Permanent magnet motors quick set-up – Beijer Electronics AN-BEI-P2-050 User Manual
Page 8
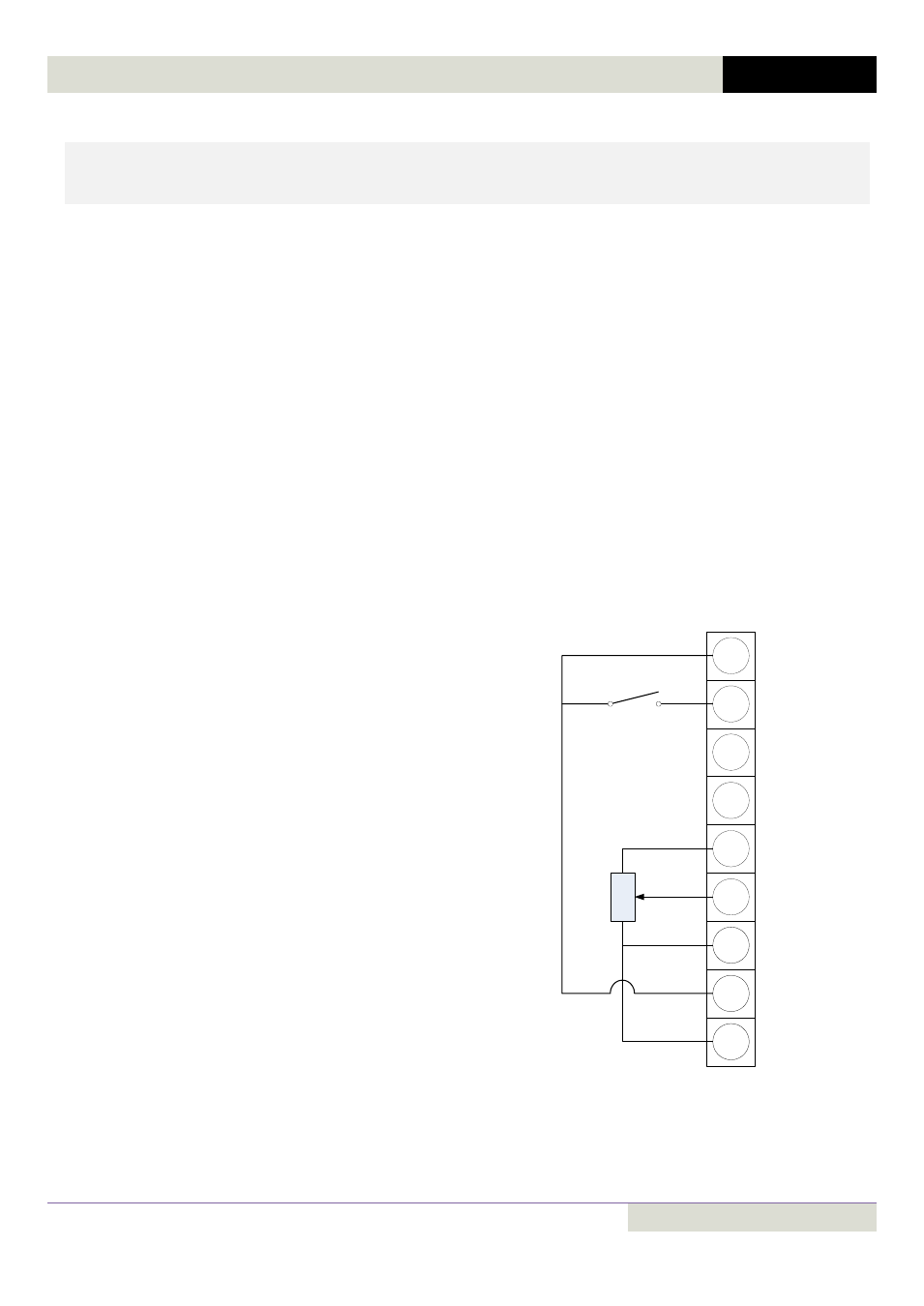
APPLICATION NOTE AN-BEI-P2-050
Date: 15/02/12
AN-BEI-P2-050 Open Loop Permanent Magnet Motor Control
8
Permanent magnet motors quick set-up:
The quick start is intended as a basic first step to successfully running the motor. For Optimum performance the
full programming and optimisation procedure should be followed.
Quick Step 1: Setting of the required parameters
Set the following parameters in the sequence they are listed.
P1-07: Nominal back emf (rms Phase-Phase)
-
= Motor Dependant
P1-08: Motor rated current (rms Phase) -
-
= Motor Dependant
P1-09: Motor rated frequency (Hz)
-
-
= Motor Dependant
P1-10: Motor rated speed (rpm) -
-
-
= Motor Dependant
P1-14: Parameter access code -
-
-
= 201
P2-24: Switching frequency (kHz)
-
-
= 16
P4-01: Control Mode
-
-
-
-
= 3
P4-03: Speed Controller proportional Gain (%) -
= 50
P4-04: Speed Controller integral time constant (ms)
= 100
Quick Step 2: Complete Auto-tune function
Note: Safe Torque Off input (terminal 12 and 13) needs to be connected in order to enable the safe torque off
function and allow auto-tune and motor control. See connection diagram below.
Set the following parameter. Drive will perform auto-tune on exit of parameter entry.
P4-02: Auto-tune Function
-
-
= 1
Wait for completion of auto-tune.
Quick Step 3: Check motor operation
Apply enable and speed set-point inputs to the Beijer
Frequency Inverter P2 P-2 Default configuration is shown right.
Vary speed set-point and check smooth operation of the motor.
Optional:
To set Beijer Frequency Inverter P2 in keypad mode set
parameter P12 = 1 Beijer Frequency Inverter P2 can now be
controlled direct from the keypad.
Quick Step 4: Set Current magnetising time
Set the following parameter to adjust Current magnetising time.
P7-12: Current magnetising time
Adjust upward if the rotor cannot be seen to orientate on start
up.
Adjust downward if a significant delay follows the orientation
of the rotor on start up.
Quick Step 5: Set Low speed boost parameters
Check low speed operation of the motor. If torque performance
at low speed needs adjustment set the following values.
P7-14: Boost Current Level
-
-
= 25%
P7-14: Boost Frequency
-
-
= 10%
Values should be optimised following on from the quick start procedure.
1
2
3
4
5
6
7
P1-12 = 0
P1-13 = 1
Input 1:
O: Stop (Disable)
C: Run (Enable)
Input 3:
Enable
Imput 2:
+24V Output
+10V Output
0V
Analog Speed Ref
12
13
Safe Torque Off Input
Safe Torque Off 0V