Amana VR8205 User Manual
Page 28
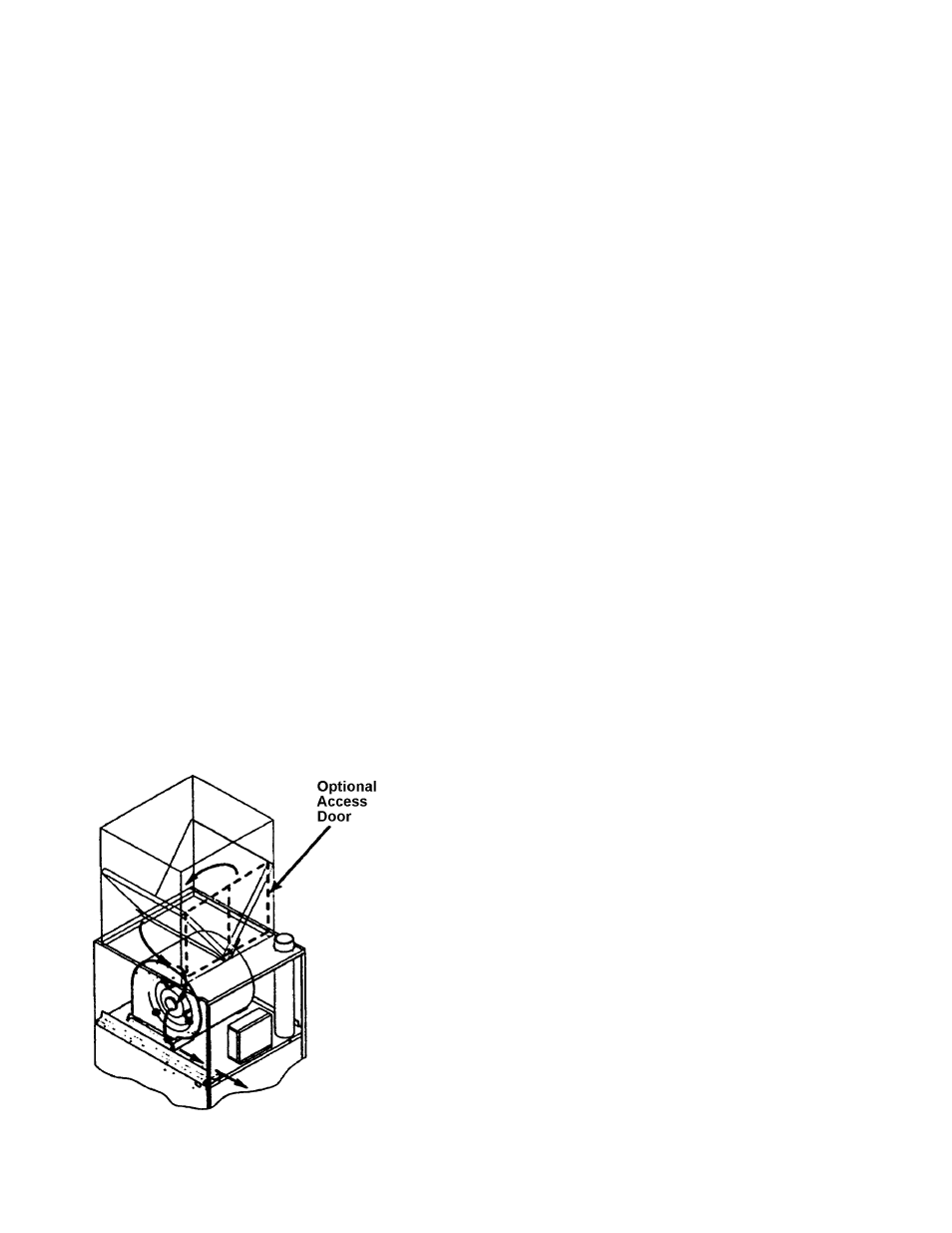
28
The furnace-mounted filter rack includes a rack mounted
on the top of the furnace. Two filters fit into the rack and rest
against the sides of the return air plenum, forming a “V”
above the furnace.
