S&S Cycle Balancing Kit User Manual
Page 2
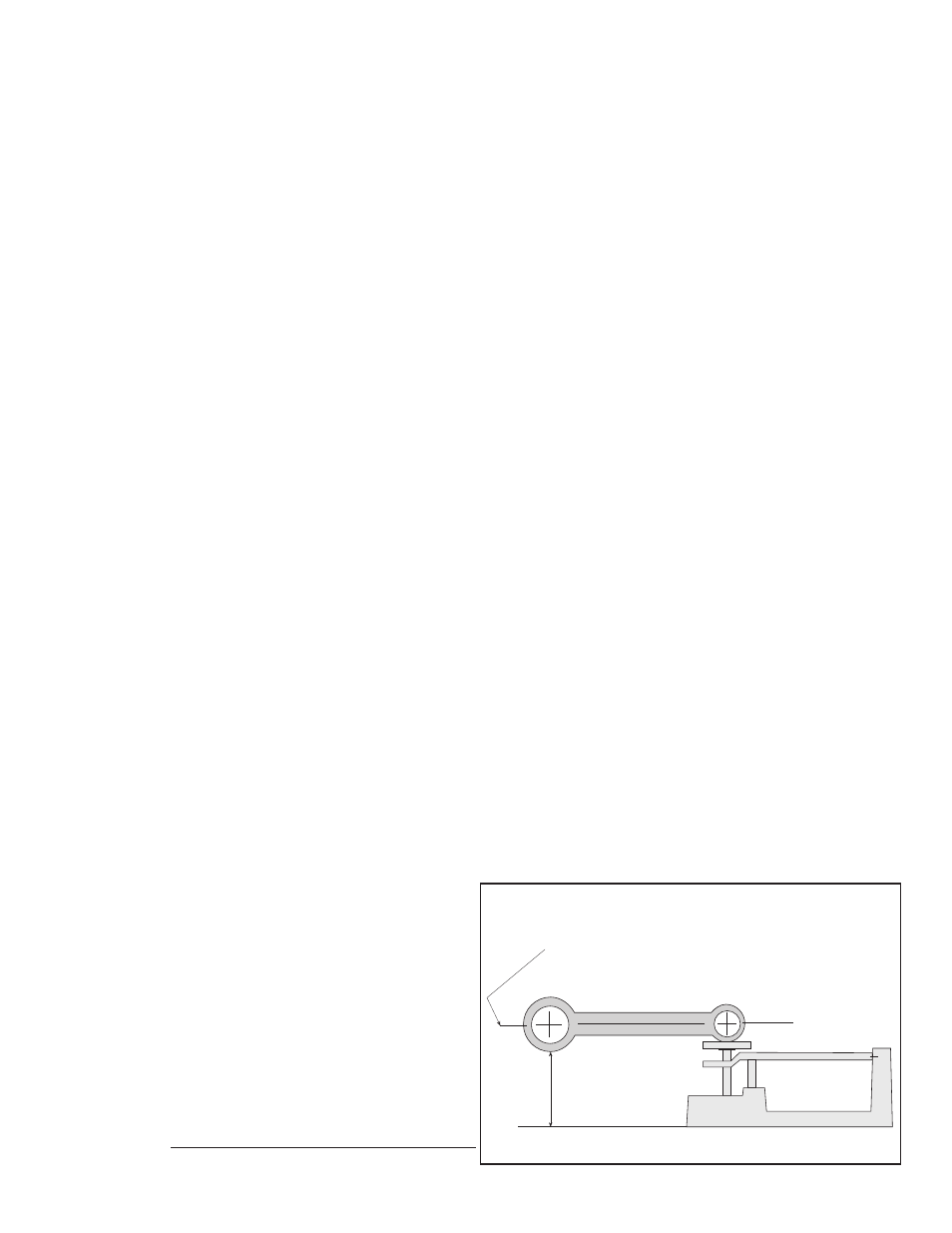
Introduction
The S&S® balancing kit is designed to allow the engine builder to
statically balance each flywheel separately in Harley-Davidson®
engines. The static method of balancing uses gravity to cause the
heaviest part of the flywheel to rotate downward when placed on the
balance stand. Weight is then removed from the heavy side by drilling
holes. When the flywheel no longer rotates, it is in balance.
