Bryant GAS-FIRED INDUCED-COMBUSTION FURNACE 393AAV User Manual
Page 3
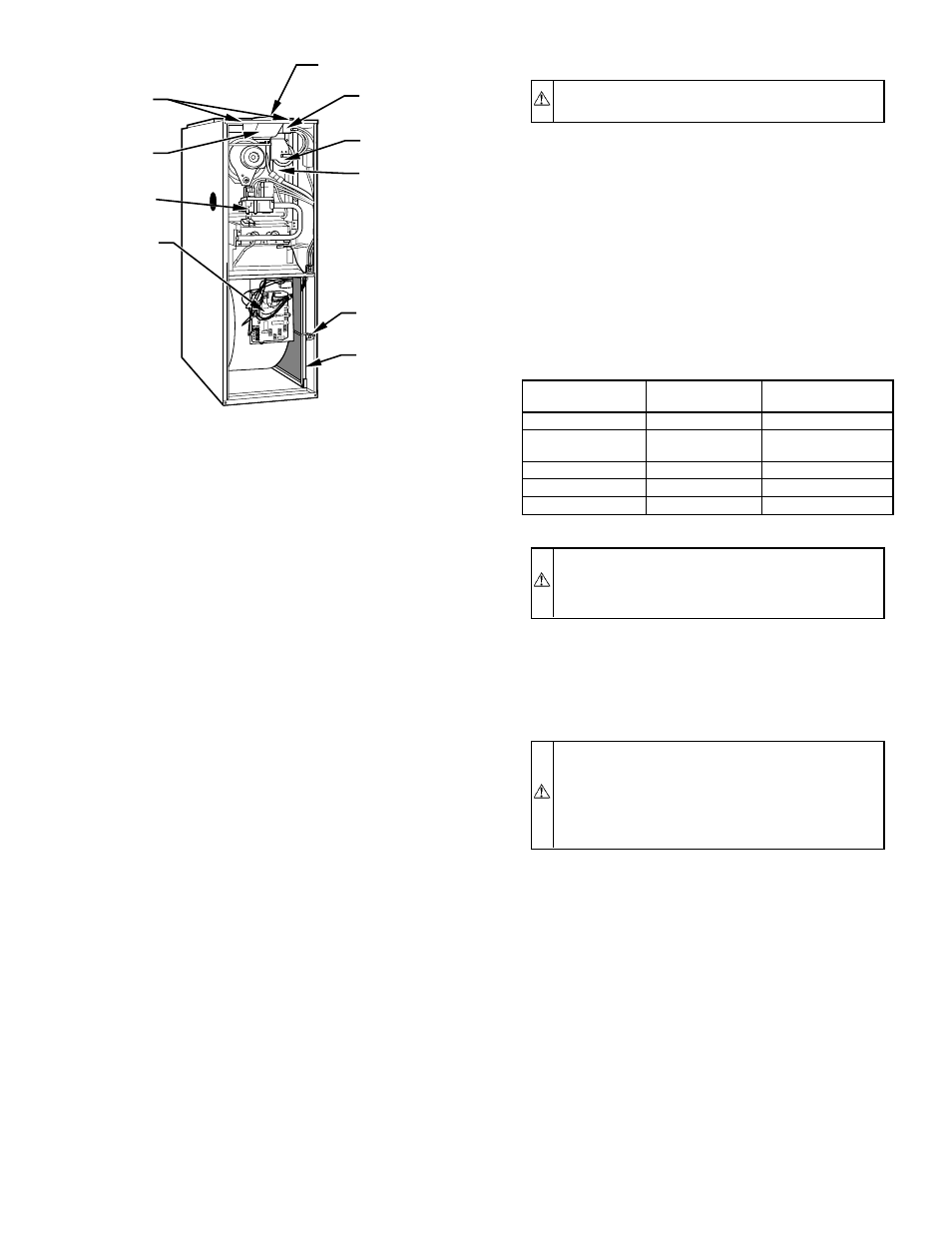
To ensure long life, economy, and high efficiency, clean accumu-
lated dirt and grease from blower wheel and motor annually.
The inducer and blower motors are pre-lubricated and require no
additional lubrication. These motors can be identified by the
absence of oil ports on each end of the motor.
