Economy in quarrying – Liebherr L 556 User Manual
Page 8
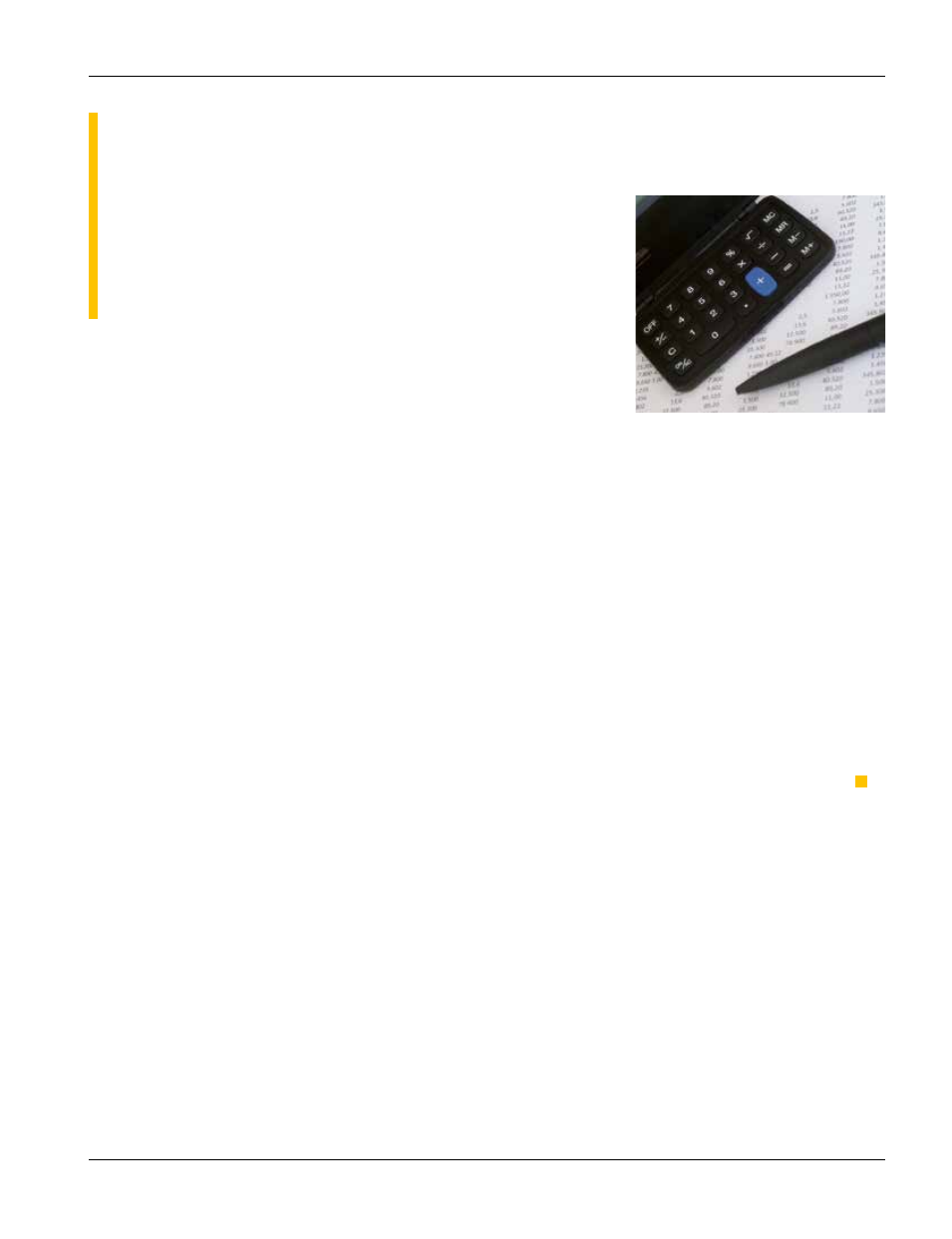
8 // Quarrying
Economy in quarrying
Two extremely important considerations
are improving mining and transportation
processes. This starts with the infrastructure
and organisation locally and asking: What
processes are performed at the site, for
example, at the quarry? How fast can the
machines operate? How much energy is
input to operate the conveyor belts and
how much fuel is needed to operate the
machines? How well trained are the
employees operating these machines? The
list of potential savings continues to
sustainable mining, resources and the
environment. We would like to illustrate
these questions by looking at examples of
machines. These have a decisive effect on
the costs per ton of materials extracted.
Wheel loader: up to 25 % less
fuel due to drive concept
Wheel loaders are mainly employed in the
industry for loading and transporting
materials. In mines and quarries, large
wheel loaders with an operating weight of
up to 33.1 tons are primarily used. Despite
this enormous machine weight and the
tough operating conditions, it is important
for fuel consumption to be kept low.
Liebherr wheel loaders achieve this with a
combination of hydrostatic travel drive and
the Liebherr Power Efficiency (LPE) system.
With this drive concept, all Liebherr wheel
loaders of the latest Tier4i / IIIB generation
save up to 25 % of fuel compared to other
machines of the same size class. While
fuel consumption drops, the hydrostatic
travel drive makes it possible to achieve
greater turnover rates per operating hour.
The hydrostatic travel drive allows a
particular installation position of the
Liebherr diesel engine – transverse or
longitudinal at the rear. Compared to
conventionally powered wheel loaders, this
leads to a higher tipping load with much
lower machine weight and an improved
turnover rate per operating hour. The LPE
system proactively influences engine
management by picking up the electronic
signal from the accelerator pedal and
computing the most efficient way of
carrying out the driver’s wishes.
Hydrostatic drive reduces wear
and costs
At the same time, the hydrostatic drive
ensures that costs caused by brake and
tire wear are reduced. While the freely
variable tractive power control reduces tire
wear by 25 %, the hydraulic braking effect
of the drive system reduces wear on the
brakes. Companies are spared the cost of
repairs caused by wear, which means
lower operating costs and better results.
How much can the impact on the
environment and on our natural resources
be reduced in mining? 0.3 gal of fuel
produces up to 7 lb of carbon dioxide
(CO
2
). By saving up to 1.3 gal per operating
hour, up to 33,070 lb less CO
2
is produced
in 1,000 operating hours.
Excavator automatically switches
engine off when idling
The excavator can be equipped with a
function that automatically switches the
engine off after a certain period spent
stationary. In conjunction with the sensor-
controlled automatic idling system, fuel
consumption is reduced even further,
lessening the environmental impact. To
optimally adapt the machine to different
conditions, the excavator driver can
choose between four different work
modes. Mode “E” (for economy) is
recommended for normal working
conditions, reducing the impact on both
the budget and the environment. A simple
touch of a button is all the driver has to do
to change modes. A pre-set engine speed
or hydraulic output is then made available
by the machine.
Driver usage, behavior data
improves economy
Not every driver uses a machine the same.
If you analyze exactly how a machine is
driven, you can draw conclusions as to how
it can be used more economically. This is
exactly what LiDAT – the electronic data
transmission and positioning system – does.
The data obtained can be used to make
the machine even more economical.
Companies working in the quarrying sector are under enormous
pressure to save time and reduce costs. Expenditures for operations
and rising fuel costs are forcing companies to work as efficiently and
economically as possible. Every company, therefore, asks the question:
how can we optimize essential production factors such as equipment,
work and energy in order to achieve a good turnover rate while keeping
operating costs low?
Advice – Part 1