S&S Cycle Billet Oil Pump for Big Twin Engines User Manual
Page 16
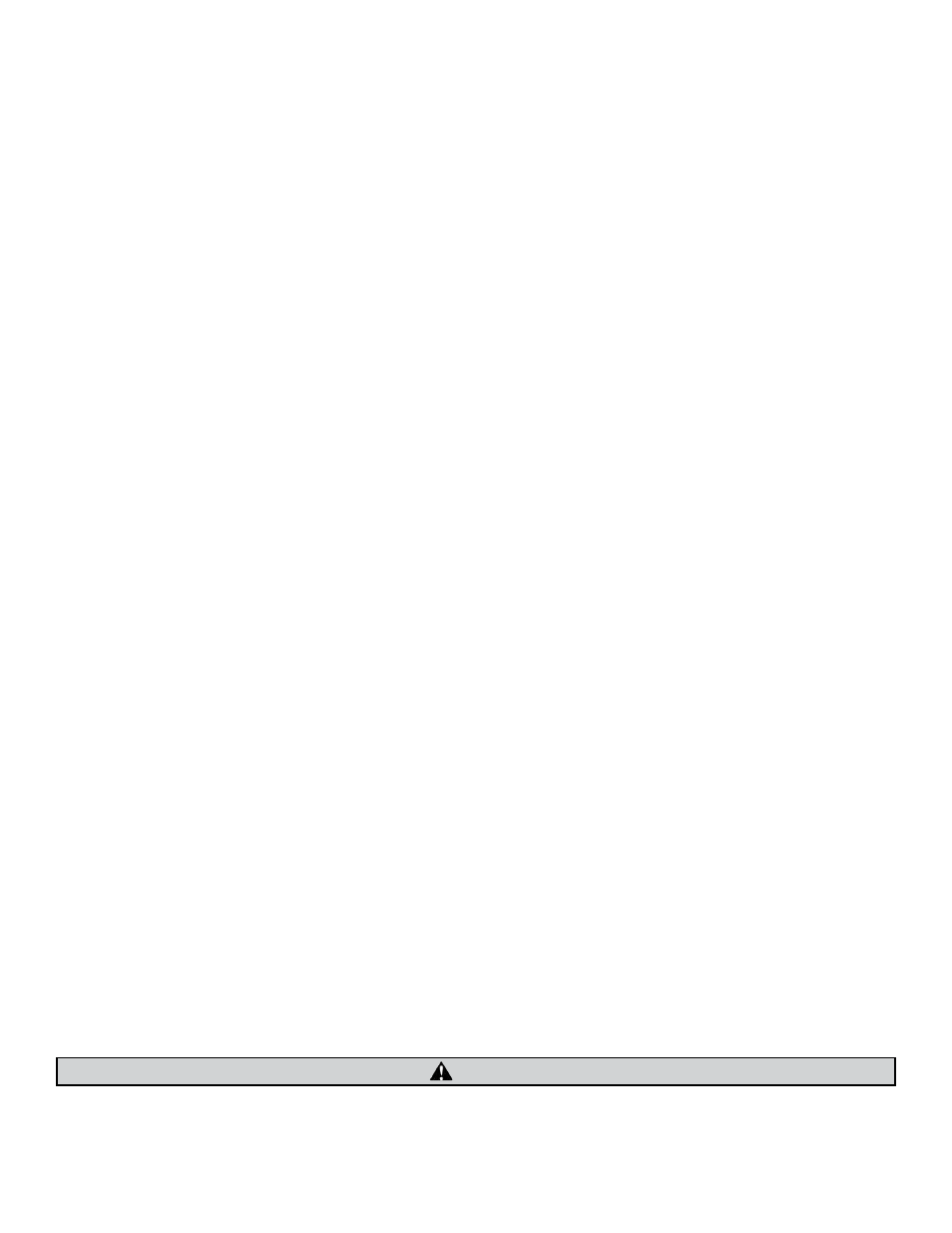
16
B. Covers #31-6060 and #31-6063 - See Pictures 5 and 6. Custom covers #31-6060 and #31-6063 are identical except that #31-6060 has
early mounting bolt pattern and #31-6063 has late pattern. Custom covers provide for bottom-mount oil line fittings only and offer no
provision for pressure sending unit, primary chain oiler, or 1992-up OEM rigid supply line. Custom covers are compatible with 1992-up
rigid return line.