The object of balancing the flywheels is to minimize engine vibration
which improves performance and riding comfort and avoids damage
to engine and chassis components. Usually the rider is quick to blame
engine flywheel imbalance as the cause of the problem. We have found
that the problem often lies elsewhere.
Improper engine installation in the frame, poor engine and transmission
sprocket alignments, flywheels not properly trued, tires out of balance,
faulty frame design, poorly balanced stator and/or clutch hub, worn
primary drive chain, and rigidly mounted handlebars are a few areas
that can cause vibrations often blamed on flywheel balance. Improper
installation of the engine in the frame and other chassis components
that are bolted on the frame sometimes form a resonant effect resulting
in vibration at certain rpms. This explains why an engine which runs
smoothly in one frame may vibrate when placed in another frame with
different forks. Only after investigating all of these other areas should
the engine be checked.
The 45˚ design of the Harley-Davidson® engine makes it difficult to
obtain perfect flywheel balance that will make the motorcycle vibration
free at all rpms. The goal is to make the motorcycle as vibration free
as possible and perform the best in the rpm range where the most
riding is done. If the engine is used exclusively for drag racing, it may
be desirable to balance for higher rpm ranges - say 3000 rpm upward.
Most street riders run their engines in the 2000 rpm to 5000 rpm range
most of the time.
The balance factor we use and recommend is 60%. We arrived at this
percentage after much experimentation, and found it to give the best
results over the rpm range that riders most commonly use. Factors
other than 60% will change the direction and amplitude of vibration.
For example, if the balance factor is 50% or less, the engine will tend to
vibrate vertically. As the percentage is increased, this vertical motion
changes to horizontal motion. Horizontal motion from our experiments
is more acceptable with less noticeable vibration transmitted to the
rider. Therefore, 60% is the percentage S&S uses as a compromise for
best all around performance and riding comfort.
Balance formula
The components which must be compensated for when balancing
Harley-Davidson® flywheels are placed in two categories.
Reciprocating parts - Reciprocating parts are those parts which
travel in a reciprocating (up and down) motion. These are the pistons,
piston rings, wristpins, wristpin clips and the wristpin ends of the
connecting rods. The total weight of the reciprocating parts equals the
reciprocating weight.
Rotating parts - Rotating parts are those which move in a circular
motion. The crankpin, crankpin nuts, bearings, bearing cages, nut locks
and screws, and crankpin end of both connecting rods are rotating
parts whose weights when added together equal the rotating weight.
The balance formula used to calculate the weight of the bobweight
that must be bolted into each flywheel is:
NOTE: S&S uses 60% of the reciprocating weight. When we speak of
the “balance factor,” we usually refer to the percentage of the total
reciprocating weight used in balance calculations.
Balancing procedure
Perform following steps to balance flywheels:
1. Weigh Parts
All reciprocating and rotating parts to be used must be weighed
and recorded to calculate weight of bobweight. For greatest
accuracy S&S recommends using gram scale. Weigh and record
weight of:
A. Front piston.
B. Front piston wristpin.
C. Front piston wristpin clips/buttons.
D. Front piston rings.
E. Repeat steps A through D for rear piston.
NOTE: Weighing parts separately allows for direct comparisons of parts in
event parts are replaced at some later time.
F. Crankpin.
G. Crankpin nuts.
H. Crankpin key.
I. Bearing cages.
J. Bearings.
K. Small end of front rod. See Figure 1 for correct positioning to
weigh connecting rod.
NOTE: To get correct weight of each end of rod, centerline of rod must
be level horizontally when pointer of scale is at zero position. Eyeball rod
position and adjust rod support stand accordingly. A card with horizontal
lines placed behind scale makes leveling of rods easier. Rest edge of rod
that exhibits smoother contours on platform and rod support stand.
Grinding marks and/or forging seam lines may cause unwarranted friction
which may distort actual balance weight of rod.
L. Big end of front rod.
M. Complete front rod.
2
Weight of
bobweight
per flywheel
(60% x reciprocating weight) + (100% x rotating weight)
2
=
Centerline of rod must be level horizontally when pointer of
scale is at zero. Eyeball rod position and adjust rod support
stand accordingly. Rest edge of rod the exhibits smoother
contours on platform and rod support stand. Grinding marks
and/or forging seam lines may cause unwarraned friction
which may cause errors in rod weight readings.
Figure 1