AMETEK 955 eBrik User Manual
Page 3
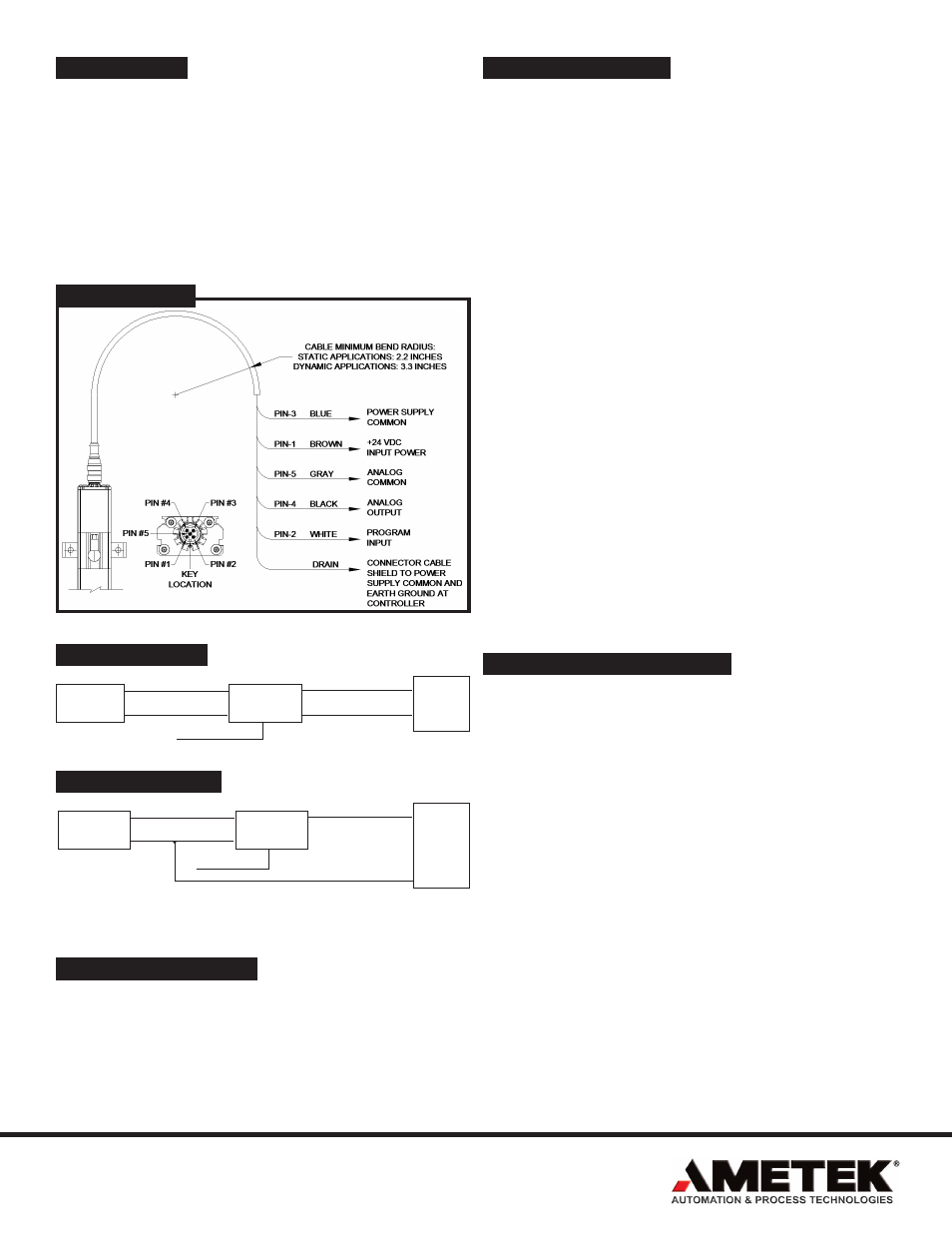
For customer service or technical support
call Toll Free 800-635-0289
There are two common methods for wiring the 955 eBrik™ to a customer
supplied interface device, such as a PLC or panel meter. The two different
methods are commonly referred to as Single Ended Input or Differential
Input. Differential Input is the preferred wiring method. With the Differential
Input, the Analog Common wire is connected to the customer supplied input
device and the Power Supply Common is wired separately to the customers
supplied power source. When wired using the Differential method, the
electrical noise and voltage offset errors produced by the currents running
through the Power Supply Common are eliminated. The Power Supply
Common and Analog Common are internally connected inside of the 955
eBrik™ LDT.