The filters should be inspected frequently and cleaned or
replaced when necessary. In some installations, the filters
can be inspected after disconnecting the electrical power
and removing the optional access door in the return air
plenum. If this access panel is not present, proceed as
follows:
1. Disconnect the electrical power.
2. Remove the non-louvered door from the furnace.
3. Remove the left filter by reaching to the left side of the
blower, pushing the filter up slightly to remove it from
the filter rack, and pulling it down to the left of the blower
and out the blower door. Repeat with the right filter.
4a. Dirty throwaway filters must be replaced with the same
filter type and size.
4b. Dirty, permanent metal filters must be cleaned as
follows:
Wash, rinse, and dry the permanent filters. Both sides
should then be sprayed with a filter adhesive as is
recommended on the adhesive container. Many hard-
ware stores stock spray adhesives for use with perma-
nent filters.
If badly torn or uncleanable, these filters must be
replaced by equal size permanent, high velocity filters.
Throwaway filters must not be used as replacement for
permanent filters. Under normal use, permanent filters
should last for several years.
5. To reinstall the filters, first MAKE CERTAIN THE
AIRFLOW DIRECTION ARROW POINTS TOWARDS
THE FURNACE. Then insert the filters from the left side
of the blower. Starting with the right filter, push the filter
into the plenum so that the bottom of the filter rests in
the filter rack and the upper edge rests against the side
of the plenum. Repeat with the left filter (Figure 44).
6. Replace the blower door, then reconnect the electrical
power.
Figure 44
Furnace mounted Filter Rack
(Counterflow)
BLOWER MOTOR
The air circulating blower motor bearings are permanently
lubricated. No further lubrication is required.
INDUCED DRAFT BLOWER MOTOR
The induced draft blower motor is permanently lubricated.
No further lubrication is required.
FLAME SENSOR (INTEGRATED IGNITION CONTROL)
(QUALIFIED SERVICER ONLY)
The fuel or combustion air supply can create a nearly
invisible coating on the flame sensor. This coating acts as
an insulator, causing a drop in the flame sensing signal. To
remove this coating, a qualified servicer should carefully
clean the flame sensor with emery cloth or steel wool. After
cleaning, the microamp signal should be in the range listed
in Specification Sheet.
IGNITOR (QUALIFIED SERVICER ONLY)
If the ignitor and the surrounding air are at about 70°F and
the ignitor wires are not connected to any other electrical
components, the resistance of the ignitor should not ex-
ceed 200 ohms. If it does, the ignitor should be replaced.
FLUE PASSAGES (QUALIFIED SERVICER ONLY)
At the start of each heating season, inspect and if nec-
essary, clean the furnace flue passages.
CLEANING FLUE PASSAGES (QUALIFIED SERVICER
ONLY)
1. Shut off electric power and gas supply to the furnace.
2. Remove burner assembly by disconnecting the gas line
and removing the manifold brackets from the partition
panel.
3. Remove the flue from the induced draft blower and the
collector box from the partition panel.
4. The primary heat exchanger tubes can be cleaned
using a round wire brush attached to a length of high
grade stainless steel cable, such as drain cleanout
cable. Attach a variable speed reversible drill to the
other end of the spring cable. Slowly rotate the cable
with the drill and insert it into one of the primary heat
exchanger tubes. While reversing the drill, work the
cable in and out several times to obtain sufficient
cleaning. Use a large cable for the large tube, and then
repeat the operation with a small cable for the smaller
tube. Repeat for each tube.
5. When all heat exchanger tubes have been cleaned,
replace the parts in the reverse order in which they
were removed.
6. To reduce the chances of repeated fouling of the heat
exchanger, perform the steps listed in Section X,
Start-
up, Adjustments, and Checks.