Midco Unipower A-Series User Manual
Page 12
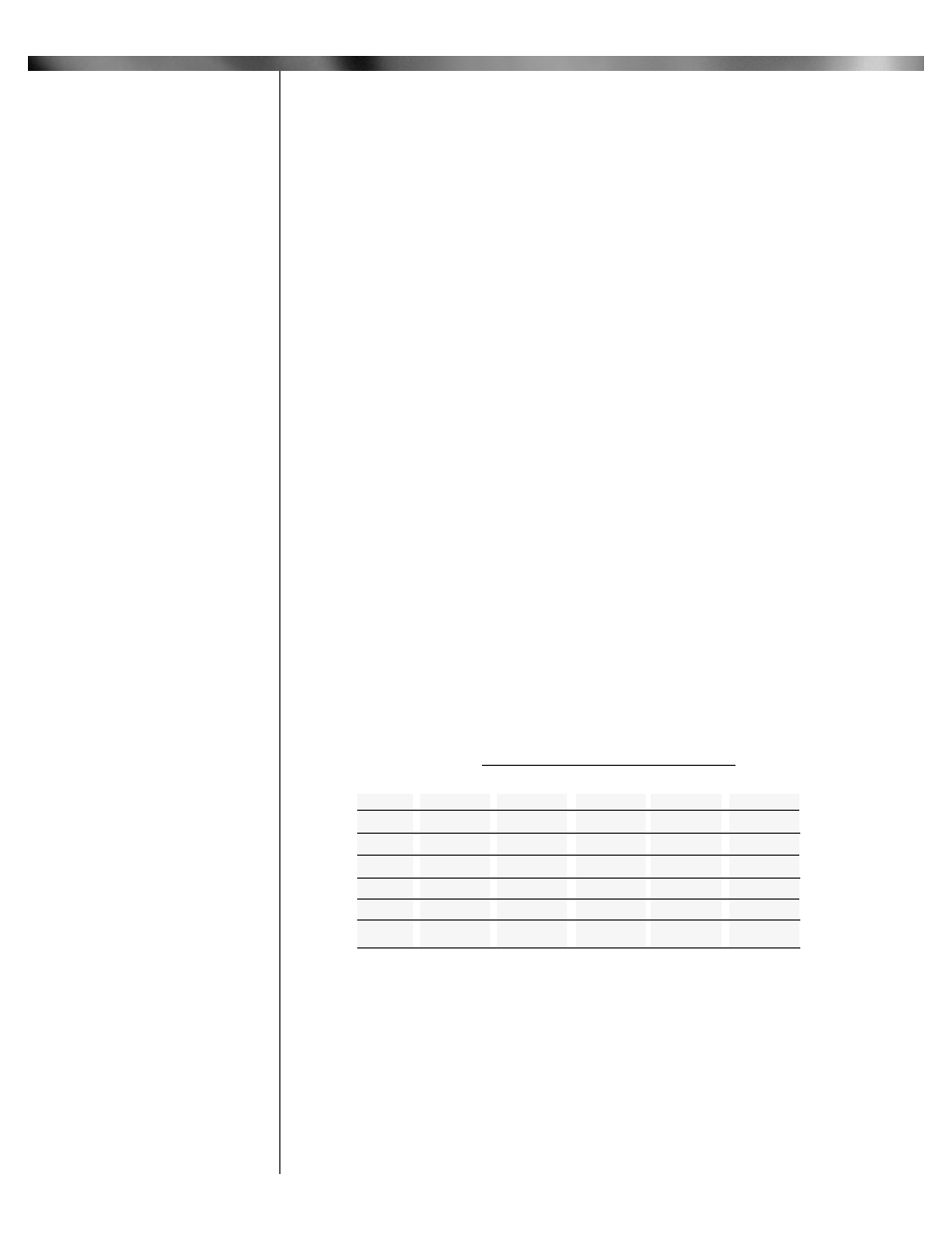
V5055 Valve Body with
Motorized Actuator Cont.
XIV Automatic Gas
Valve Leak Test
XV Flame Safeguard
XVI Special Equipment
■
■
■
■
Do not disassemble the valve actuator, it is not field repairable. If malfunction occurs, replace
the entire actuator.
1.
Turn off power to burner.
2.
Fully close the manual test cock (located downstream of the gas input adjuster.
3.
Remove the
1
/
8
" pipe plug from the test tap located:
a. with diaphragm valve (in one of the pipes nipples between the valve and test cocks, or
b. with motorized valve (in the bottom of the valve body on its downstream side, or in the
tee connecting the high gas pressure switch tube to the valve train.
4.
Install a pet cock in the test tap and attach a short length of
1
/
4
" flexible tubing. The open
end of the tubing should be cut at a 45° angle.
5.
Immerse the open end of the tubing to a depth of
1
/
2
" in a container of water.
6.
Open the pet cock. If bubbles appear, wait until the rate stabilizes, then count the number
appearing in ten seconds. An excess of 23 bubbles over a ten second period (approximately
.023 CFH of gas) indicates that the valve should be repaired or replaced.
7.
If there are two automatic gas valves in the valve train, check the downstream valve first and
then the upstream valve. Use the appropriate tap in one of the motorized valve bodies, or
when a diaphragm and solenoid valve are furnished, in the pipe nipple between the valves.
8.
After the test is completed, be sure to replug the test taps and fully open the test cock.
■
■
■
■
Standard Unipower burners are equipped with a Honeywell RM7895 microprocessor based
burner control, employing a flame rectification system of flame detection. Burner construction for
special codes and/or insurance requirements such as Factory Mutual or Industrial Risk Insurers (IRI)
may require alternate controls. Refer to Section XV Special Equipment. A safe start and run
control sequence is provided with instantaneous response to presence or loss of flame signal.
Flame failure response time is 3 seconds. Pilot Flame Establishing Period (PFEP) is field selectable
from 4 or 10 seconds. The RM7895 features a pre-purge time (30 seconds for On-Off, 90
seconds for 2-Step or Modulating burners) and a plug-in amplifier. An airflow circuit is also field
selectable to allow either lockout or recycle upon loss of airflow. Five LED's (light emitting diodes)
are provided to display sequence information. Refer to the Honeywell RM7895 literature for
detailed operating information, configuration requirements, testing and service.
■
■
■
■
Special Equipment, such as high-low gas pressure switches, main valve, proof of closure
switches etc., can affect the start-up and operation of the burner. Refer to your burner wiring
diagram and specific start-up instructions, as well as equipment manufacturer's literature included
with the burner for further information.
■
■
■
■
If any doubt exists concerning burner operation when special equipment is involved, contact
the installing contractor or Midco International Inc.
Burner
Model
0" W.C.
.25" W.C.
.50" W.C.
.75" W.C.
1.0" W.C.
A50G
A52G
A53G
A55G
A73G
A75G
A77G
1500
2000
2500
3000
4200
5000
6000
—
—
—
—
4200
5000
5800
1300
1700
2500
2800
4000
5000
5600
—
—
—
—
3850
5000
5400
*
1525
2500
2575
3650
5000
5200
Combustion Chamber Back Pressure
Table 6: Maximum Capacities at Specified Back Pressures
12