Duff-Norton Machine Screw Rotating 500lb - 1 Ton User Manual
Page 7
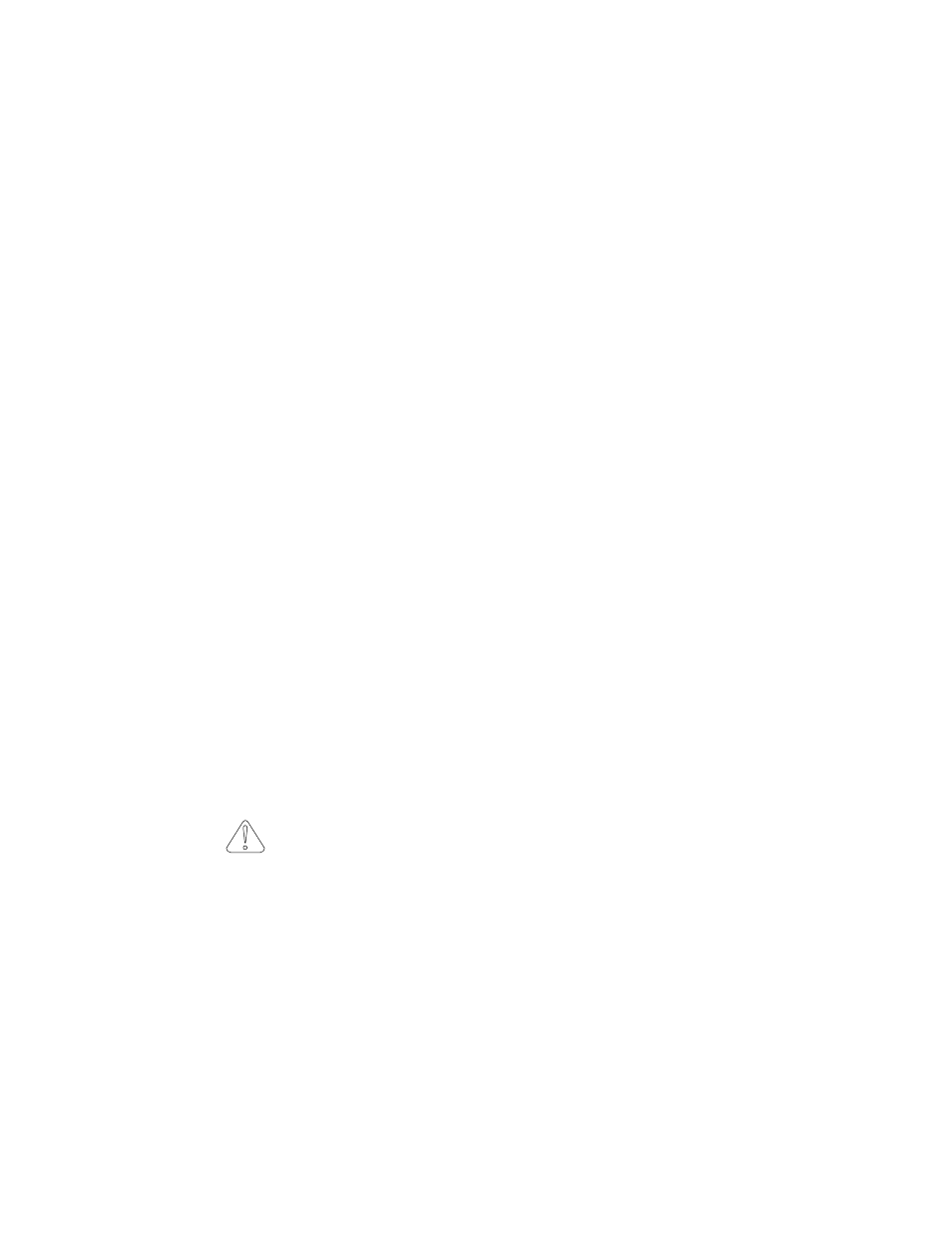
7
Note
If necessary, tap bearing loose with a soft face
hammer.
5. Remove bottom load bearing (8), which may be
attached to either shell (3) or gear (6).
6. 1/4 and 1/2-ton - remove four set screws (9) from the
shell (3) to loosen worm retainer bushings (10). If
threaded bushings are used, remove these, using a
spanner wrench. 1-ton - remove two retainer rings
(17) from worm housing.
