S&S Cycle Balancing Kit User Manual
Page 7
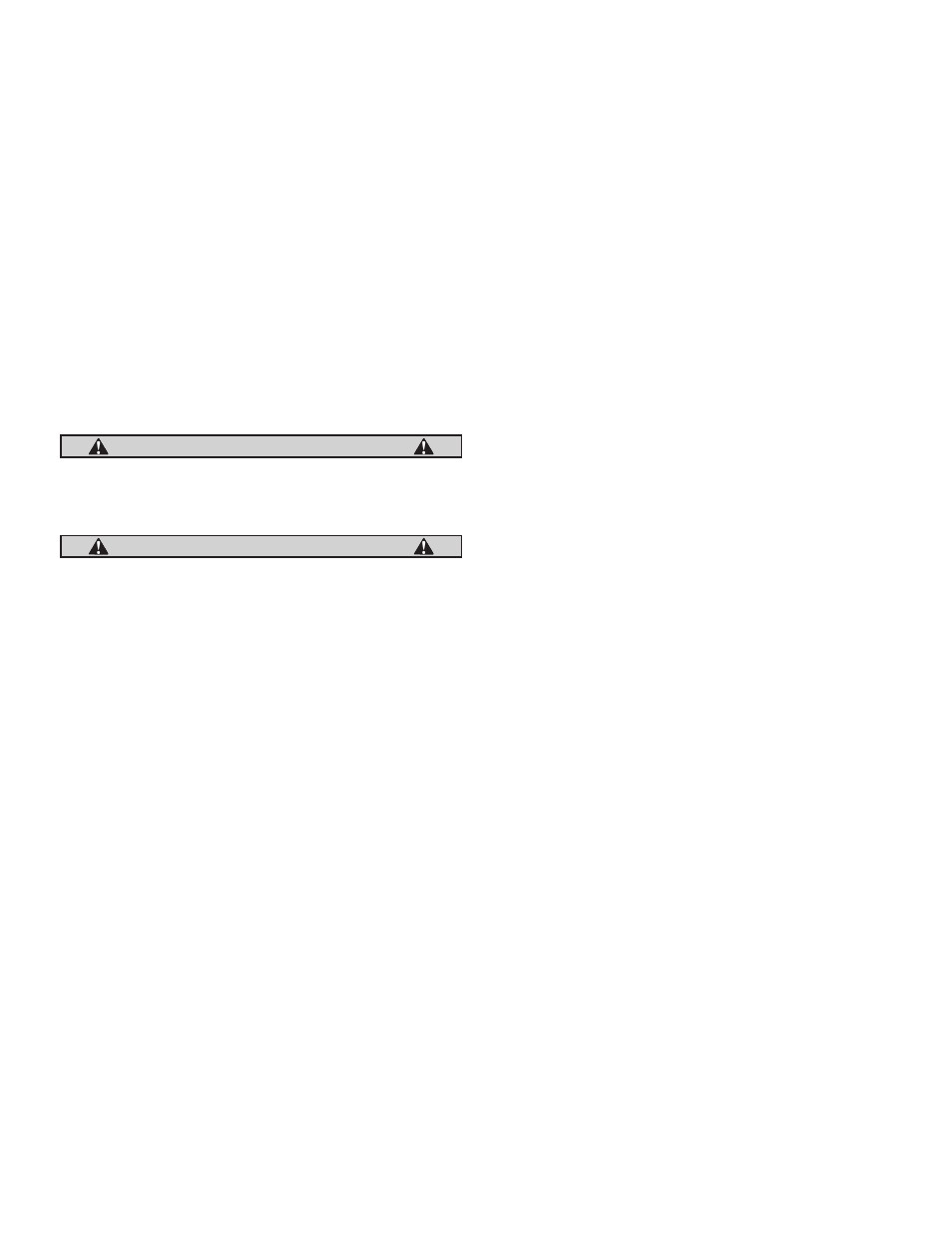
Example:
If 200 gm is removed from bobweight, 100 gm must be added to
counterweight. Slug size can be estimated using the following:
1.000" Diameter X 1.100" long adds about 100gm
.500" Diameter X 1.100" adds about 25gm
Mallory metal is available from:
M. I. Tech Metals
1340 North Senate Ave
Indianapolis, IN 46202
1-800-624-1895
www.mi-techmetals.com
Conclusion
We feel that excellent results can be obtained using this kit to statically
balance flywheels. As proficiency increases, actual balancing can be
done in a matter of minutes. Weighing parts and calculating weight of
bobweight to be used will actually take longer.
Included is a copy of a record form we developed and urge you to
use. Make copies of this form and use them (save the original to make
copies). It is interesting to review these records from time to time and
note similarities and trends.
The material in this instruction sheet should equip the engine builder
with a basic understanding of balancing. There are many technical
aspects that would fill books on the subject, but for the average shop
application, further discussion is not necessary.
NOTE: If heavy spot continually changes position around circumference
and flywheel still wants to rotate, more than likely balance stand/surface
plate is not perfectly level, or balance shaft or balance stand surfaces are
dirty, nicked or uneven.
G. Repeat process for other flywheel.
NOTES:
•
Drill holes in center of face along dotted line in diagram. (See Figure
4, previous page) Leave 5⁄16" of material to avoid breaking out of back
side of flywheel.
•
Do not drill holes deeper than 1⁄4" in areas marked near crankpin hole.
•
When balancing stock Harley-Davidson® or other cast iron flywheels,
drill holes 1⁄4" minimum from outer edge of rim. Space holes 1⁄4” apart.
•
S&S® forged steel flywheels are stronger. Holes can be drilled 1⁄8" from
outer rim and 1⁄8" apart.
•
Do not accept flywheels for rebalancing with holes drilled in
unprescribed areas.
•
Have flywheels magnafluxed to check for cracks if any doubt exists
about structural integrity.
CAUTION
Numerous holes and drilling holes in unprescribed areas may
weaken flywheels causing them to break resulting in damage to
engine.
WARNING
Weakened flywheels from improper balancing and being
rebalanced too many times may explode during operation
causing personal injury to you or others around you.
•
Before drilling, check opposite side of flywheel for old balance holes.
Do not drill into old holes.
•
If drilling must be done in crankpin side of flywheel and there are
holes in counterweight side, fill holes in counterweight side first before
balancing. There are several ways to do this:
Solder method:
1. Tap holes.
2. Heat holes with propane torch.
3. Fill holes with acid core solder.
4. Use punch or chisel to stake threads to insure that solder can
not come out of threaded hole during engine operation.
Threaded rod method:
1. Tap holes.
2. Screw a bolt or threaded rod into holes. Use Loctite® or similar
thread locking compound to insure that threaded rod can not
come out of threaded hole during engine operation.
3. Cut threaded rod off and grind or machine flush with surface of
flywheel.
Filling holes makes counterweight side heavier thereby reducing
number of holes required to balance flywheel.
•
When balancing flywheels to very heavy bob weights, it is sometimes
necessary to machine holes in counterweight of flywheel and press
in slugs of Mallory metal tungsten alloy (sometimes called heavy
metal). To determine the amount of Mallory to add to counterweight,
remove weights from bobweight until flywheel could be balanced to
the lightened bobweight by normal drilling method. Note amount of
weight removed, and replace weights on bobweight. One half amount
of weight removed from bobweight must be added to flywheel
counterweight.
7