The Automatic Gain Control feature will automatically search and find the
magnet on power up. If power is applied without a magnet on the LDT, turn
power off and place magnet within the active stroke area. Re-apply power. If
using the Floating magnet option, the magnet should be placed within ¼” of
the LDT’s sensing surface, and must be within the active region of the LDT
when power is applied.
Typical Wiring
Setting ZERO & SPAN
Manual Setting ZERO & SPAN
Automatic Gain Control
Wiring Diagram
Differential Input
Single Ended Input
Power +
Supply
_
955e
LDT
+ Input
- Input
Customer Supplied Power (Brown)
Power Supply Common (Blue)
Position Output (Black)
Position Common (Gray)
Program Input (White)
Power
+
Supply
_
955e
LDT
+ Input
Common
Customer Supplied Power (Brown)
Power Supply Common
Position Output (Black)
Program Input
(White)
(Blue)
Note: The 955e is current sourcing, which allows the current to flow from
the LDT into the user’s equipment.
If the programming feature was ordered the 955 eBrik™ is programmable
over the entire active stroke length of the LDT. The unit can easily be
changed in the field from a 0 to 10VDC to a 10 to 0VDC or 4 to 20mA to a 20
to 4mA. Keep in mind that there is a 2.75” Null area at the connector end of
the LDT and a 2.75” Dead band at the other end of the LDT that the magnet
must stay out of at all times.
The units come fully programmed from the factory and do not require re-
programming unless desired. The units are 100% absolute and will not lose
programmed parameters on power loss. The Zero and Span points can be
programmed in any order and anywhere within the LDT's active sensor area.
NOTE 1: Zero or Span can be adjusted individually without setting the other.
NOTE 2: Zero = 0V on 0-10 VDC units and 4mA on 4-20mA units. There is
a timing sequence that is used to unlock the probe for programming. This is
to ensure that the Span cannot be accidentally re-programmed by someone
in the field.
Before programming the Zero or Span, the program input must be connected
to the Power Supply Common for a minimum of 2 seconds and no more
than 6 seconds, and then released for 1 second. The LDT programming
sequence is now unlocked and will remain an unlocked unit until either the
Zero or Span is programmed or the 10 second programming sequence times
out. During the unlock mode either the Zero or Span can be programmed
by momentarily connecting the Program Input to either the Power Supply
Common or Power Supply +. NOTE: The LDT must be unlocked to program
the Zero and unlocked again to program the Span. Once either the Zero
or Span is programmed, the LDT will go back into the locked mode. To
program the Zero or Span, the program input must be connected to the
Power Supply Common for 4 seconds, and then released for 1 second.
Within the next 5 seconds, you can program either the Zero or the Span
by momentarily connecting the Program Input to either the Power Supply
Common or Power Supply +VDC.
WARNING: During normal operation, electrically insulate the White
Program wire to prevent accidental setting of Span.
To set the Zero and Span position, follow these steps:
1. Apply power to the LDT
2. Place magnet assembly where Zero is to be located, but within the
active region of the probe.
3. Short the Program Input pin to the Power Supply Common for 4
seconds. Remove the short for 1 second. Within 5 seconds, short
the Programming Input pin to the Power Supply Common. This
completes the Zero programming process.
4. Place magnet assembly where Span is to be located, but within the
active region of the probe.
5. Short the Program Input pin to the Power Supply Common for 4
seconds. Remove the short for 1 second. Within 5 seconds, short
the Programming Input pin to the Power Supply +VDC. This
completes the programming process.