S&S Cycle Balancing Kit User Manual
Page 5
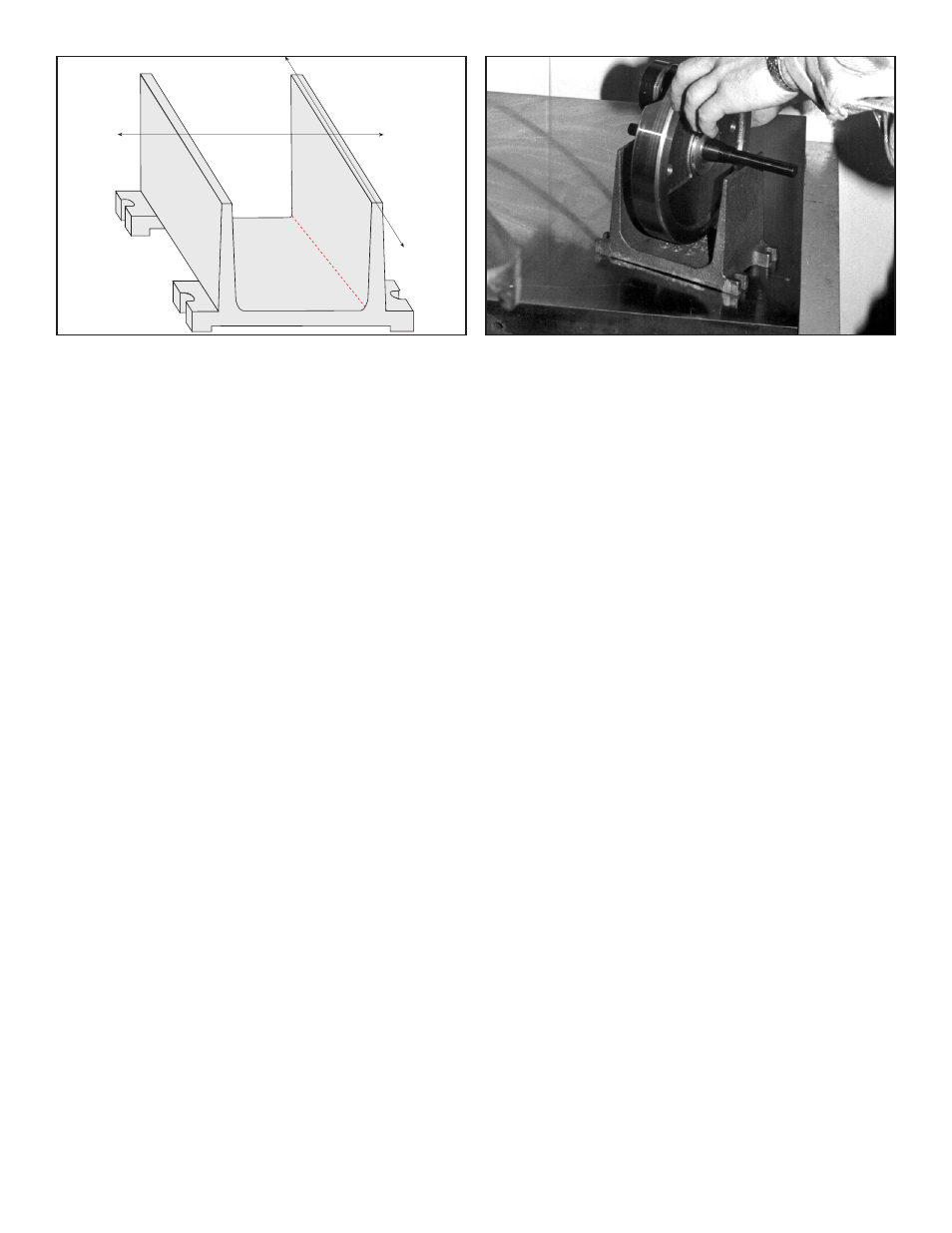
All Engines With One Piece Mainshaft/Flywheels
In 1985 Harley-Davidson® changed flywheel/mainshaft assembly
design from multiple piece to single, one piece construction. S&S®
kit components used to balance these flywheels are a set of special
adapter sleeves, two collar spacers and a counterweight. See Picture 2,
page 4 (one collar spacer not shown). Special adapter sleeve is screwed
on shaft to act as bearing surface and counterweight adapter. Collar
spacer is used on sprocket shaft to space adapter away from flywheel
if Timken® bearing has been removed. Counterweight is screwed in
adapter and offsets weight of flywheel and bobweight when assembly
is placed on balance stand.
