Bendix Commercial Vehicle Systems AD-IS EVERFLOW User Manual
Page 6
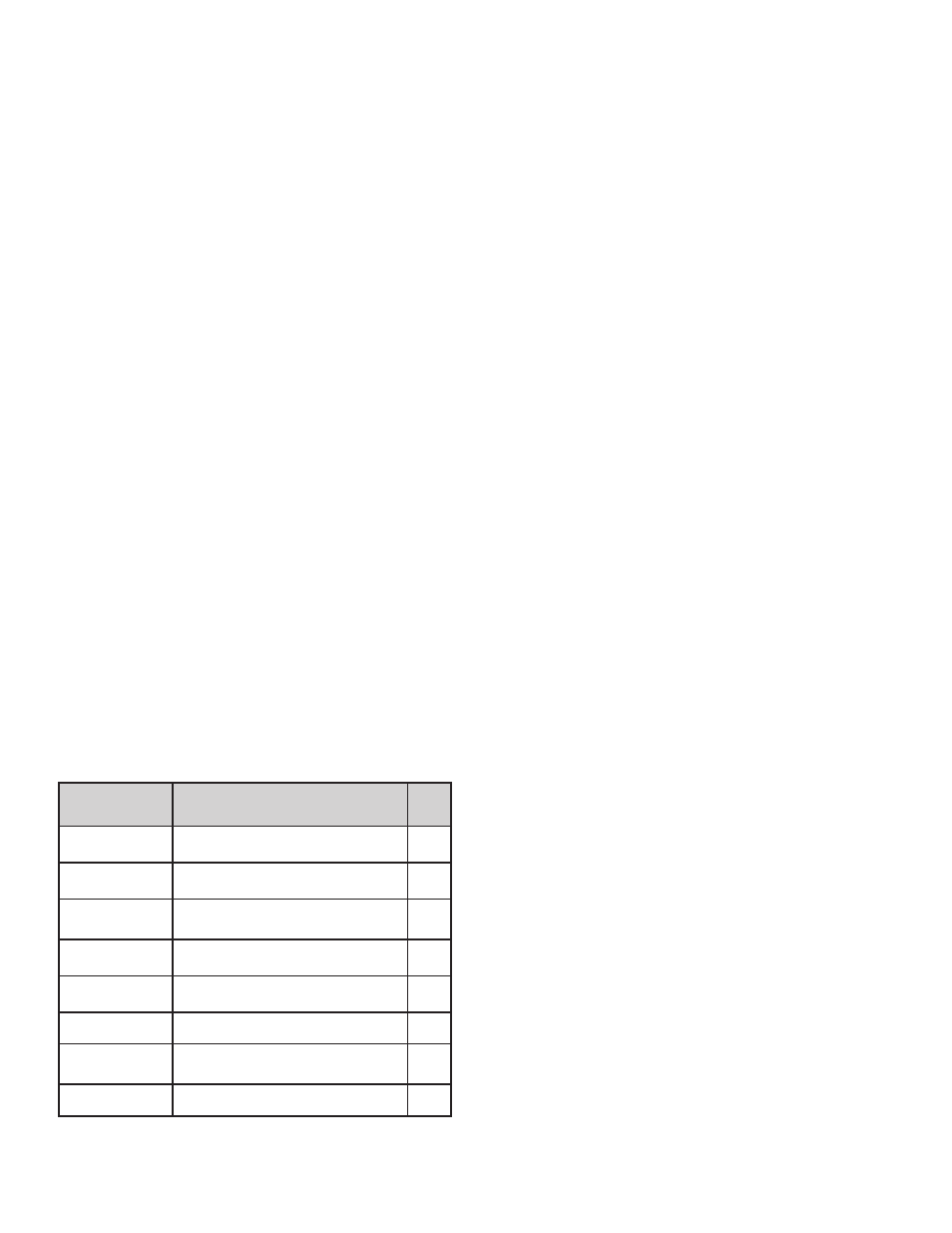
6
TURBO CUT-OFF FEATURE
The primary function of the turbo cut-off valve is to prevent
loss of engine turbocharger air pressure through the AD-IS
EverFlow assembly when both dryers are in the unloaded
mode. At the onset of the purge cycle, the downward travel
of the purge piston is stopped when the turbo cut-off valve
(tapered portion of purge piston with a soft seat) contacts
its mating metal seat in the purge valve housing. With
the turbo cut-off valve seated (closed position), air in the
compressor discharge line and AD-IS EverFlow assembly
inlet port cannot pass through the air dryer. In this manner
the turbo cut-off effectively maintains turbo charger boost
pressure to the engine.
