Part 1 installation – Midco EC200 & EC300 User Manual
Page 3
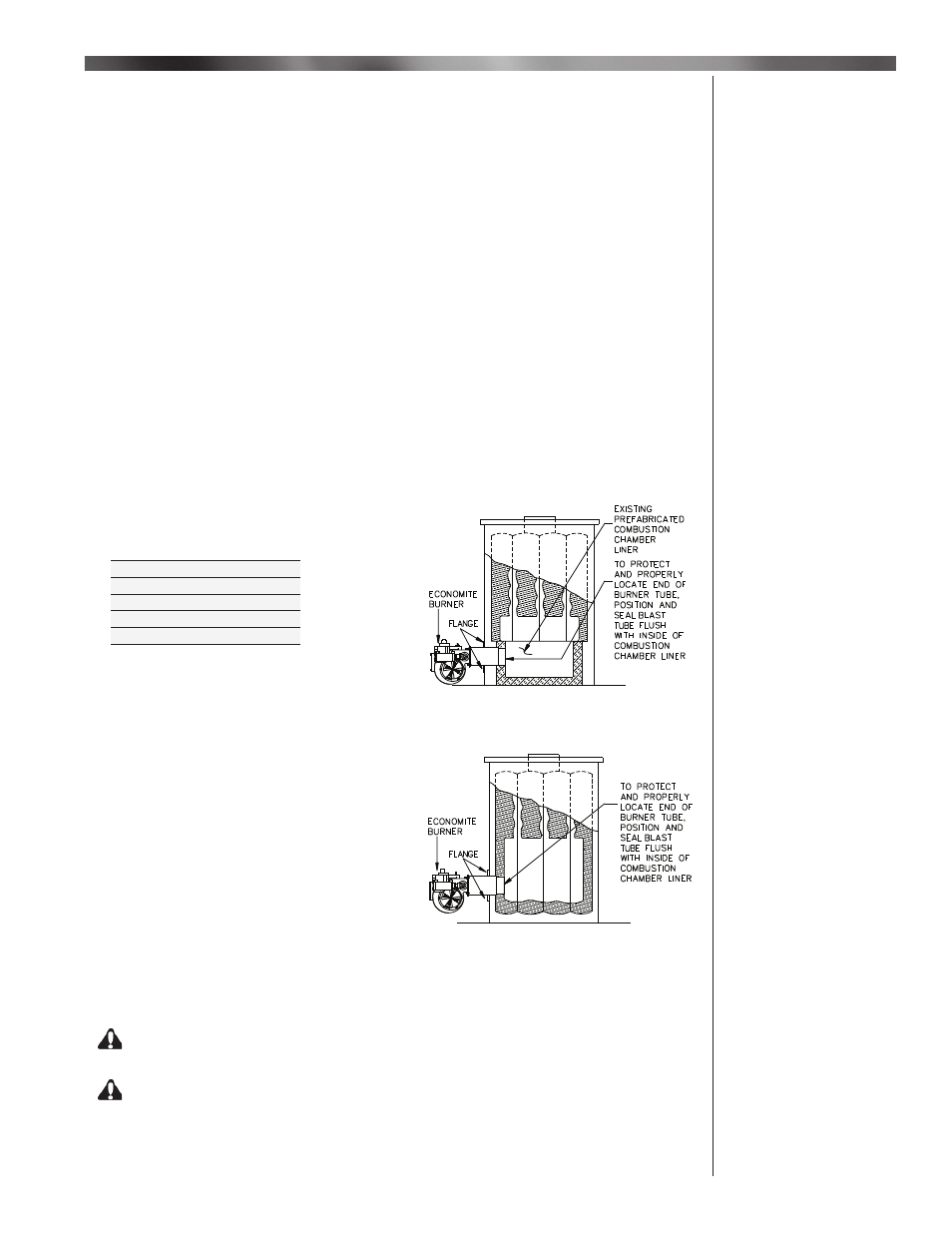
Midco International Inc.
3
8471 38
Part 1 Installation
III - Combustion Chamber
II - Preparation of the Gas
Utilization Equipment
free area per 2,000 BTU. In any case, the minimum dimension of rectangular air ducts shall not be
less than 3 inches.
-
In Canada, for detailed ventilation requirements, refer to standard CAN/CGA 1-B149.1 or .2
and/or local codes.
___________________________
-
Clean the appliance, heat exchanger interior, combustion chamber, and fl ue connections.
Remove all adhering tars, scale, dirt and soot. Inspect for actual leaks and/or potential leaks.
-
Cement all joints, including those in the gas utilization equipment base and around door frames,
to prevent leakage into or out of the combustion chamber.
-
The access or fi ring door should open easily to relieve pressure. If positive latches exist, they
should be modifi ed to permit easy opening; a spring loaded door holder is recommended.
-
On all boilers, make certain the pressure relief safety valve is in good operating condition.
___________________________
A combustion chamber liner is normally required to protect non-heat transfer surfaces and to provide
a radiant bed for rapid heat transfer to the primary surfaces of the heat exchanger. In most cases,
an existing oil burner combustion chamber liner can be used, if in good condition.
- Install
mounting
fl ange to the burner blast tube. The distance from the fl ange to the blast
tube edge should be same as the gas utilization equipment wall thickness plus the fl ange gasket
thickness. This will allow the burner blast tube to be fl ush with the inner chamber wall after the
burner is installed. If the blast tube extends into the combustion chamber serious damage to the
burner may occur, voiding the warranty, see Figure 1 & 2 for reference. For minimum combustion
chamber dimensions see Table 1.
Gas Input
Width/
MBH*
Height ″ Length ″
100
8″
8″
150
9″
9″
200
10″
10″
250
10″
10″
300
10″
11″
-
Mount the burner to the appliance. Use the
supplied gasket to assure a tight seal between the
mounting fl ange and front plate gasket.
-
With a wet base boiler, where the entire
combustion chamber is comprised of heat exchange
surfaces and no combustion chamber liner was
provided for oil fi ring, a liner is usually not required.
A liner or target wall may be necessary if the
combustion chamber is unusually short.
To avoid fl ame contact on the heat exchanger walls
or fl ueways.
-
Use 2300°F minimum insulating material
when the application requires the construction or
replacement of a combustion chamber liner
-
The burner tube must be sealed air tight into the
combustion chamber liner opening with refractory
material as shown by Figures 1 and 2.
CAUTION: In no case should the burner tube be allowed to extend into the
combustion chamber; it must be set fl ush with the inside surface.
WARNING: Burner cabinet must be mounted in orientation shown in Figures 1 and
2. Any other mounting may cause a dangerous condition, and will void burner warranty and
agency approvals. Non-standard arrangements may be available for some models; consult
factory for details if required.
I - Ventilation
Continued
Figure 1: Dry Base Boiler with Combustion
Chamber Liner
(Similar to Warm Air Furnace Construction)
Table 1: Minimum Combustion
Chamber Dimensions
* 1 MBH = 1,000 BTU/Hr
Figure 2: Wet Base Boiler with Combustion
Chamber Unlined
Source: ANSI Z21.8b 1993, Installation of Domestic
Gas Conversion Burners. For other applications,
consult factory.