NOTE: Some earlier two piece mainshaft/flywheel assemblies may also
be balanced using these balancing components in lieu of disassembling
them, rebalancing them and then reassembling them.
Big twin - driveside
A. Clean mainshaft bearing surface, flywheel crankpin taper, inside
and outside of collar spacer #53-0097 and sleeve #53-0091,
counterweight #53-0099 and bobweight taper with solvent.
B. If Timken® bearing assembly has been removed, use collar #53-
0097 to space sleeve #53-0091 away from flywheel.
C. Slip sleeve #53-0091 on sprocket shaft. Screw sleeve on to
sprocket shaft until sleeve contacts bearing or #53-0097 spacer.
Hand tighten. Do not overtighten.
D. Lay flywheel down with sleeve/shaft facing up and screw
counterweight #53-0099 into end of sleeve until hand tight. Do
not overtighten.
E. Bolt bobweight assembly in crankpin hole.
Big twin - camside
A. Clean mainshaft bearing surface, flywheel crankpin taper, inside
and outside of sleeve #53-0101, counterweight #53-0099 and
bobweight taper with solvent.
B. Slip sleeve #53-0101 on pinion shaft. Screw sleeve on shaft until
it contacts flywheel, and hand-tighten. Do not over tighten.
C. Lay flywheel down with sleeve/shaft facing up and screw
counterweight #53-0099 into end of sleeve until hand tight. Do
not over tighten.
D. Bolt bobweight assembly in crankpin hole.
Harley-Davidson® Sportster® model - driveside
A. Clean mainshaft bearing surface, flywheel crankpin taper, inside
and outside of collar spacer #53-0098 or #53-0085 and sleeve
#53-0093, counterweight #53-0099 and bobweight taper with
solvent.
B. If Timken® bearing assembly has been removed, slide collar
#53-0098 for ‘86-’90 engines or collar #53-0085 for ‘91 and up
engines on sprocket shaft to space sleeve #53-0093, away from
flywheel.
C. Slip sleeve #53-0093 on sprocket shaft. Screw sleeve on shaft
until it contacts spacer or Timken® bearing. Hand tighten only.
Do not overtighten.
D. Lay flywheel down with sleeve/shaft facing up and screw
counterweight #53-0099 into end of sleeve until hand tight. Do
not overtighten.
E. Bolt bobweight assembly in crankpin hole.
Harley-Davidson® Sportster® model - camside
A. Clean mainshaft bearing surface, flywheel crankpin taper, inside
and outside of sleeve #53-0095, counterweight #53-0099 and
bobweight taper with solvent.
B. Slip sleeve #53-0095 on pinion shaft. Screw sleeve on shaft until
it contacts flywheel and hand tighten. Do not overtighten.
C. Lay flywheel down with sleeve/shaft facing up and screw
counterweight #53-0099 into end of sleeve until hand tight. Do
not overtighten.
D. Bolt bobweight assembly in crankpin hole.
5. Balance stand
Balance stand shown in Figure 3, above left, has four mounting lugs
so it can be bolted down. Bottom of lug pads and two narrow top edges
have been surface ground. When stand is placed on a perfectly flat and
level surface, narrow edges should be level in both axes as shown.
A. Select unobstructed work surface or construct separate
“balancing bench.”
NOTE: If many balancing jobs are to be performed, it is recommended
that a special balancing bench be constructed. Building a separate bench
cuts down balancing stand setup and leveling time, because bench isn’t
subjected to day to day abuses which can alter stand staying level.
B. Bolt stand to bench. Do not tighten bolts. If surface plate is used
as in Picture 3, above right, stand does not need to be bolted
down.
C. Shim under four corners as necessary to level stand in both
directions as shown in Figure 3, above left. If separate bench
and surface plate combination is used, surface plate can be
leveled using three leveling screws located under surface plate.
See Picture 4, next page. Level stand/plate by placing level on
stand as in Picture 5, next page. Turn stand with level on edges
90° and check.
5
Level stand in
both axes as
shown.
Figure 3
Picture 3