0 troubleshooting, 0 troubleshooting table, Operating and installation instructions stobu – ARI Armaturen STOBU PN63-160 EN User Manual
Page 15
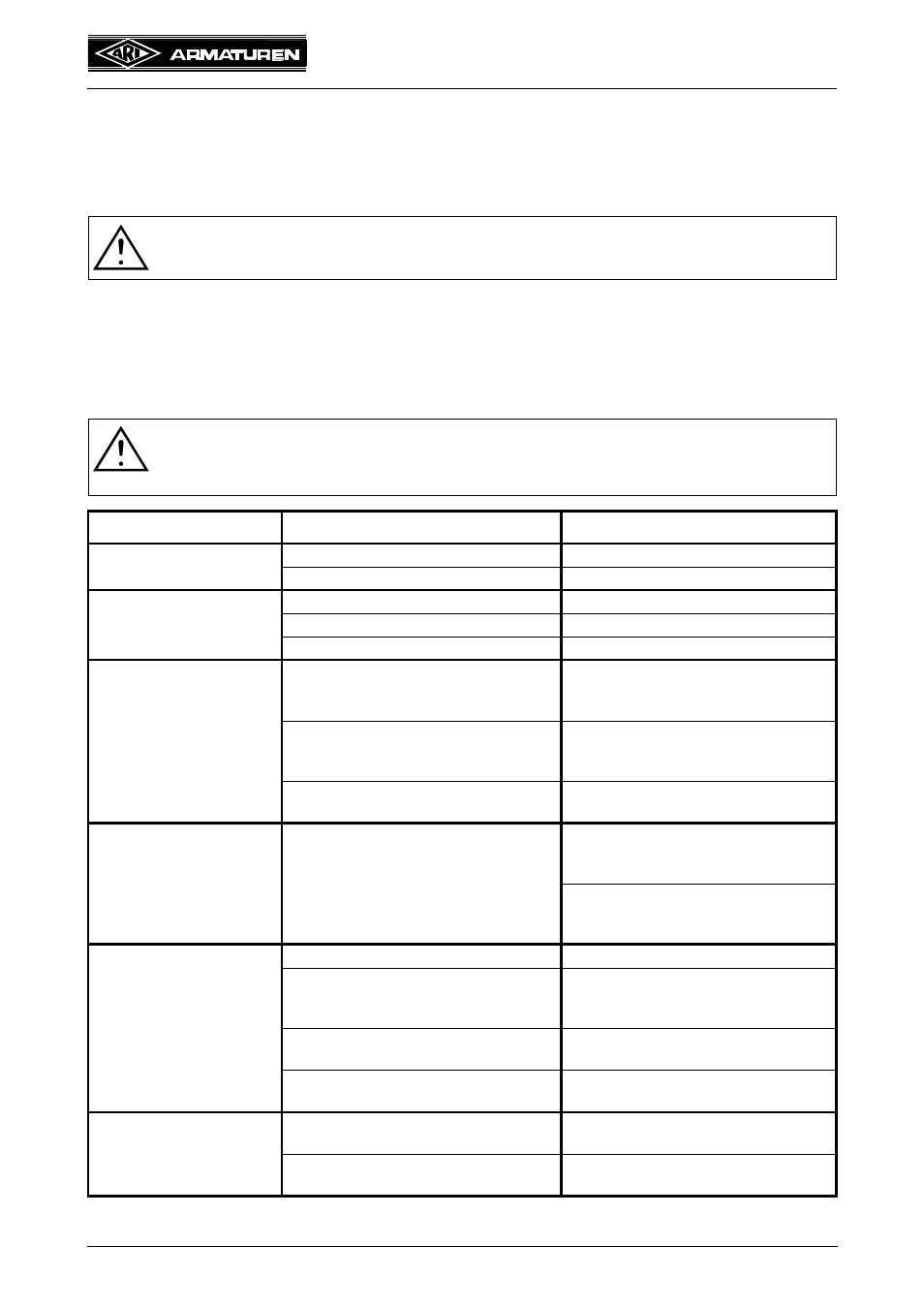
Operating and installation instructions
STOBU
®
PN63-160
Rev. 0040102002 0213
Page 2-15
8.0 Troubleshooting
In the event of malfunction or faulty operating performance check that the installation and
adjustment work has been carried out and completed in accordance with these Operating
Instructions.
If malfunctions cannot be eliminate with the help of the following table
“9.0 Troubleshooting table”, the supplier or manufacturer should be consulted.
9.0 Troubleshooting table
-
ATTENTION !
It is essential that the safety regulations are observed when identifying faults.
ATTENTION !
- read point 10.0 and 11.0 prior to dismantling and repair work!
- read point 6.0 before restarting the plant !
Fault
Possible cause
Corrective measures
No flow
Valve closed.
Open valve.
Flange covers not removed.
Remove flange covers.
Little flow
Valve not sufficiently open.
Open valve.
Dirt sieve clogged.
Clean / replace sieve.
Piping system clogged.
Check piping system.
Valve difficult to move or
cannot be opened
Stem/ Stem unit dry (pos. 4; fig. 14)
Grease stem / Stem unit
(pos. 4; fig. 14)
(Lubricant: see page 13)
Stuffing box too tight (pos. 6; fig. 1 - 8)
Slacken hex. nuts of stuffing box gland
(pos. 15) slightly, but not sufficiently to
cause leakage (fig. 1 - 8)
Wrong direction of rotation
Turn in correct direction (anticlockwise
to open valve).
Valve stem leaking
Stuffing box gland (pos. 15) slack
(fig. 1 - 8).
Tighten stuffing box gland (pos. 15)
until leakage stops.
-Hex. nut (fig. 1 - 8).
If necessary, renew packing in stuffing
box seal (pos. 6). Observe warnings
(fig. 14)!
Leakage across valve
seat.
Valve not properly closed.
Pull hand wheel tight without tools.
Seat (pos. 1.2) / plug (pos. 3 / 4.1)
damaged by foreign particles.
(fig. 1 - 8).
Replaced valve, consult supplier/man-
ufacturer.
Pressure difference too high.
Use a valve with balancing plug
(see point 5.3).
Medium contaminated
(suspended solids).
Clean valve.
Install dirt screen upstream of valve.
Leakage too high when
valve is closed
Pneumatic actuator not completely
vented; spring force not fully effective.
Vent actuator air chamber completely.
Actuator not powerful enough.
Install more powerful actuator.
Check service data.