8 commissioning, 9 operation, 10 maintenance and care – Festo Линейный привод с датчиком перемещения DFPI User Manual
Page 4: 11 disassembly and repair, 12 troubleshooting, 13 technical data
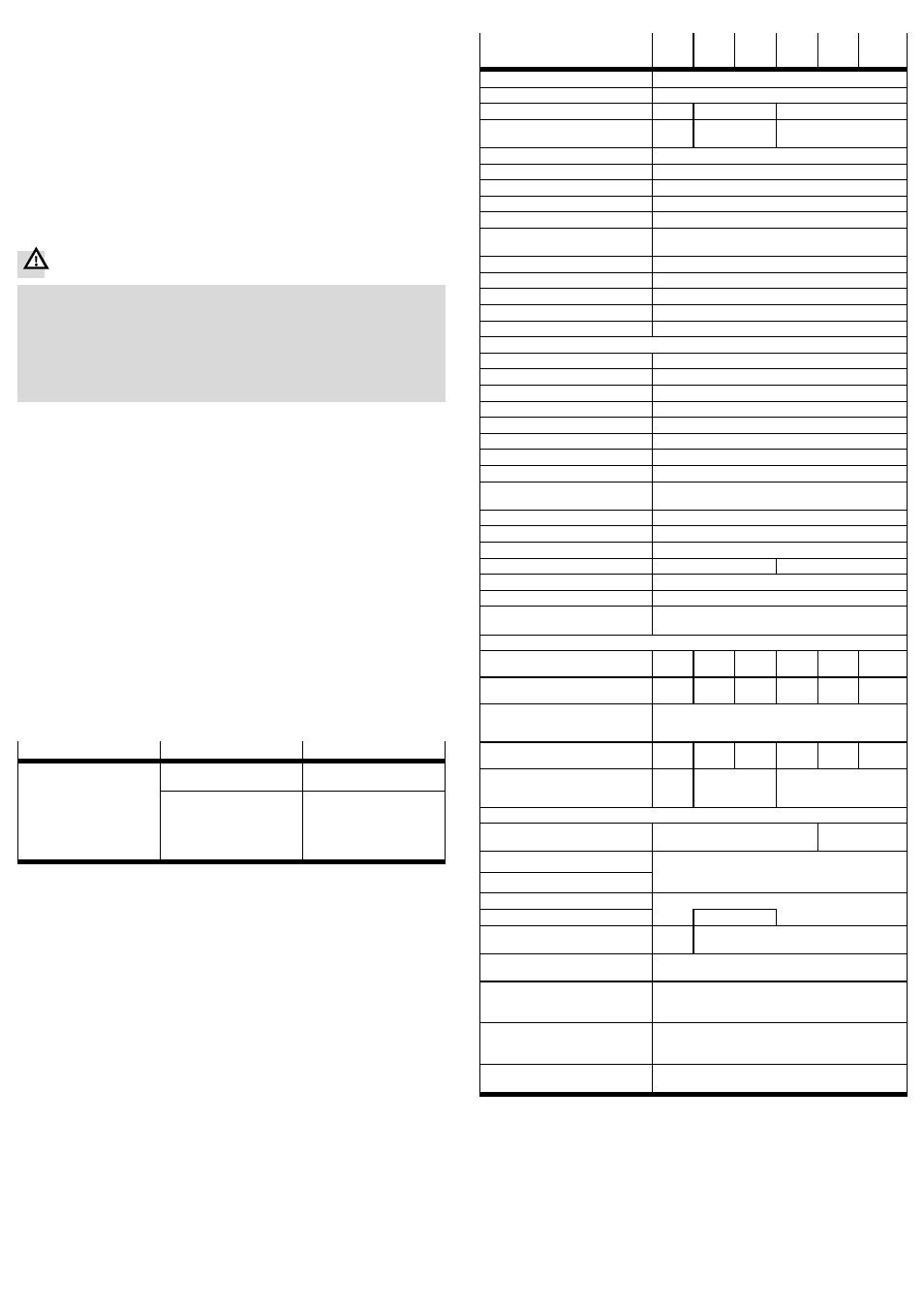
8
Commissioning
The product is ready for operation as soon as it is installed and connected.
• Make sure that the operating conditions lie within the permitted ranges (tech-
nical data
chapter 13).
• Make sure that a slide gate (process valve) attached to the linear drive can be
positioned without hindrance.
• If necessary, adjust the linear drive adapter attached to the piston rod. This
setting serves to optimise the opening or closing reaction of the connected
process valve or penstock valve.
• Slowly pressurise the linear drive.
For slow start-up pressurisation use soft-start valve type HEL.
• At first, select a slow travel speed.