Delivery pressure in excess of
175 PSIG can cause the purge valve to cycle rapidly
between load and purge mode. All AD-IS EverFlow
assemblies require a soft seat purge valve.
HIGH VOLUME MODE
If the GOV port of the electronic module indicates that the
compressor has been charging for longer than 30 seconds,
the dryers will alternatively purge every 30 seconds. This
is an indication of high volume through the dryer. When
the governor signal indicates the charge cycle is complete,
the assembly returns to normal brake cycling.
PREVENTATIVE MAINTENANCE
For Bendix
®
AD-IS
®
EverFlow
®
air dryers: Preventative
Maintenance is as easy as 1-2-3
Adhering to a preventative maintenance schedule is
crucial to keeping a vehicle’s air system clean and
ensuring superior performance of all components that
utilize system air — such as brakes, emissions equipment
and automated manual transmissions. Depending on
vocation, Bendix recommends a 1, 2 or 3-year air dryer
cartridge replacement on vehicles equipped with a Bendix
®
compressor.
For severe service application — such as residential refuse
trucks or school buses — the air dryer cartridge should
be replaced every year or 100,000 miles; for pick-up
and delivery operations, or for double- and triple-trailer
line haul trucks, every two years or 200,000 miles is the
recommendation. Line-haul operations using a single trailer
should swap the filter out every three (3) years or 300,000
miles. The recommended intervals for trucks equipped with
non-Bendix compressors are 6 months (50,000 miles),
one year (100,000 miles) and two years (200,000 miles),
respectively.
TABLE 1 -
BENDIX
®
AD-IS
®
AIR DRYER PORT
DESIGNATIONS
Air Connection
Port ID
Function/
Connection
QTY
1
IN
Inlet Port (air in)
1
21
PRI
Delivery Port Out (to Primary Reservoir)
1
22
SEC
Delivery Port out (to Secondary
Reservoir)
1
24
AUX 1
Auxiliary Delivery Port (air out)
4
23
AUX 2
Auxiliary Delivery Port (air out)
1
UNL
Unloader Control Air (D-2A
™
Governor)
2
RES
Common Reservoir Pressure
(D-2A Governor)
2
EXH
Governor Exhaust
1
volume is high, the electronic module switches the dryers
every 30 seconds until the air volume demand returns to
normal. The air dryer purge piston moves down in response
to a pneumatic signal from the Bendix
®
AD-IS
®
EverFlow
®
electronic module, causing the purge valve to open to
the atmosphere and the turbo cut-off valve to close off
the supply of air from the compressor (this will be further
discussed in the Turbo Cut-off Feature section). Water
and contaminants which have collected in the dryer are
expelled immediately when the purge valve opens. Also, air
which was flowing through the desiccant cartridge changes
direction and begins to flow toward the open purge valve.
Liquids and other contaminants collected by the liquid
separator are removed by air flowing from the purge
reservoir through the desiccant bed to the open purge valve.
The initial purge and desiccant cartridge decompression
lasts only a few seconds and is evidenced by an audible
burst of air at one of the Bendix
®
AD-IS
®
EverFlow
®
assembly’s purge exhaust. The actual reactivation of the
desiccant bed begins as dry air from the purge reservoir
flows through the purge orifice into the desiccant bed.
Pressurized air from the purge reservoir expands after
passing through the purge orifice.
The flow of dry air through the drying bed removes water
vapor from the desiccant material. The purge lasts 30
seconds. The delivery check valve assembly prevents air
pressure in the brake system from returning to the purging
air dryer during the purge cycle. After the purge cycle is
complete, the air dryer is ready for the next charge cycle
to begin.