Dow THERMAX™ Wall System User Manual
Page 4
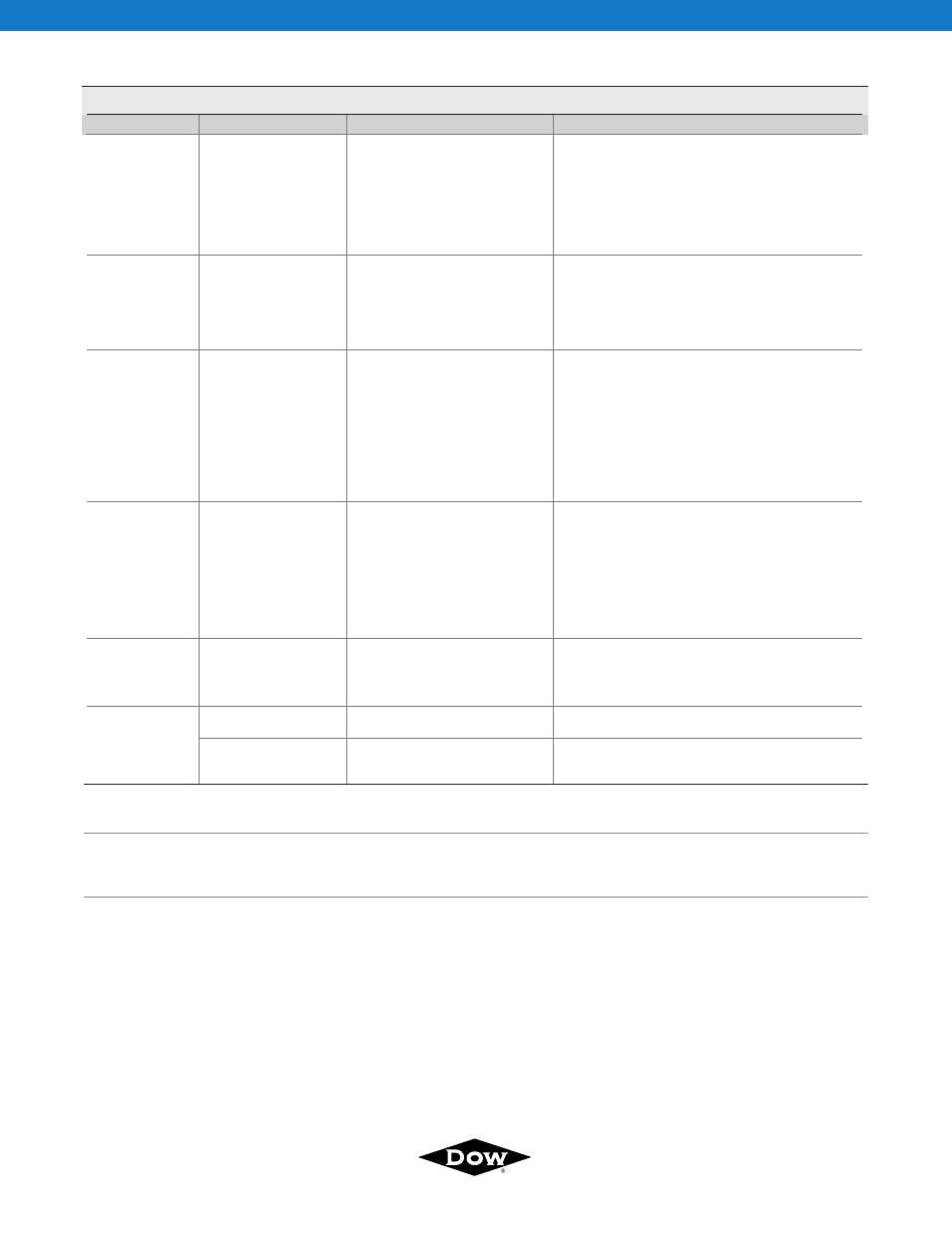
I N S T A L L A T I O N
I N F O R M A T I O N
.
C O M M E R C I A L
NOTICE: No freedom from any patent owned by Dow or others is to be inferred. Because use conditions and applicable laws may differ from one location to another and may change with time, Customer is responsible for
determining whether products and the information in this document are appropriate for Customer’s use and for ensuring that Customer’s workplace and disposal practices are in compliance with applicable laws and other
government enactments. The product shown in this literature may not be available for sale and/or available in all geographies where Dow is represented. The claims made may not have been approved for use in all countries or
regions. Dow assumes no obligation or liability for the information in this document. References to “Dow” or the “Company” mean the Dow legal entity selling the products to Customer unless otherwise expressly noted. NO
EXPRESS WARRANTIES ARE GIVEN EXCEPT FOR ANY APPLICABLE WRITTEN WARRANTIES SPECIFICALLY PROVIDED BY DOW. ALL IMPLIED WARRANTIES INCLUDING THOSE OF MERCHANTABILITY AND FITNESS
FOR A PARTICULAR PURPOSE ARE EXPRESSLY EXCLUDED.
