S&S Cycle Billet Oil Pump for Big Twin Engines User Manual
Page 8
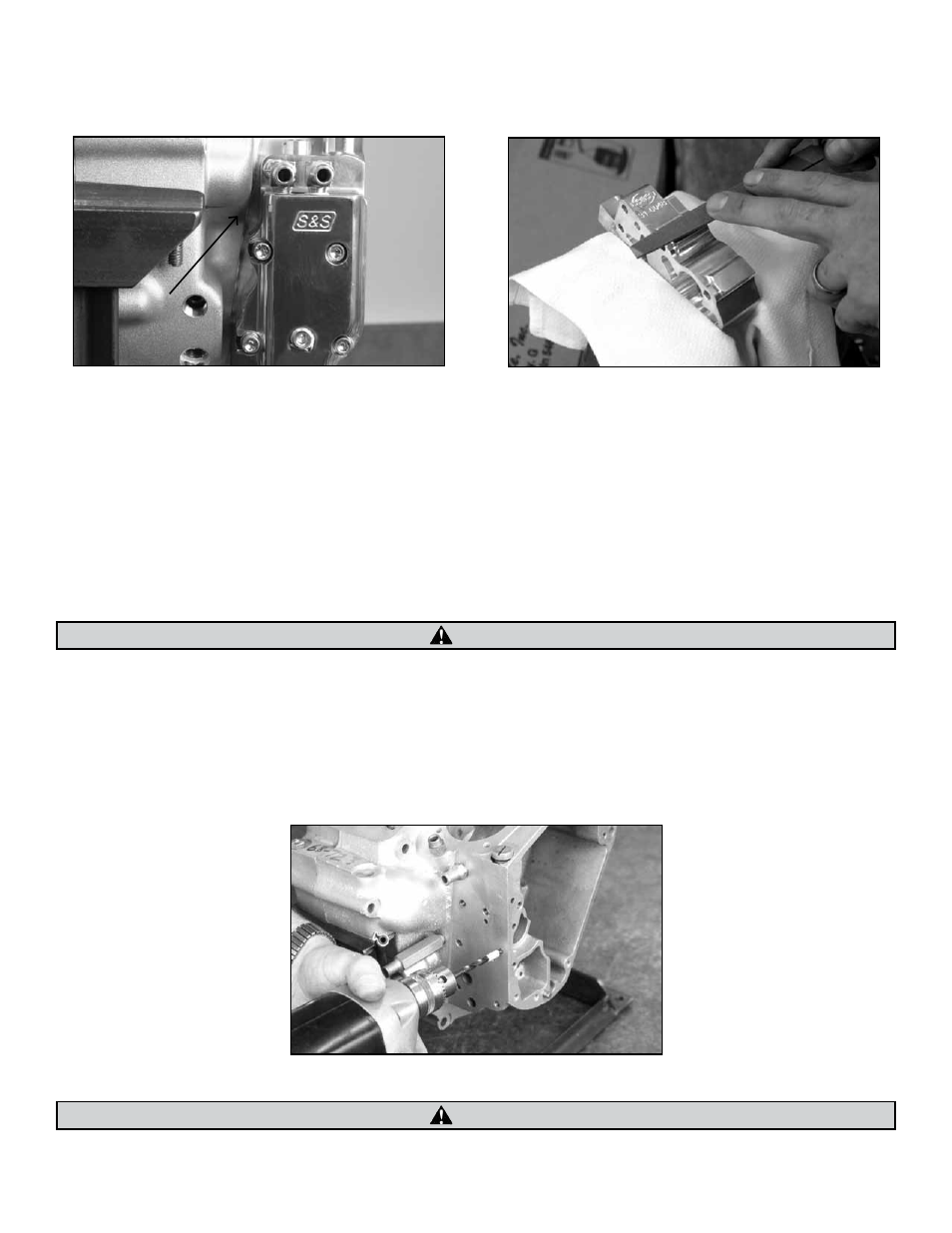
8
C. Confirm that adequate clearance exists between oil pump body and crankcase by temporarily installing pump assembly on crankcase and
inspecting areas indicated in photo. See Picture 9. In some instances it may be necessary to remove small amount of material from pump
body to obtain correct fit. See Picture 10.
Picture 9
Picture 10
NOTES
•
If modification of pump body is necessary, remove minimum amount of material required to properly position oil pump on crankcase. Take special care
not to damage gasket surfaces. After modification, clean pump body thoroughly with suitable parts cleaner and compressed air to remove metal filings
generated during procedure. Remove all traces of solvent prior to installation.
•
S&S® crankcases require no modification for S&S oil pump. S&S 1936-1969 generator- style cases are machined to accept S&S or stock cast iron or early
alloy pump. S&S 1970-later alternator style crankcases are machined for 1981-1991 or 1992-up oil pump as specified at time of order. Both S&S and stock
oil pump for specific year group can be installed without modification.
•
S&S has used 1991-earlier and 1992-later style mounting bolt pattern in S&S engines. Confirm pattern prior to ordering replacement pump body or
cover. See Picture 4. Oil pump gasket of known year can be used to positively identify mounting bolt pattern.
•
Proper identification of crankcase is imperative to insure correct pump installation. Machining of some aftermarket crankcases may not be consistent
with a specific year group. If in doubt about modifications required for aftermarket crankcase, contact crankcase manufacturer.
•
Failure to clean oil pump before engine assembly may result in engine damage.
•
Improper oil pump installation due to incorrect identification of crankcase year group may result in engine damage.
2. Crankcase Modification - 1970-1972 Only - Plug 3⁄16" Oil Overflow Hole.
A. If engine has been removed from chassis, CAREFULLY enlarge hole in photo (See Picture 11) with .203" (13⁄64") drill. If engine has not been
disassembled, apply grease to bit and both ends of hole to catch chips. Wrap masking tape around drill .225" from point to use as depth
guide. If engine is in chassis, enlarging hole may be difficult. In this case hole may be tapped without enlarging, but extreme caution is
required to avoid breaking tap off in hole.
CAUTION
Picture 11
Drill bit o.d. is close to hole size and may distort hole if drill is not steadied. Distorted hole may cause poor thread fit after hole is tapped.
CAUTION