Clean blower motor and wheel as follows:
1. Turn off electrical supply to furnace.
2. Remove control and blower access doors.
3. Disconnect blower leads from furnace control. Note wire
color and location for reassembly.
All other factory wires can be left connected, but field
thermostat connections may need to be disconnected de-
pending on their length and routing.
4. Remove 2 screws securing control and transformer support
to furnace.
5. Hang control and transformer support to side of furnace
casing.
6. Remove screws holding blower assembly to blower deck
and slide blower assembly out of furnace.
7. Clean blower wheel and motor using a vacuum with soft
brush attachment. Do not remove or disturb balance weights
(clips) on blower wheel blades. The blower wheel should
not be dropped or bent as balance will be affected.
8. If greasy residue is present on blower wheel, remove wheel
from the blower housing and wash it with an appropriate
degreaser. To remove wheel:
a. Mark blower wheel location on shaft before disassembly
to ensure proper reassembly.
b. Loosen setscrew holding blower wheel on motor shaft.
NOTE:
Mark blower mounting arms, motor, and blower housing
so motor and each arm is positioned at the same location during
reassembly.
c. Mark blower wheel orientation and cutoff plate location
to ensure proper reassembly.
d. Remove screws securing cutoff plate and remove cutoff
plate from housing.
e. Remove bolts holding motor and motor mounts to
blower housing and slide motor and mounts out of
housing. Disconnect capacitor and ground wire attached
to blower housing before removing motor. Motor mount
belly band need not be removed unless motor is to be
replaced.
f. Remove blower wheel from housing.
CAUTION:
The blower wheel should not be dropped or
bent as balance will be affected.
9. Reassemble motor and blower by reversing items 9a
through 9f. Be sure to reattach ground wire.
10. Reinstall blower assembly in furnace.
11. Reinstall control and transformer support assembly in
furnace.
12. Reconnect blower leads to furnace control.
Refer to furnace wiring diagram and connect thermostat
leads if previously disconnected. (See Fig. 7.)
NOTE:
Refer to Table 2 for motor speed lead relocation if leads
were not identified before disconnection.
CAUTION:
Heating air speed selection MUST be ad-
justed to provide proper air temperature rise as specified
on the rating plate. Failure to adjust the heating speed
may shorten heat exchanger life.
13. Turn on electrical supply. Manually close blower access
door switch. Use a piece of tape to hold switch closed.
Check for proper rotation and speed changes between
heating and cooling by jumpering R to W and then R to Y
on furnace control thermostat terminals.
WARNING:
Blower access door switch opens 115-v
power to furnace control. No component operation can
occur. Caution must be taken when manually closing this
switch for service purposes. Failure to follow this warn-
ing could result in electrical shock, personal injury, or
death.
NOTE:
If thermostat terminals are jumpered before blower ac-
cess door switch is closed, blower will run for 90 sec before
beginning a heating or cooling cycle.
14. If furnace is operating properly, REMOVE TAPE TO
RELEASE BLOWER ACCESS DOOR SWITCH, replace
blower access door.
C.
Cleaning Heat Exchanger
The following steps should be performed by a qualified service
technician.
NOTE:
If the heat exchangers get a heavy accumulation of soot
and carbon, they should be replaced rather than trying to clean
them thoroughly due to their intricate design. A build-up of soot
and carbon indicates that a problem exists which needs to be
corrected, such as improper adjustment of manifold pressure,
insufficient or poor quality combustion air, incorrect size, or
damaged manifold orifice(s), improper gas, or a restricted heat
exchanger. Action must be taken to correct the problem.
Fig. 2—Model 393AAV Upflow Furnace
A99284
BLOCKED
VENT
SAFEGUARD
FLUE
COLLECTOR
BOX
MOUNTING
SCREWS
RELIEF
BOX
CONTROL
FILTER
RETAINER
WASHABLE
FILTER
FLUE
COLLAR
PRESSURE
SWITCH
GAS
VALVE
C
OM
24V
HUM
G
R
Y
W
→
TABLE 2—SPEED SELECTOR
COLOR
SPEED
FACTORY-
ATTACHED TO
Black
High
Cool
Yellow (When
present)
Medium-High
Spare
Blue
Medium-Low
Heat
Red
Low
Spare
White
Common
L2/COM
—3—
→