1. Preparation - Apply PTFE tape or pipe sealant to threads of 2 ea. 90° elbow fittings #50-8114 and 2 ea. 1⁄8 -27 hose fittings #50-8115. If
1992-up rigid return line is used, substitute compression fitting #50-8120 for one hose fitting #50-8115.
2. Install elbow fittings #50-8114 in hole #5 (return) and hole #9 (supply). Install hose fittings #50-8115 in elbows. If 1992-up rigid return
line is used, substitute compression fitting for hose fitting in hole #5 elbow. Position elbow so open end of compression fitting faces
front of motorcycle.
NOTE - Return fitting in hole #5 will normally be directed toward oil filter. For instance, return fitting will normally face forward in models with oil filter in
front of crankcase.
C. Cover #31-6061 - See Pictures 5 and 7. Cover #31-6061 is often referred to as S&S® universal cover. It is supplied on S&S engines unless
customer specifies otherwise at time of order. Universal cover is compatible with rigid supply and return lines used on 1992-up rubber
mount models. Fittings for oil supply and return lines can be placed in holes at either bottom or top of cover as required by purchaser.
Fitting for main oil supply line can also be installed in hole in face of cover.
NOTE - Hole #6 in face of cover #31-6061 can be used as main oil supply line only. Hole is low pressure site and cannot be used for top end oil supply or oil
pressure monitoring.
1. Preparation - Apply PTFE tape or pipe sealant to threads of 2 ea. 90° elbow fittings #50-8114 and 2 ea. hose fittings #50-8115. Substitute
compression fitting #50-8120 for one hose fitting #31-6010 if 1992-up rigid return line is used.
2. Install elbow fittings in holes #1 or #5 (return), and #2 or #4, or #6 (supply). Hole #5 will be used for 1992-up rigid return line. Hole #6 will
be used for 1992-up rigid supply line.
3. Install hose fittings #50-8115 in elbows. If compression fitting #50-8120 is used for 1992-up rigid return line, install in hole #5 elbow.
NOTE - If rigid oil lines are used , return fitting must face forward, toward front of engine. Supply fitting will face downward at approximate 45° angle
toward lower left corner of pump cover.
D. Cover #31-6062 - See Pictures 5 and 7. Fitting for main oil supply line fitting can be placed in hole in top of cover or hole in face of cover.
Bottom hole is only location for return line fitting. Cover #31-6062 is compatible with 1992-up rigid return line.
NOTE - Hole in face of cover #31-6062 can be used as main oil supply line only. Hole is low pressure site and cannot be used for top end oil supply or oil
pressure monitoring.
1. Preparation - Apply PTFE tape or pipe sealant to threads of 2 ea. 90° elbow fittings #50-8114, 2 ea. hose fittings #50-8115, and one 1⁄8-27
pipe plug #50-8331. Substitute compression fitting #50-8120 for one hose fitting if 1992-up rigid return line is used.
2. Install elbow fittings in holes #1 or #5 (return), and #2 or #4, or #9 (supply).
3. Install hose fittings # 50-8115 in elbows. If compression fitting #50-8120 is used for 1992-up rigid return line, install in elbow in hole #5.
8. Installation
A. Confirm that adequate clearance exists between oil pump body and crankcase by temporarily installing pump assembly on crankcase and
carefully inspecting areas indicated in photo. See Picture 9. Do not install oil pump driveshaft gear or snap ring at this time. It may be
necessary to remove a small amount of material from oil pump body to obtain correct fit. See Picture 10.
NOTES
•
Remove minimum amount of material required to properly position oil pump on crankcase. Avoid damaging gasket surfaces. After modification, clean
pump body thoroughly with suitable parts cleaner solvent and compressed air to remove metal filings generated during procedure. Solvent must be of
type that will not harm driveshaft seal in oil pump body. Remove all traces of solvent prior to installation of pump.
•
S&S includes both 1⁄4 -20 and 1⁄4 -24 mounting bolts in oil pump kits. Some 1⁄4 -24 bolts provided previously were black. All mounting bolts provided in
current kits are plated. Visually compare threads and gently screw bolts into crankcase to confirm correct thread.
•
S&S oil pump bodies, covers and gaskets may appear similar to other manufacturerís products but should not be interchanged due to possible differences
that could impair oil pump function.
•
Failure to confirm fit of pump on crankcase as described in Section 8-A may result in oil pump damage not covered under warranty.
•
Using oil pump components other than those provided by S&S® may result in oil leak, insufficient oil pressure and possible
engine damage.
CAUTION