ROTRONIC HF5 User Manual
ROTRONIC Accessories for electrical
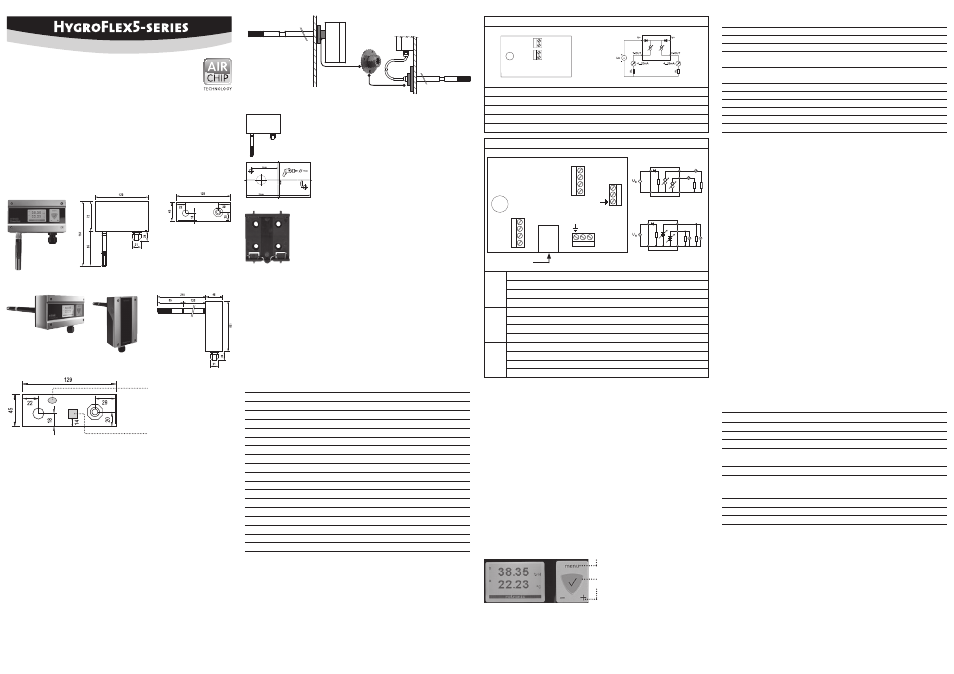
12
.0
84
2.0
00
8
ROTRONIC AG, CH-8303 Bassersdorf
Tel. +41 44 838 11 44, www.rotronic.com
ROTRONIC Messgeräte GmbH, D-76275 Ettlingen
Tel. +49 7243 383 250, www.rotronic.de
ROTRONIC SARL, 56, F - 77183 Croissy Beaubourg
Tél. +33 1 60 95 07 10, www.rotronic.fr
ROTRONIC Italia srl, I- 20157 Milano
Tel. +39 2 39 00 71 90, www.rotronic.it
ROTRONIC Instruments (UK) Ltd, West Sussex RH10 9EE
Phone +44 1293 571000, www.rotronic.co.uk
ROTRONIC Instrument Corp, NY 11788, USA
Phone +1 631 427-3898, www.rotronic-usa.com
ROTRONIC South East Asia Pte Ltd, Singapore 339156
Phone +65 6294 6065, www.rotronic.com.sg
ROTRONIC Shanghai Rep. Office, Shanghai 200233, China
Phone +86 40 08162018, www.rotronic.cn
A
Digital transmitter for humidity & temperature
Duct & Wall Version
Congratulations on your purchase of the new state-of-the-art HygroFlex5-Series transmitter. Please
read these short instructions carefully before installing the device
General description
The HygroFlex5-Series devices are universal transmitters for transmission of humidity and tempera-
ture measurements. Compatible with all interchangeable HC2 probes. These short instructions are
limited to a description of the main functions and installation of the device. The detailed instruction
manual can be found on the internet at:
www.rotronic.com
Dimensions / Connections
Duct version
Wall version
Mechanical installation
General recommendations
Relative humidity is extremely temperature-dependent. In order to measure it exactly, the probe and
sensors must be set exactly on the temperature level of the environment that is to be measured.
The installation site can therefore have a significant influence on the performance of the device.
Follow the guidelines below to ensure optimum performance:
a) Select a representative installation site: Install the probe at a point where the humidity, tem-
perature and pressure conditions are representative for the environment that is to be measured.
b) Make sure there is sufficient air movement around the probe: An air flow of at least 1 metre/
second accelerates and facilitates adjustment of the probe to changing temperatures.
c) Avoid:
1. Probe too close to heating elements, cooling coils, cold or hot walls, direct sunlight, etc.
2. Probe too close to steam, injectors, humidifiers or direct precipitation.
3. Unstable pressure conditions with high air turbulence.
d Insert the probe as far as possible into the environment that is to be measured.
e) Avoid accumulation of condensation at the contact wires of the sensor. Install the probe so
that the tip points down. If that is not possible, install it in horizontal position.
