System information, 1 description and theory of operation – Pulsafeeder PULSAlarm User Manual
Page 5
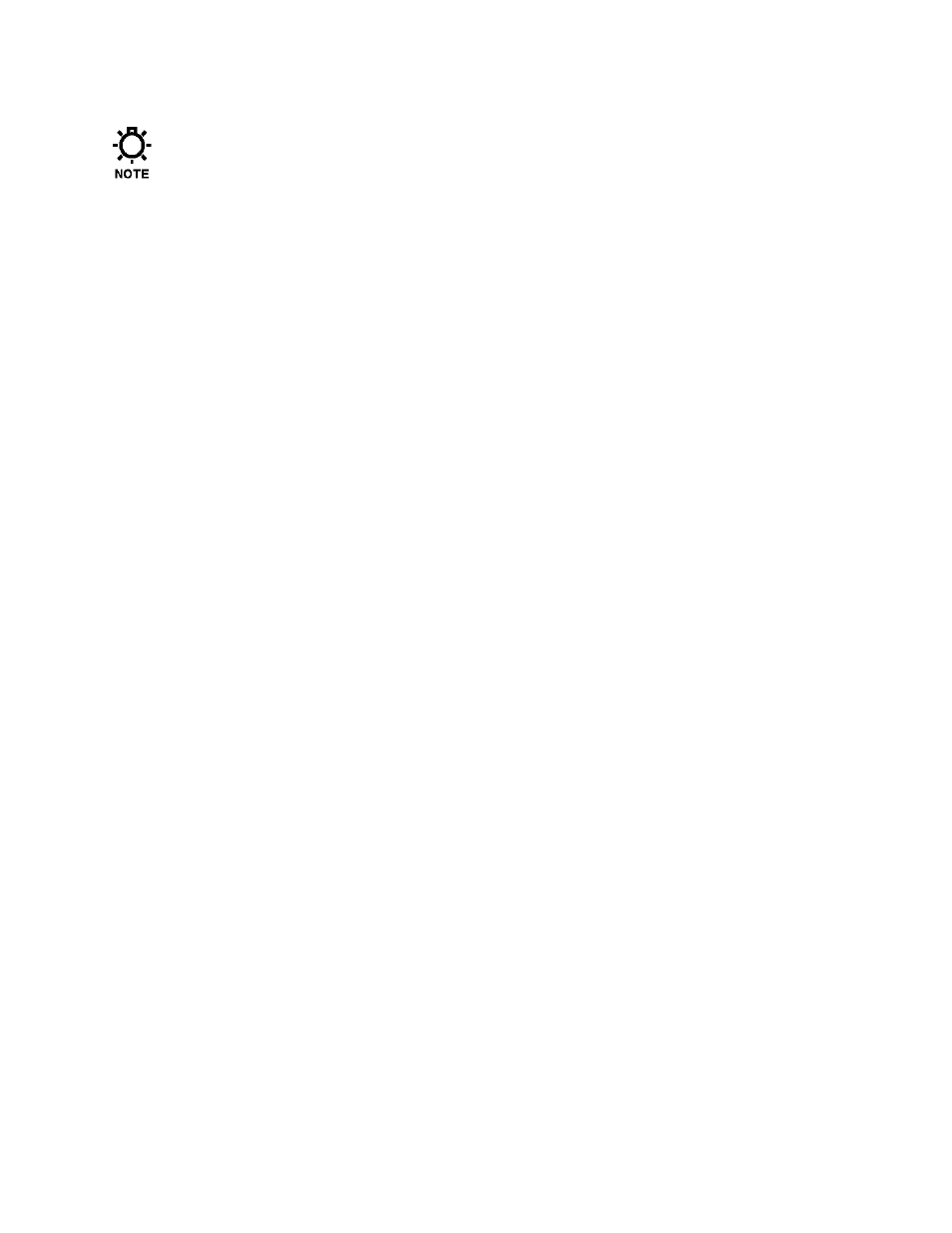
5
For information on overall pump operation and maintenance, refer to the
Installation, Operation, and Maintenance manual specific to the model of pump in
question. The information in this bulletin pertains only to the PULSAlarm leak
detection system supplied as an option on Pulsafeeder PULSA Series pumps.
1. System Information
1.1
Description and Theory of Operation
The PULSAlarm leak detection system utilizes a two-layer PTFE diaphragm, coupled to a pressure
or vacuum switch.
For the vacuum-based option, a vacuum is drawn between the two layers of the diaphragm
assembly. During normal operation, vacuum is maintained. If there is a failure of either layer of
the diaphragm, the vacuum is lost. When the vacuum reaches a set value, the sensing switch is
trigger to signal an alarm. This system allows for simple setup, however the vacuum will leak
down over time under normal conditions. The system will need to have this vacuum occasionally
renewed during operation.
For the pressure-based option, the system is initially primed by filling the void within the detection
assembly and between the diaphragm layers with a barrier fluid. The setup process then bleeds
excess fluid from between the diaphragm layers until they are in close contact. The system operates
as follows:
During normal pump operation, the two layers of the PTFE diaphragm bear directly against one
another, and there is no pressure generated between the two layers. The sensing system monitors
the space between the layers, which will remain at zero pressure as long as the diaphragm layers
remain undamaged.
In the event of a failure of either layer of the diaphragm, liquid will enter the space between the two
layers. This liquid will be either the hydraulic oil (if the rear layer fails) or the pumped fluid (if the
front layer fails). As the pump operates, this liquid will generate pressure between the layers of the
diaphragm that will then be transferred outwards by the barrier fluid. This fluid will create pressure
against the pressure switch. This switch has a trip point of 5 psi (0.34 bar). When this pressure is
reached the switch will operate. The pressure system requires a more complex setup procedure,
however once operational it should require no further maintenance or operator interaction.
The output of the switch on either system (both normally closed and normally open connections are
available) can then signal the failure of the diaphragm. It is recommended that the pump be
stopped in the event a leak is detected. Immediate attention to the problem, followed by cleanup
and appropriate maintenance, will avoid further damage to the pump.
The barrier fluid used with the pressure-based system should be chosen for compatibility with the
process and environmental conditions. The fluid chosen should have as low a viscosity as possible
to aid in priming the system. Water can be used, and ethylene or propylene glycol can be added for
corrosion and temperature protection. Thin oils such as silicone oil or mineral oil can also be used.
Liquids of higher viscosity will extend the time required to properly prime the system. Thinner
liquids will allow for faster setup. Pulsafeeder supplies as standard a low viscosity silicone oil.
System identification (vacuum or pressure based) is noted on the switch cover nameplate, and also
on your Pulsa Series pump Specification Data Sheet.