Dow Polyisocyanurate Insulation
CAUTION: This product is combustible and shall only be used as specified by the local building code with respect to flame spread classification and to the use of a suitable thermal barrier. For more information, consult MSDS,
call Dow at 1-866-583-BLUE (2583) or contact your local building inspector. In an emergency, call 1-989-636-4400.
WARNING: Rigid foam insulation does not constitute a working walkable surface or qualify as a fall protection product.
STYROFOAM™ Brand Spray Polyurethane Foam contains isocyanate, hydrofluorocarbon blowing agent and polyol. Read the instructions and Material Safety Data Sheets carefully before use. Wear protective clothing, gloves,
goggles and proper respiratory protection. Supplied air or an approved air-purifying respirator equipped with an organic vapor sorbent and a particle filter is required to maintain exposure levels below ACGIH, OSHA, WEEL or
other applicable limits. Provide adequate ventilation. Contents under pressure. STYROFOAM™ Brand SPF should be installed by a trained SPF applicator.
Building and/or construction practices unrelated to building materials could greatly affect moisture and the potential for mold formation. No material supplier including Dow can give assurance that mold will not develop in any
specific system.
Printed in U.S.A.
®™Trademark of The Dow Chemical Company (“Dow”) or an affiliated company of Dow
Form No. 179-04074X-0811MCK
McKAY209737
www.thermaxwallsystem.com
Technical Information
1-866-583-BLUE (2583)
Sales Information
1-800-232-2436
IN THE U.S.
THE DOW CHEMICAL COMPANY
200 Larkin
Midland, MI 48674
Observation
Cause
Potential Issues
Potential Solutions
TABLE 2: STYROFOAM™ BRAND SPF TROUBLESHOOTING TIPS
(1)
1. Ensure drum transfer pumps are working properly
(steady static pressures).
2. Ensure that chemical filters are not plugged and the
check valves in the displacement pumps are operating
correctly (steady dynamic pressures). A low polyol level
will produce foam that is brittle and amber colored. A
low isocyanate level will produce foam that is spongy
and dark blue in color.
• Poor foam properties
• Excessive shrinkage
• Stud line cracking
Color changes
A/B off-ratio
1. Check the drum chemical temperatures and determine
if between 60°F and 90°F.
2. Determine if the dynamic pressures are approximately
800 psi or higher.
3. Determine if the chemical temperatures are between
115°F and 130°F.
• Poor foam properties
• Excessive shrinkage
• Stud line cracking
Color swirls
Poor mixing
1. Verify that drum temperatures are at the appropriate
temperature.
2. Determine whether the heater block has the capacity
to heat the chemicals to the temperature for spraying
at the desired rate.
3. Ensure the line temperatures are operating properly.
4. Ensure that the dynamic pressures are in the
recommended ranges.
5. Minimize exposure of the line to direct sunlight or
severe cold.
• Poor yield
• Poor foam properties
• Excessive shrinkage
• Stud line cracking
Faster/slower than
normal cream
High/low chemical
temperatures; high/low
chemical pressures
1. Check the drum chemical temperatures and determine
if between 60°F and 90°F.
2. Determine if the dynamic pressures are approximately
800 psi or higher.
3. Determine if the chemical temperatures are between
115°F and 130°F.
4. Clean gun tip or remove and soak gun’s mixing chamber.
If mixing chamber cannot be cleaned with solvents, a
burn-out oven may be required.
• Poor yield
• Poor foam properties
• Excessive shrinkage
• Stud line cracking
Non-circular or
smaller/larger than
usual spray pattern
Plugging; high/low
chemical temperatures or
high/low pressures
Foam reversion occurs when the mixing chemicals exit the
gun as a froth or foam and then collapse. This is often due
to excessively high temperature leading to boiling of the
blowing agent in the mixing chamber.
• Poor yield
• Poor foam properties
• Excessive shrinkage
• Stud line cracking
Foam reversion
High chemical
temperatures
Clean the substrate.
Poor adhesion
Poor wetting of the
substrate
Dirty substrate
Prime the substrate.
Substrate incompatible
with SPF
(1) Contact equipment supplier if you are unfamiliar with equipment maintenance or these troubleshooting tips.
Poor adhesion