9
Operation
Warning
Fast moving parts can cause injury to people in the vicinity of the DFPI.
• Make sure that, in the positioning range:
– Nobody can place his/her hand in the path of moving components (e.g. by
providing a protective guard).
– There are no foreign objects in the path of the moving components.
It should not be possible to touch the DFPI until the mass has come to a com-
plete rest.
10
Maintenance and care
If used as intended in the operating instructions, the device will be maintenance-
free.
11
Disassembly and repair
Make sure that the following energy sources are switched off:
– electrical power supply
– compressed air supply.
1. Remove the slide gate from the piston rod.
2. Remove the screws on the flange of the processing valve or penstock valve.
3. Remove the drive (if necessary including mounting adapter and coupling exten-
sion).
Recommendation: Send the product to our repair service. This way, the required
fine tuning and tests will be taken into special consideration.
Information about spare parts and accessories
www.festo.com/spareparts.
12
Troubleshooting
Malfunction
Possible cause
Remedy
Piston rod does not move in
the desired direction
Compressed air tubes inter-
changed
Correct the tubing connection
Displacement encoder cable
incorrectly connected at posi-
tioning controller or DFPI (e.g.
connections at pin 1 and pin 3
interchanged).
Correct the connection
Fig. 11
13
Technical data
DFPI-...-...-ND2P-E-P-G2
-100-
...
-125-
...
-160-
...
-200-
...
-250-
...
-320-
...
Based on standard
DIN 3358
Type of mounting
on flange in accordance with DIN 3358
Flange hole pattern
F07
F10
F10, F14
Width across flats, spanner
flat on the piston rod
22
27
36
Design
Piston rod, cylinder barrel
Cushioning
No cushioning
Mounting position
Any
Mode of operation
Double-acting
Position sensing
With integrated displacement encoder
Measuring principle of displacement
encoder
Potentiometer
Operating voltage range
[V DC]
0 … 15
Max. operating voltage
[V DC]
15
Independent linearity
[% FS]
±0.04
Hysteresis
[mm]
0.33
Repetition accuracy
[mm]
±0.12
Resistance value of displacement encoder (on the T.E.P.) dependent on the stroke length
1)
–
š 290 mm
[kΩ]
5
–
, 290 mm to 590 mm
[kΩ]
10
–
, 590 mm to 990 mm
[kΩ]
20
Electrical connection
3-pin; straight plug; screw terminal
Pneumatic connection
For tubing outside
∅ 8 mm
Operating pressure
[bar]
3 … 8
Nominal operating pressure
[bar]
6
Operating medium
Compressed air in accordance with ISO 8573-1:2010 [7:4:4]
Note on the operating medium
Operation with lubricated medium possible (in which case
lubricated operation will always be required)
Max. cable length
[m]
30
Protection class - in mounted status
IP65, IP67, IP68, IP69K, NEMA 4
Stroke
[mm]
40 … 990
Stroke reserve
[mm]
3
4
Ambient temperature
[°C]
–20 … +60
Relative air humidity
[%]
0 ... 100 condensing
Use in exterior
C1 – weather-protected areas in accordance with
IEC 60654
Product weight
– Basic weight with 0 mm
stroke
[g]
3476
5530
6529
13 946
22 569
35 359
– Additional weight per
10 mm stroke
[g]
80
145
159
187
325
399
– Additional weight
of displacement encoder
per 10 mm
[g]
2
– Moving mass
with 0 mm stroke
[g]
1228
1944
2250
4722
7059
11417
– Additional weight
of moving mass
per 10 mm stroke
[g]
27
52
87
Materials
– Cylinder barrel
Anodised wrought aluminium alloy
High-alloy
stainless steel
– Cap (end cap)
Anodised wrought aluminium alloy or
Anodised and painted wrought aluminium alloy or
Cast aluminium painted
– Bottom cap (bearing cap)
– Piston rod
High-alloy stainless steel
– Screws
Steel
2)
– Seals
NBR,
PU
NBR
Note on materials
Contains PWIS (paint-wetting impairment substances),
RoHS-compliant
Vibration resistance
in accordance with DIN/IEC 68,
Part 2-6
0.35 mm path at 10 ... 60 Hz;
5 g acceleration at 60 ... 150 Hz
Continuous shock resistance
in accordance with DIN/IEC 68,
Part 2-82
±15 g at 6 ms duration;
1000 shocks per direction
CE certification (see declaration of
conformity
www.festo.com)
in accordance with EU Explosion Protection Directive
(ATEX)
3)
1)
T.E.P. = theoretical electrical path
2)
Steel and high-alloy stainless steel
3)
Certification-specific special documentation must be considered (
www.festo.com/sp).
Fig. 12