Mounting the duct version
To avoid measurement errors, at least 200 mm of the probe should be inserted into the environ-
ment that is to be measured.
If necessary, use the mounting flange AC5005 to install the probe and fasten the transmitter.
AC5005 Mounting flange
for 15 mm probe
Models with digital HF556 connection
Service interface
Digital connection
Mounting the wall version
Alignment
Mount the transmitter so that the probe points down.
Mounting variant 1
Drill the necessary holes using the drill template drawn on the
packaging. Then insert the plugs delivered with the device and
mount the transmitter with the screws.
Mounting variant 2
If there is a TS35 DIN top-hat rail available, the transmitter can be
clipped on to the top-hat rail directly with the help of the mounting
kit AC5002 (available as optional extra). For this, the DIN holders
(a kit has two holders and eight screws) are screwed directly on to
the predrilled holes in the transmitter.
Electrical installation
Power supply
a) HF52 (2-wire, current loop): 10 to 28 VDC – depending on the connected load. The minimum
supply voltage can be calculated as follows. V min = 10 V + (0.02 x load*) *Load (resistance in
Ohm). The minimum supply voltage for the maximum load of 500 Ohm is: 10 + (0.02 x 500) =
20 VDC. When both outputs are connected, the maximum current consumption is 40 mA.
b) HF53 (3-wire with analogue outputs): 5 to 40 VDC or 5 to 28 VAC.
When both outputs are connected, the maximum current consumption is 100 mA.
c) HF54 (3-wire galvanic separated with analogue outputs): 9 to 36 VDC or 7 to 24 VAC.
When both outputs are connected, the maximum current consmption is 100 mA.
d) HF55 (3-wire with digital output: 5 to 40 VDC or 12 to 28 VAC.
Maximum current consumption: USB 100 mA, Ethernet (TCP/IP) 300 mA.
Supply voltage / Technology
Type
Supply voltage V+
Load
Output
2- or 2x2-wire
HF520
10...28 VDC: 10 V + (0.02 x load)
Max. 500
Ω
4...20 mA
3 / 4-wire
HF531
15...40 VDC / 12... 28 VAC
Max. 500
Ω
0...20 mA
HF532
15...40 VDC / 12...28 VAC
Max. 500
Ω
4...20 mA
HF533
5...40 VDC / 5...28 VAC
Min. 1000
Ω
0...1 V
HF534
10...40 VDC / 8...28 VAC
Min. 1000
Ω
0...5 V
HF535
15...40 VDC / 12...28 VAC
Min. 1000
Ω
0...10 V
Galvanically separated
HF541
9...36 VDC / 7...24 VAC
Max. 500
Ω
0...20 mA
HF542
9...36 VDC / 7...24 VAC
Max. 500
Ω
4...20 mA
HF543
9...36 VDC / 7...24 VAC
Min. 1000
Ω
0...1 VDC
HF544
9...36 VDC / 7...24 VAC
Min. 1000
Ω
0...5 VCD
HF545
9...36 VDC / 7...24 VAC
Min. 1000
Ω
0...10 VCD
Digital output
HF556
15...40 VDC / 12...28 VAC
Digital output
HF557
Power over Ethernet (PoE)
Digital output
Caution:
Wrong supply voltages and excessively high loading of the outputs can
damage the transmitter.
Terminal configuration / Connection diagrams
The type is defined using the table Supply voltage / Technology to then use the following connec-
tion diagrams:
2- or 2x2-wire / HF520
Terminal Description
K2-2-T-OUT
Analogue temperature output +
K2-1-V+
Supply voltage +
K1-2-H-OUT
Analogue humidity output +
K1-1-V+
Supply voltage +
HF53, HF54 (galvanically isolated), HF55
Terminal
Description
K1-1 GND
K6-1 GND
GND / Neutral
K1-2 V+
K6-2 V+
Supply voltage + / Phase
K1-3
K6-3
Earth
K2-4 GND
GND
K2-3 GND
GND
K2-2 OUT2
Analogue temperature output +
*
K2-1 OUT1
Analogue humidity output +
**
K3-4 D–
RS-485 Bi-directional TX – / RX –
K3-3 D+
RS-485 Bi-directional TX + / RX +
K3-2 GND
GND
K3-1 PWR
DC (+) 15…24 VDC (+) See remarks below
* For humidity and calculated value output settings:
OUT2 = calculated value, OUT1 = humidity
** For temperature and calculated value output settings:
OUT1 = calculated value, OUT2 = temperature
Terminal K1-3: Earth is usually connected to GND. If this is not wanted, a land (B18) on the PCB
must be removed.
