Duff-Norton Machine Screw Rotating 500lb - 1 Ton User Manual
Page 6
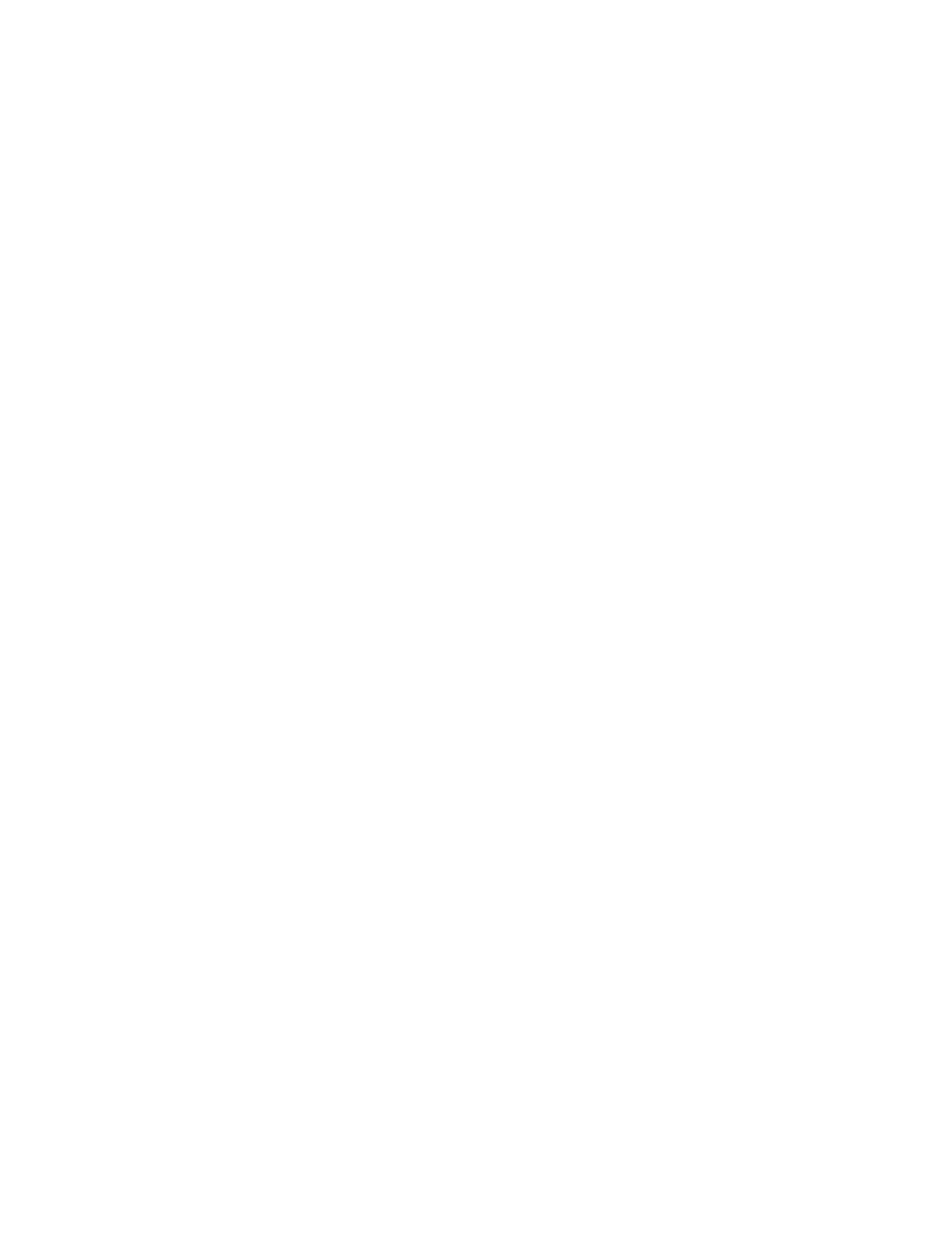
6
should be protected by some means such as a boot.
Note
Rotating screws should never be run dry. Inspect
frequently at regular intervals to be certain that a
lubrication film is present.
Note
For loads of 25% to 100% of actuator capacity, torque
requirements are approximately proportioned to the
load.
7. These actuators are self-lowering and these units
require a brake or other hold back device.
8. The lubrication procedures for normal and severe
service conditions, as described in Section II para-
graph 2-1, should be closely followed.
1-6.
Warranty and Warranty Repair
Subject to the conditions stated herein, Duff-Norton
will repair or replace, without charge, any parts proven to
Duff-Norton’s satisfaction to have been defective in
material or workmanship. Claims must be made within
Section II
Maintenance
one year after date of shipment. Duff-Norton will not
repair or replace any parts that become inoperative
because of improper maintenance, eccentric loading,
overloading, chemical or abrasive action, excessive wear,
or other abuse.
Equipment and accessories not of Duff-Norton’s
manufacture are warranted only to the extent that they
are warranted by the manufacturer, and only if the
claimed defect arose during normal use, applications and
service. Equipment which has been altered or modified
by anyone without Duff-Norton’s authorization is not
warranted by Duff-Norton. EXCEPT AS STATED
HEREIN, DUFF-NORTON MAKES NO OTHER WAR-
RANTIES, EXPRESS OR IMPLIED, INCLUDING WAR-
RANTIES OF MERCHANTABILITY AND FITNESS FOR
A PARTICULAR PURPOSE.
If you have any questions concerning warranty
repair, please contact Duff-Norton.
Authorization for return must be received from
Duff-Norton before returning any equipment for
inspection or warranty repair.
2-1.
Lubrication
Unless otherwise specified, actuators are shipped
packed with grease which should be sufficient for one
month of normal operation. For normal operation, the
actuator should be lubricated once a month using Shell
Albida
®
LC EP2 grease, (Shell Product Code 70311).
This grease has been thoroughly evaluated in Duff-
Norton actuators and has demonstrated superior lubricat-
ing properties affecting both wear life and maximum duty
cycle. Duff-Norton is not aware of an equivalent
grease. If this grease is not available in your area please
contact your local supplier for their recommendations.
Greases containing molybdenum disulfide should never
be used.
For severe service conditions, the actuators should
be lubricated more frequently using the above grease
(daily to weekly depending upon the conditions). If duty is
heavy, an automatic lubrication system is strongly
recommended.
Note
Lifting screws should never be run dry. Inspect
frequently at regular intervals to be certain that a lubrica-
tion film is present.
2-2.
Rebuild Procedure
Duff-Norton recommends the following procedures
for assembly and disassembly of machine screw
actuators.
1. Tag critical parts to facilitate reassembly.
2. Mark mating surfaces to ensure proper meshing.
3. Clean and lubricate all parts as required.
4. All seals must be replaced when rebuilding.
5. All screws, washers and other small common parts
must be replaced if damaged in any way.
6. Replace damaged or frozen lubrication fittings with
new ones.
Please Note: Only Duff-Norton factory supplied parts
should be used.
2-3.
Required Tools
A bearing puller and press, soft jaw table clamp and
common hand tools are necessary for proper assembly
and disassembly.
2-4.
Disassembly (Refer to Figure 3-1)
1. Remove lifting nut (23) from screw (5)
2. Remove set screws (1) from shell cap (2) and remove
shell cap from shell (3).
Note
It may be necessary to tap on shell cap (2) or shell (3)
with a hammer to loosen shell cap for removal.
These units are sealed with an expansion plug. If
necessary, these can be removed later.
3. Remove lifting screw (5) and gear (6) from shell (3).
4. Remove top bearing (7) which may be attached to
either shell cap (2) or worm gear (6).