Watts R14-06-1111000 User Manual
Page 7
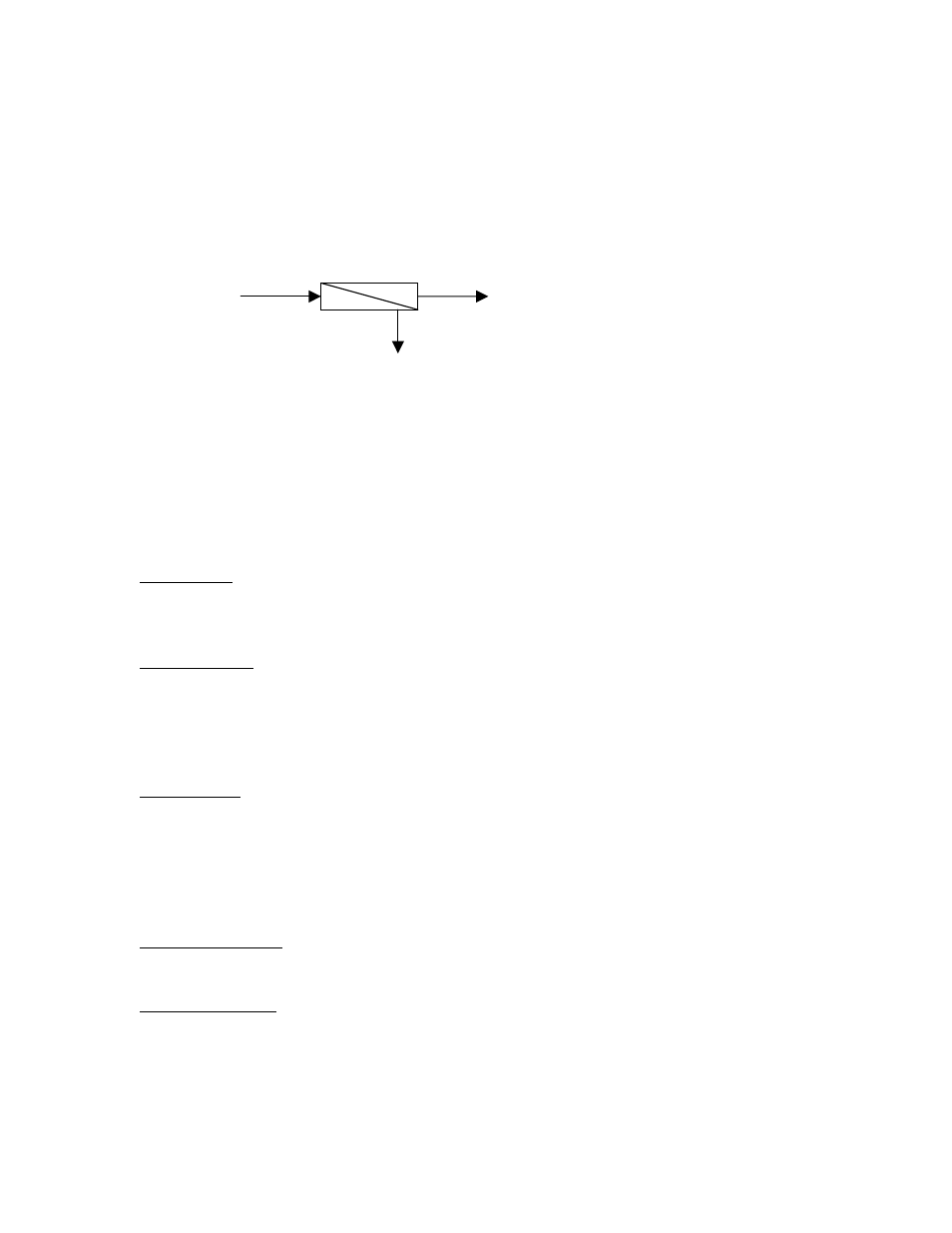
B. RO OVERVIEW
Reverse osmosis systems utilize semipermeable membrane elements to separate the feed
water into two streams. The pressurized feed water is separated into purified (product) water
and concentrate (reject) water. The impurities contained in the feed water are carried to drain
by the reject water.
RO Membrane
Feed Water Product Water
Reject Water
C. PRETREATMENT
The RO feed water must be pretreated in order to prevent membrane damage and/or fouling.
Proper pretreatment is essential for reliable operation of any RO system.
Pretreatment requirements vary depending on the nature of the feed water. Pretreatment
equipment is sold seperatly. The most common forms of pretreatment are described below.
Media Filter - Used to remove large suspended solids (sediment) from the feed water.
Backwashing the media removes the trapped particles. Backwash can be initiated by time or
differential pressure.
Water Softener - Used to remove calcium and magnesium from the feed water in order to
prevent hardness scaling. The potential for hardness scaling is predicted by the Langelier
Saturation Index (LSI). The LSI should be zero or negative throughout the unit unless
approved anti-scalents are used. Softening is the preferred method of controlling hardness
scale.
Carbon Filter - Used to remove chlorine and organics from the feed water. Free chlorine will
cause rapid irreversible damage to the membranes.
The residual free chlorine present in most municipal water supplies will damage the thin film
composite structure of the membranes used in this unit. Carbon filtration or sodium bisulfite
injection should be used to completely remove the free chlorine residual.
Chemical Injection - Typically used to feed antiscalant, coagulant, or bisulfite into the feed
water or to adjust the feed water pH.
Prefilter Cartridge - Used to remove smaller suspended solids and trap any particles that may
be generated by the other pretreatment. The cartridge(s) should be replaced when the
pressure drop across the housing increases 5 - 10 psig over the clean cartridge pressure drop.
The effect of suspended solids is measured by the silt density index (SDI) test. An SDI of
five (5) or less is specified by most membrane manufacturers and three (3) or less is