Terminals K3 (RS-485): Terminals K3-1 and K3-2 can be used to feed the device (multi-point
connection). Several RS-485 devices can be operated with a strong 15 VDC power supply unit. In
this case the supply voltage at K1-1 to K1-3 is not used.
Warning: Make sure that all settings have been made correctly before integrating and connecting
the transmitters in the network.
Programming
The basic settings of the devices are made in the factory according to your order. The transmit-
ters are adjusted in the factory and therefore do not need to be checked and readjusted during
installation. The devices can be started immediately after installation.
Display
In models with LC display the value can be read directly.
Button MENU: open / close menu
Button ENTER: select menu point
Menu navigation
Buttons + / - change value: increase/decrease
Note: Unauthorised use of the menu can be prevented by locking the setting “Display Menu”
(using the HW4 software > Device Manager > Display).
The main menu points
Main menu
Menu points
Options / Information
Remarks
Decive Settings
Units
Metric / English
Contrast
LC display contrast
adjustment
Trend
On / Off
Trend shown on the
display
Device Information
Version
Firmware version
Serial No.
Serial number
Address
Address RS-485
Type
Device type
Name
Device name
User-defined
Sources of error
Measured values can be influenced by the following factors:
Temperature errors :
Adaptation time too short, cold outside wall, heating elements, sunlight, etc.
Humidity errors:
Steam, water spray, dripping water or condensation at the sensor, etc. Repeatability and long term
stability are, however, not influenced by these factors even if the probe is exposed to high humidity
or saturation with steam (condensation) over a longer period of time.
Soiling:
By dust in the air. The choice of probe filter depends on the amount of soiling at the measuring
point. The filter must be cleaned or replaced periodically.
Scaling / Adjustment / Firmware update
The following settings can be made with the help of the HW4 software and either the service cable
AC3006 or AC3009:
• new scaling of the outputs
• adjustment
• firmware update
You can find a detailed description in the manual that you can download from our web site at
www.rotronic-humidity.com
Periodic calibration of the probe / transmitter
Both the Pt 100 RTD temperature sensor and the corresponding electronics are very stable and do
not normally need to be changed or calibrated after factory calibration. The long term stability of the
ROTRONIC Hygromer humidity probes is typically better than 1 %rh per year. For maximum accuracy
we recommend calibration of the probe about every six to 12 months. More frequent calibration
can be necessary in applications where the sensor is exposed to pollutants. The calibration can
be performed by the user himself on site or in the laboratory / workshop. For routine calibrations
the probe should be checked at one or two points.
The electronics of the transmitter do not normally require calibration in the field. They can be
checked easily with the help of the probe simulator in the HW4 software package. The electronics
cannot be repaired in the field and should be returned to the manufacturer in the case of problems.
For details on calibration, please see the full version of the instruction manual, which you can
download from the internet.
Technical data (measurement)
Humidity:
0...100 %rh
Temperature:
–100...200 °C
Accuracy:
Probe-dependent: ± 0.8 %rh, ± 0.1 K @ 23°C
Protection:
IP65 except for models with USB and Ethernet interface
Outputs:
Current or voltage signals, digital output depending on order code,
UART service interface
Technical data (
Electronics operating range)
Temperature:
HF53/54/55/56: –40...60 °C
HF520: –25...60 °C
Models with display –10...60 °C
Humidity:
0...100 %rh, non-condensing
Technical data probe
Depending on type
SHORT INSTRuCTION MANuAL
Current output
Voltage output
=
~
K1: V+
K1: GND
K2: GND
K2: OUT1
K2: OUT2
K1: V+
K1: GND
K2: GND
K2: OUT1
K2: OUT2
T – OUT
V +
H – OUT
V +
K 2
K 1
2
1
2
1
Ethernet
PoE
Wireless
USB
RS-485
K 3
D –
D +
GND
PWR
4
3
2
1
1
2
3
K 1
GND
V +
K 2
GND
GND
OUT2
OUT1
4
3
2
1
OUT 1 = %RH
OUT 2 = °C/F
3 2 1
GN
D
V
+
K 6
digital in/output
Equipment depending on model
Digit
al
Analog
Pow
er
Sup
ply