JLG 3246E2 ANSI Operator Manual User Manual
Page 15
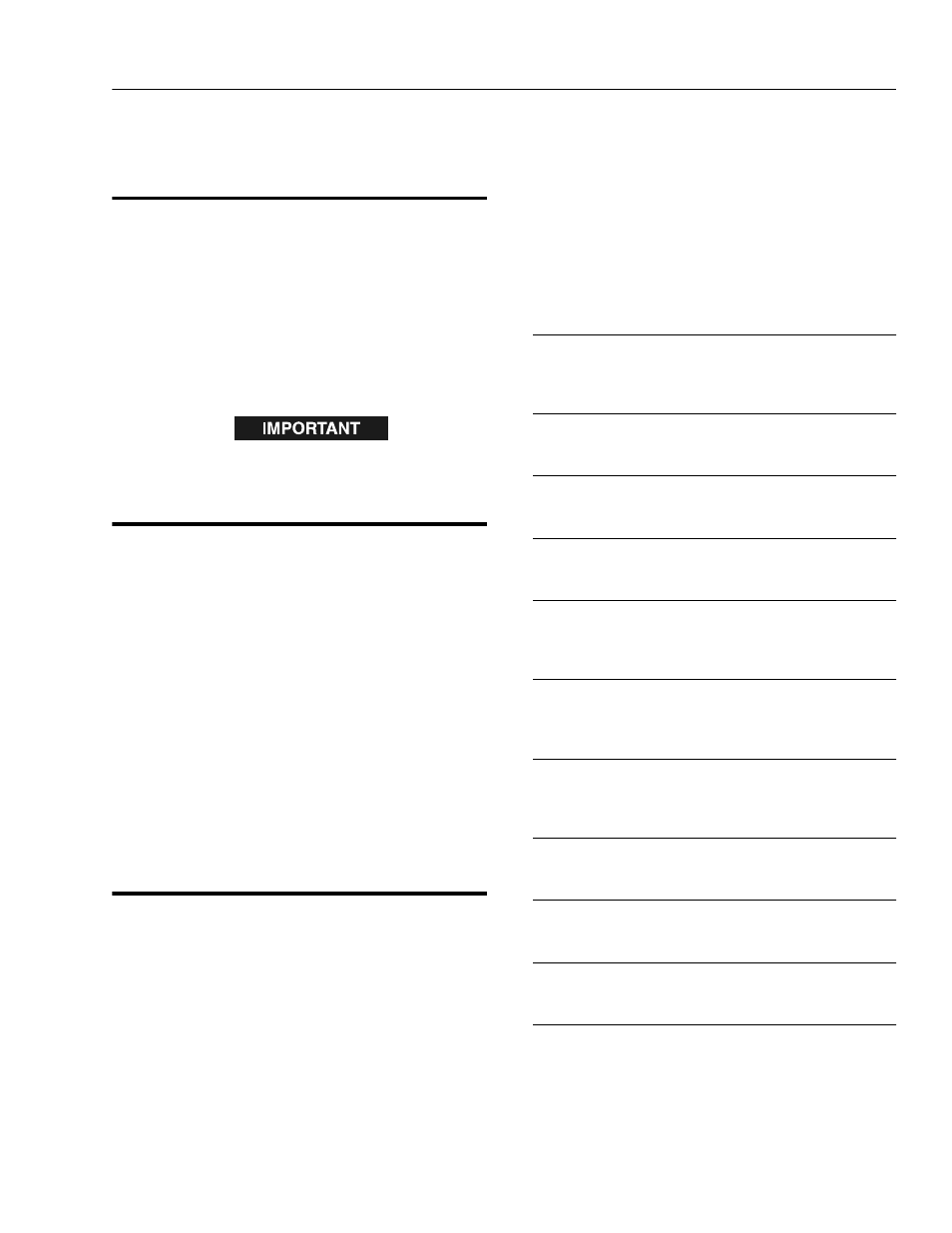
SECTION 2 - PREPARATION AND INSPECTION
3120736
– JLG Lift –
2-1
SECTION 2. PREPARATION AND INSPECTION
2.1
GENERAL
This section provides the necessary information needed
by those personnel that are responsible to place the
machine in operation readiness, and lists checks that are
performed prior to use of the machine. It is important that
the information contained in this section be read and
understood before any attempt is made to operate the
machine. Ensure that all the necessary inspections have
been completed successfully before placing the machine
into service. These procedures will aid in obtaining maxi-
mum service life and safe operation.
SINCE THE MACHINE MANUFACTURER HAS NO DIRECT CON-
TROL OVER THE FIELD INSPECTION AND MAINTENANCE,
SAFETY IS THE RESPONSIBILITY OF THE OWNER/OPERATOR.
2.2
PREPARATION FOR USE
Before a new machine is put into operation it must be
carefully inspected for any evidence of damage resulting
from shipment and inspected periodically thereafter, as
outlined in paragraph 2-3, Delivery and Periodic Inspec-
tion. The unit should be thoroughly checked for hydraulic
leaks during initial start-up and run. A check of all compo-
nents should be made to assure their security.
All preparations necessary to place the machine in opera-
tion readiness status are the responsibility of manage-
ment personnel. Preparation requires good common
sense, (i.e. lift works smoothly and brakes operate prop-
erly) coupled with a series of visual inspections. The man-
datory requirements are given in paragraph 2-4, Walk
Around Inspection.
It should be assured that the items appearing in the Deliv-
ery and Periodic Inspection and Functional Check are
complied with prior to putting the machine into service.
2.3
DELIVERY AND PERIODIC INSPECTION
NOTE: This machine requires periodic safety and mainte-
nance inspections by a JLG distributor, or certified
JLG mechanic. A decal located on the frame pro-
vides a place to record (stamp) inspection dates.
Check decal and notify dealer if inspection is over-
due.
An annual inspection shall be performed on the aerial plat-
form no later than thirteen (13) months from the date of
the prior annual inspection. The inspection shall be per-
formed by person(s) qualified as a mechanic on the spe-
cific make and model of the aerial platform.
The following checklist provides a systematic inspection
to assist in detecting defective, damaged, or improperly
installed parts. The checklist denotes the items to be
inspected and conditions to examine. Periodic inspection
shall be performed monthly or more often when required
by environment, severity, and frequency of usage.
Handrail Assemblies
Properly installed; no loose or missing parts; no visible
damage.
Platform Assembly
No visible damage; free of dirt and debris.
Sizzor Arms
No visible damage, abrasions and/or distortions.
Electrical Cable
No visible damage; properly secured.
Pivot Pins
No loose or missing retaining hardware; no visible dam-
age; no evidence of pin or bushing wear.
Lift Cylinders
No rust, nicks, scratches or foreign material on piston rod;
no leakage.
Frame
No visible damage; loose or missing hardware (top and
underside).
Tire and Wheel Assemblies
No loose or missing lug nuts; no visible damage.
Pothole Protection System
No loose or missing parts; no visible damage; no debris.
Sliding Wear Pad Blocks
No excessive wear; no visible damage.
Hydraulic Oil Supply
On all machines built before serial number 0200082630,
operate lift function through one complete cycle before
checking oil level. Oil level should read at full mark, or
within 1/2" below full mark, on side of hydraulic tank (all
systems shut down, machine in stowed position); no visi-
ble oil leakage on the ground.