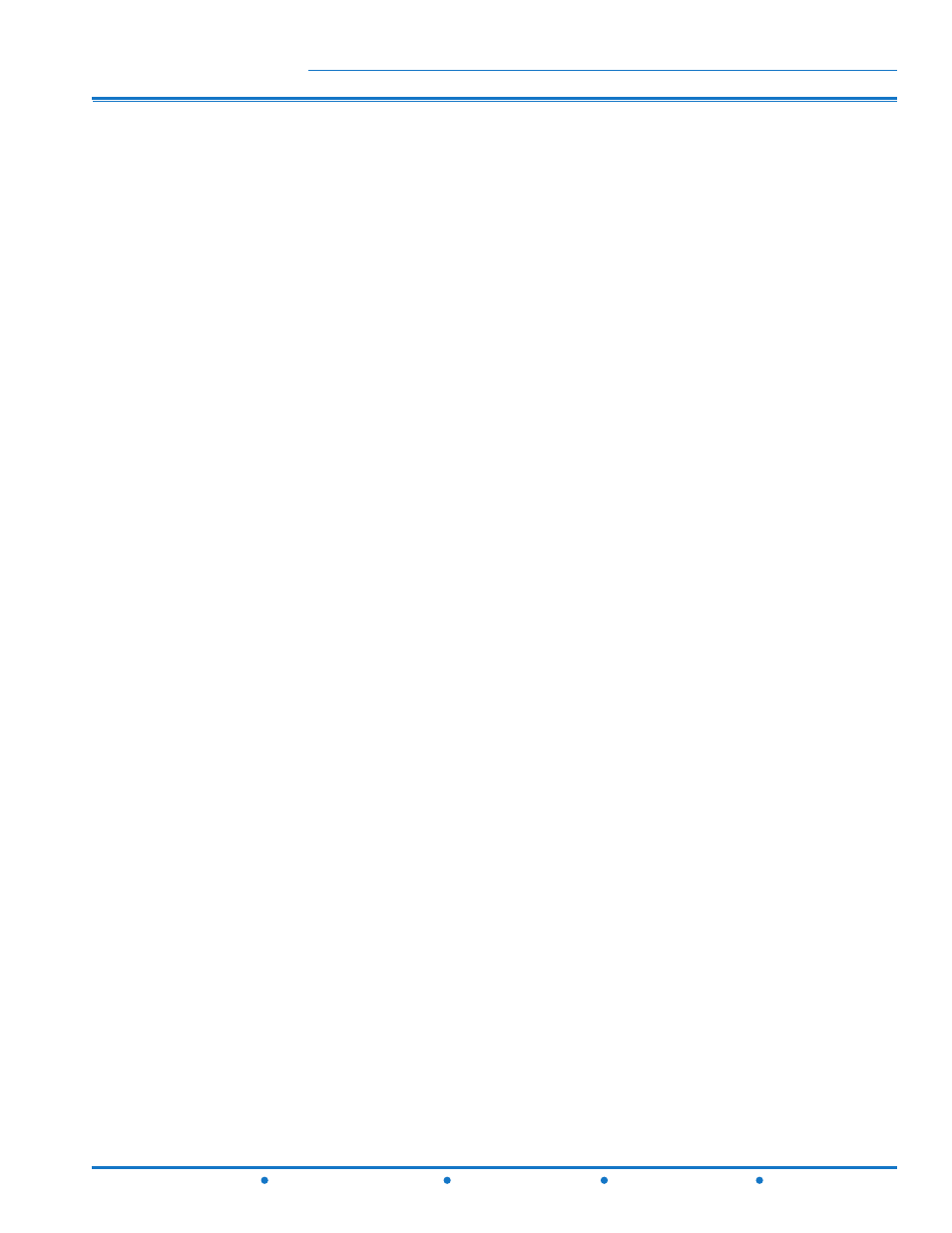
12541 Gulf Freeway
•
Houston, Texas 77034
•
(Ph) 713.943.0688
•
(Fx) 713.944.9445
•
www.watts.com
M
ustang
s
eries
M115-2 (Globe)
M1115-2 (Angle)
Installations
Start-Up
• Prior to installation, flush line to remove debris.
• Install valve horizontally “in line” (cover facing up), so flow arrow matches flow through the line. Avoid
installing valves 6” and larger vertically. Consult factory prior to ordering if installation is other than de-
scribed.
• Install inlet and outlet isolation valves.
NOTE: When using butterfly valves, insure disc does not contact
control valve. Damage or improper valve seating may occur.
• Provide adequate clearance for valve servicing and maintenance.
• Install pressure gauges to monitor valve inlet and outlet pressure.
• If installation is subjected to very low flow or potentially static conditions, it is recommended a pressure
relief valve (1/2” minimum) be installed downstream of the Pressure Reducing Valve for additional system
protection.
Proper Automatic Control Valve start-up requires bringing the valve into service in a controlled manner. All
adjustments to control pilots and speed controls should be made slowly, allowing the valve to respond and the
system to stabilize.
NOTE: Control Valves should be set‑up in a dynamic (flowing) condition for proper
start‑up. Provisions for flow must be made to insure proper settings.
• For proper valve set-up upstream pressure must be manually lowered to desired sustaining setpoint.
1. Close upstream and downstream valves to isolate the valve from line pressure. Release spring tension
on Pressure Reducing and Sustaining Controls by turning adjustment screws out (counterclockwise),
decreasing setpoints. Open all Isolation Ball Valves, if so equipped. If valve is fitted with adjustable speed
controls, turn needle(s) in (clockwise) until seated, and return out (counterclockwise) 1-1/2 to 2-1/2 turns.
These are approximate settings, and should be fine tuned to suit system requirements after pressure
adjustments have been made.
2. Slowly open upstream isolation valve to allow controlled filling of the valve. Vent entrapped air by carefully
loosening control tubing or pipe plug at the highest point possible. If valve is equipped with a Position
Indicator, open Air Bleed Petcock to vent air. Water will be milky in appearance and will begin to clear as
air is vented. Carefully loosen enough cover screws on control pilot(s) to vent entrapped air. Re-tighten
when water vents clearly.
3. Setting Reducing Control: Slowly open downstream isolation valve. Gradually turn adjustment screw on
the Pressure Reducing Control in (clockwise) to raise downstream pressure. Allow valve and system to
stabilize. Observe inlet and outlet pressure gauges. Continue to adjust as needed, pausing approximately
every 1
‑1/2 turns, allowing valve and system to stabilize. Turning adjustment screw clockwise raises outlet
pressure. Turning adjustment screw counterclockwise lowers outlet pressure. When desired downstream
pressure is reached, tighten locknut on adjustment screw.
4. Setting Sustaining Control: Partially close upstream isolation valve, lowering valve inlet pressure, until
upstream pressure gauge is at desired sustained setpoint. While observing upstream pressure gauge (or
Position Indicator), slowly turn Pressure Sustaining Control adjustment screw clockwise until upstream
pressure begins to rise. The Sustaining Pilot is set at the point the valve begins to close, raising upstream
pressure. Tighten locknut on adjustment screw. Fully open upstream isolation valve.
5. Fine tune Speed Controls to suit system requirements. Adjust Closing Speed Control (if equipped)
clockwise for slower closure, and counterclockwise for faster closure. Adjust Opening Speed Control (if
equipped) clockwise for slower opening, and counterclockwise for faster opening.
910 Ops & Inst