7. Remove worm (11), needle bearing (13) and race
washers (12)(bearing Index No. 18 on 1-ton unit)
from the shell by striking one end of the worm with a
wooden or lead mallet.
8. Slide off worm retainer bushings (10) and needle
bearings (12 and 13) or bearing (18).
9. Restraining lifting screw (5) from turning (use soft
jaws), remove locknut (20) and lockwasher (21)(if
used) from screw(5).
10. Remove worm gear (6) from screw (5).
Note
It may be necessary to tap on worm gear. Use only a
soft-face hammer. Do not tap on gear teeth.
11. Remove key (22) from screw (5).
12. Inverted models — remove guide bushing (14) from
shell (3).
13. For units with damaged expansion plug (4a) in shell
(3) or shell cap (2), drive or press plug out of shell (3)
or shell cap (2) with a large die punch (1" diameter).
Disassembly is now complete.
2-5.
Cleaning
1. Use degreasing solvent to remove grease or oil from
all parts.
Note
Remove grease from unit and do not reuse old
grease.
Warning
Provide adequate ventilation during the use of
cleaning agent; avoid prolonged breathing of
fumes and contact with skin. Read and follow
manufacturer’s instructions.
2. Use clean hot water or a soap solution for general
cleaning of painted surfaces.
3. Dry parts thoroughly after cleaning.
Note
Before installing new parts, remove any rust preven-
tive, protection grease, etc.
2-6.
Inspection (Refer to Figure 3-1)
1. Make a visual inspection of shell (3) for broken,
cracked or distorted areas. Check threads of all
bores for burrs or broken threads.
2. Check shell cap (2), lifting screw (5), lifting nut (23)
and worm gear (6) for burrs or scratches on their
working or mating surfaces.
3. Check fit between rotating screw thread and internal
thread of lifting nut. If fit is excessively loose, replace
lifting nut or rotating screw as required.
4. Check small common components (screws, etc.) and
replace as required.
5. Check bearings (7,8, 13 and 18) for seizure, galling or
play and replace as required.
2-7.
Assembly (Refer to Figure 3-1)
1. To replace expansion plug (4a) refer to Figure 2-1.
For upright models, plug is installed in shell (3) (see
Figure 3-1) and in shell cap (2) for inverted units (see
Figure 3-1, Detail A).
a. As is appropriate, set shell cap (2) or shell (3) over
a steel bar which is approximately 1/8" or 3/16"
shorter than the shell or shell cap. The diameter of
the bar should be close to the I.D. of the shell or
shell cap.
b. Place expansion plug (4a) on the bar (concave
surface down) and flatten the plug against the bar.
Use a large diameter punch or press making sure
that the plug is flattened throughout its entire
diameter.
2. For 1-ton models, press bearing cones on worm gear
(6) with small end of cone facing away from gear
surface. Be sure that cone is seated properly against
shoulder.
3. Insert key (22) in screw (5).
4. Assemble worm gear (6) on screw (5).
5. Assemble lock washer (21) if used and lock nut (20)
to screw (5). Torque lock nut to appropriate torque as
follows: 1/4 ton-100 in-lb.; 1/2 ton-180 in-lb.; 1 ton-40
ft-lb.
6. Inverted units only. Install guide bushing (14) in shell
(3). Guide bushing must be flush with base. Lock
guide bushing in place by peening on the thread O.D.
of the bushing and shell with a center punch.
7. Place bottom load bearing (8) into shell (3) -on 1-ton
units, press bearing cup into shell first.
8. Install worm (11) into housing (3). For 1/4-ton and 1/2-
ton models- proceed as follows:
a. Slide thrust race (12), needle bearing (13) and
another thrust race on each end of worm (11).
b. Position worm (11) in shell (3).
c. Slide bronze worm retainer bushings (10) on both
sides of the worm shaft and place them in shell
until bushings are positioned to control lateral
movement of the worm to about .002 inches. If
bushings are the threaded type, the same proce-
dure should be followed except bushing should be
threaded into position in the shell. Install four set
screws (9) in shell (3). Tighten them down until
they seat against bronze retainer bushing (10).
For one ton model-press in one worm bearing (18),
position retainer ring (17) behind this bearing, place