S&S Cycle Balancing Kit User Manual
Page 6
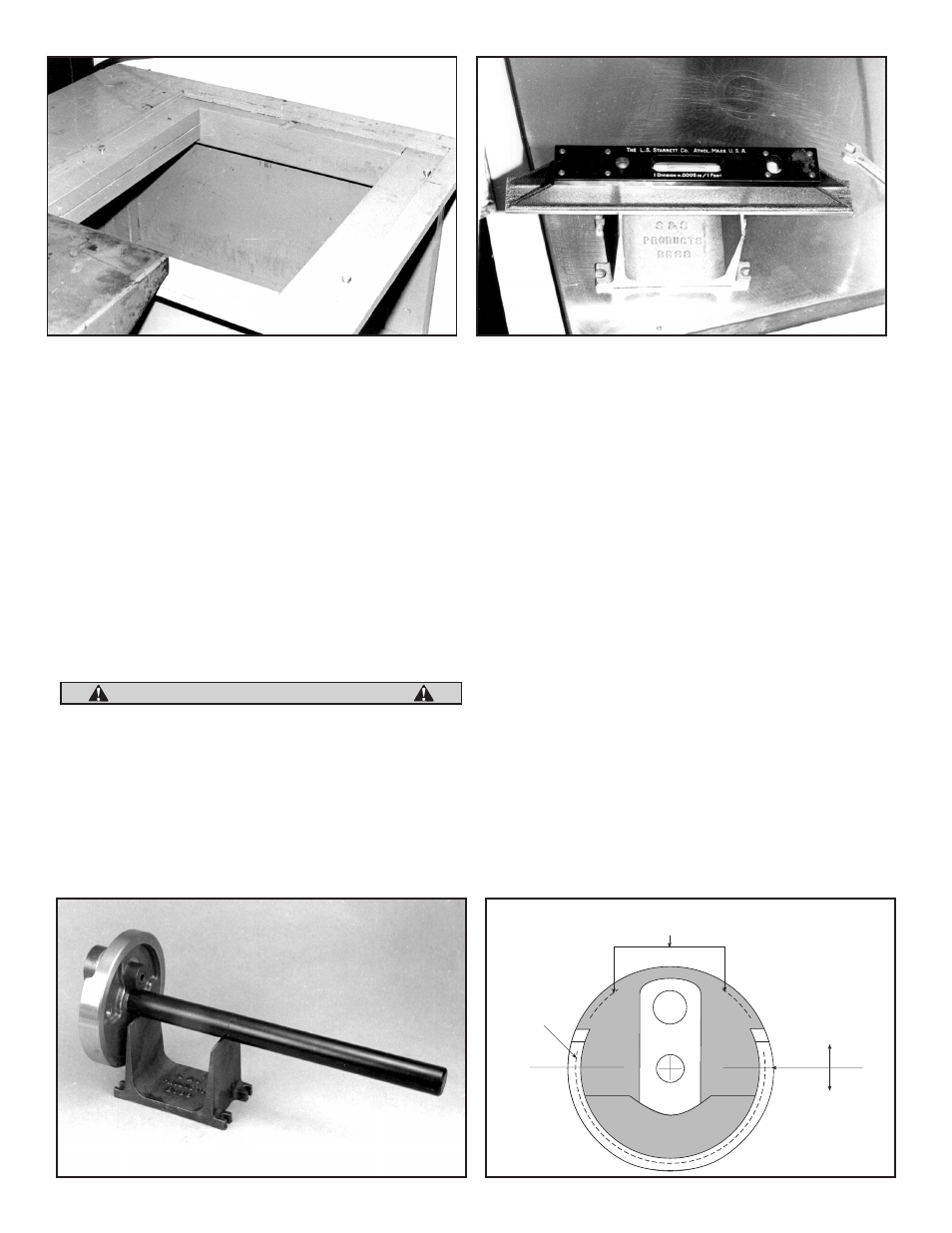
NOTE: Leveling is important and should be done as accurately as possible.
Recheck before performing each balance job.
6. Balancing flywheels
A. Gently place flywheel assembly to be balanced on balance
stand. Position assembly with balance shaft installed between
and in center of stand edges with bobweight at top. See Picture
3, page 5. Bobweight must clear edge when allowed to rotate
360°. Assembly with sleeve and counterweight screwed on
shaft place outside of stand edges but in center with bobweight
at top. Counterweight must be perpendicular to parallels, and
bobweight nut must clear stand throughout 360° of rotation.
See Picture 6, below
NOTE: Balance stand and balance shaft should be handled with care so as
not to nick or scratch stand edges or other balancing component surfaces.
CAUTION
Damaged components will cause unwarranted rolling resistance
between parts often resulting in misleading readings and
improper balance hole placement.
B. Heavy side of assembly (usually counterweight side of flywheel
or side opposite bobweight) will rotate downward. When
heavy point on flywheel has been determined, mark position
on inside (connecting rod side of flywheel). Check to be sure
heaviest spot has been selected by positioning spot 90° to right
of downward position and then letting flywheel rotate. Recheck
by positioning spot 90° to left of downward position and then
letting flywheel rotate. Note each time how fast flywheel drops
to heaviest position.
C. Set drill press with table that can be moved up and down and
swiveled from side to side so flywheel/bob weight assembly
when placed with rod side up on table can be drilled around
outer rim. Support as much of the assembly on drill press table
as possible.
D. Set drill depth so drill point stops 5⁄16" above table. Use 3⁄8" to
7⁄16" dia. drill to drill holes in Harley-Davidson® Sportster® model
flywheels and 7⁄16" to 1⁄2" dia. drill for big twins.
E. Before drilling see Figure 4, below right, for recommended
areas to drill. See following notes for drilling rules and additional
information.
F. There is no formula to explain how many holes to drill or how
deep holes should be. Experience is best teacher. After several
balance jobs you may be able to judge how much material
(how many holes to drill and how deep) must be removed from
flywheel by how fast heavy spot rotates downward. When first
starting and learning, drill hole about 1⁄4" deep, then check, then
drill again. Drill first hole at heaviest point to half depth. Drill
additional holes, an equal number to identical depths, on each
side of first hole. When flywheel is close to being balanced, 1⁄16"
depth of material in a 1⁄2" diameter hole will make a big difference
between assembly rotating or remaining stationary. If about
1⁄16" is all that’s left to remove, drill remaining amount from first
hole. Assembly is in balance when heavy point is placed in three
different positions on balance stand, 120° apart, and flywheel
remains stationary and does not rotate.
6
Picture 4
Picture 5
Picture 6
Figure 4
Counterweight Side
Crankpin Side
Do not drill holes deeper than ¼" in
area marked near crankpin holes