Part 1 installation part 2 service – Midco J121-DS User Manual
Page 8
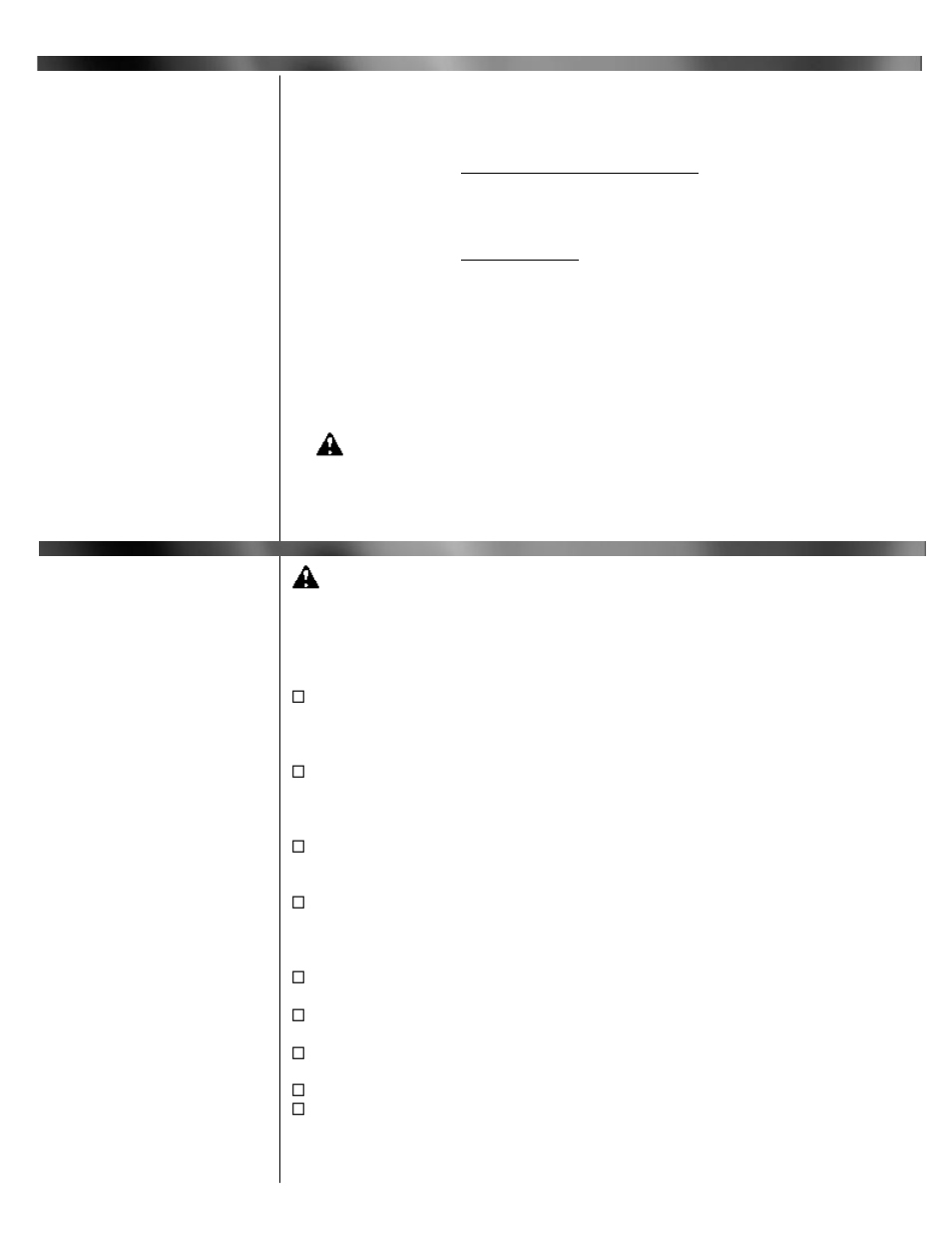
12. The actual NATURAL gas firing rate in BTU per hour can be determined by
timing the gas meter. Accurately time the meter test dial for one revolution,
convert to hourly cubic feet and multiply by the BTU per cubic foot value of your
gas per formula:
3600 X Test dial Size x BTU Value
= BTU / Hr.
No.of Seconds for One Rev. Test Dial
Then divide by 1,000 for MBH value.
EXAMPLE:
3600 x 1 x 1000*
= 180,000 BTU / Hr. = 180 MBH
20
* Approximate BTU Value
13. Start and stop the burner several times to check its operation with the charging
door open, and then with it closed. Remove any temporary Door Open
bypasses installed in Step 6.
14. Test operation of any auxiliary operating and/or limit controls.
15. Load incinerator and make trial run. Confirm that the incineration chamber
pressure stays within the range of 0 to minus 0.5"W.C.
16.
WARNING: When the incinerator is located inside a building and a
draft control is used, check that there is no spillage of flue products from
the draft control.
17. To shut off: Turn Burner Switch or Timer off and close Main Manual Shut -Off
Valve
WARNING: BE SURE THAT THE MANUAL VALVE AND BURNER
DISCONNECT SWITCH ARE TURNED OFF BEFORE ANY PARTS ARE
REMOVED FOR SERVICE.
The Ignitor and Regulator Assembly is removed as a unit. Disconnect the ignitor gas
line and electrode wires, remove the two mounting screws and pull out the assembly.
When the ignitor gas pressure is in the proper range (see Table 3) and the
electrodes are adjusted to the dimensions shown in Figure 5, any ignition problems
are usually caused by lint, dust, corrosion, cracked electrode insulators, foreign
matter in the blast tube or deterioration of ignitor ports in Retention Plate.
Ignitor trouble will be evidenced by failure of main burner ignition. It may cause
frequent Electronic Control lockout. Check for dirt in the ignitor air and mixture
passageways and check for obstructions in the ignitor ports. Also check electrode
adjustments (see Figure 5). Replace any severely burned parts.
Proper operation of the flame sensor rod can be checked by measuring the flame
current. With the Electronic Control energized, a good reading should run steady 2 or
more microamps.
When servicing, clean the Ignitor Retention Plate ports and blow out the internal air
and gas passages. Clean the Electrode Insulators and check them for hairline cracks.
Also check the electrode ends and the Ground Barrier for serious corrosion or loss of
metal. Replace any defective parts.
Make sure that there is no debris in the Blast Tube that could short out the Spark
or Flame Electrode.
Clean the Ignitor Gas Orifice in Tee Orifice Fitting (see Figure 5) and check that the
orifice size is correct per Table 3.
Check that the electrode ends are positioned and that the gap between the end of
each electrode and the ground barrier is spaced per Figure 5.
Check that the Ignitor Air Deflector is at the correct angle (45°). See Figure 4.
Inspect the electrode wire insulation for cracks or worn areas, or any contact with
the burner frame. Dampness will facilitate electrical leakage to ground, which will
cause ignition or flame signal failure.
8
Part 1 Installation
Part 2 Service
Part 1
Installation
Continued
Part 2
Service
VIII Ignitor and Regulator
Assembly