Dwyer instruments, inc – Dwyer 2000 User Manual
Page 2
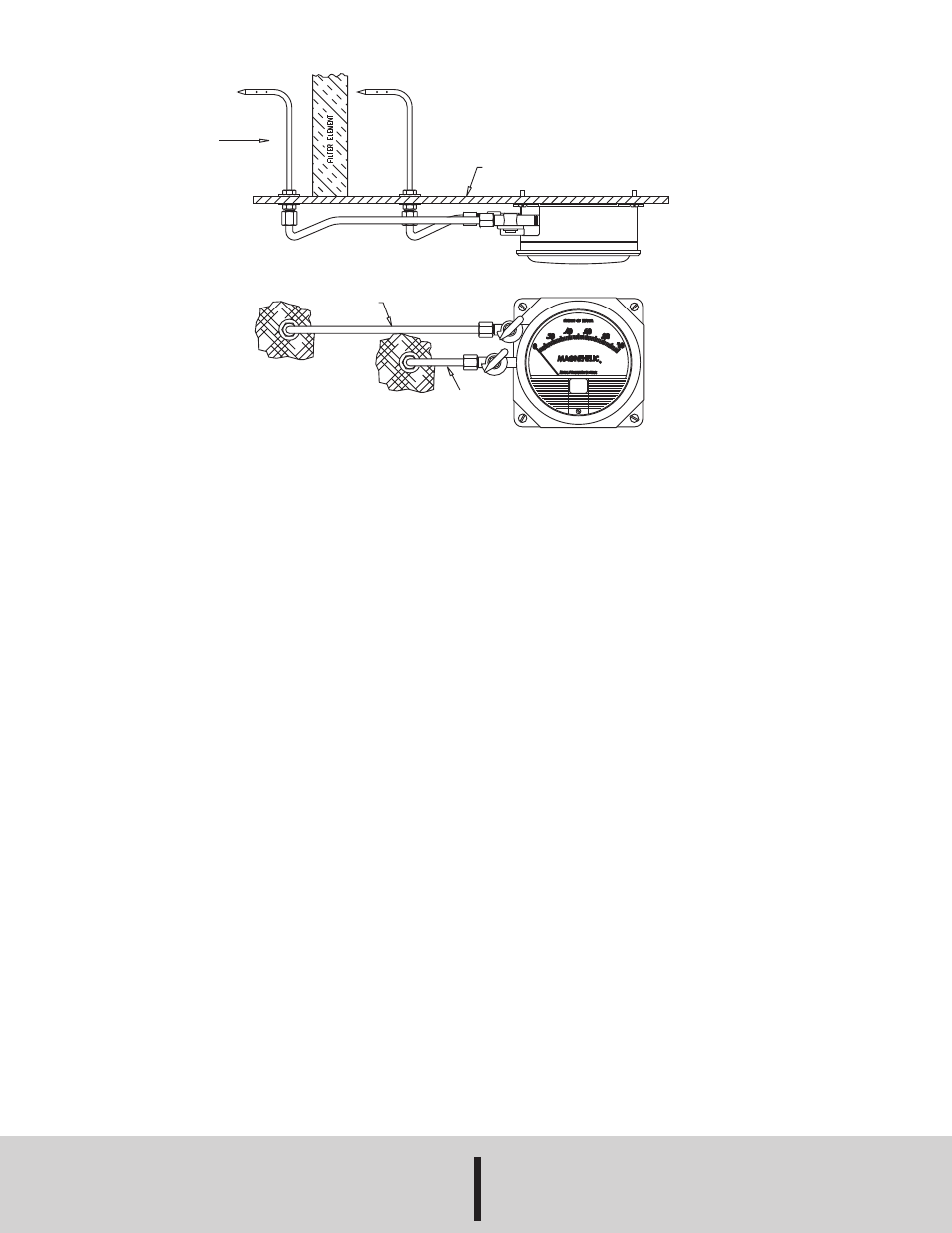
INSTALLATION PROCEDURE
1. Screw vent valves into side connections of gage. Be sure back connections of
gage are sealed with plugs provided with the gage. Attach gage to mounting
plate with three No. 6-32 screws provided.
2. Select a convenient location on filter wall and punch or drill four 1/8˝ dia. max.
holes for mounting plate as shown in drawing above. Attach mounting plate
to filter wall with four self-tapping screws provided. If gage is to be flush
mounted in control panel, refer to Bulletin No. A-27.
3. Drill two 7/16˝ holes in the duct, one on each side of the filter and at least 12”
distant*. Secure the static pressure tips as in the drawing above, with the tips
directed into the air flow.
4. Connect 1/4˝ metal tubing from the static pressure tips to the gage. The tip on
the downstream side of the filter is connected to the vent valve in the low
pressure connection of the gage. The tip on the upstream side is connected
to the vent valve in the high pressure connection.
5. Turn both vent valves to “VENT” position and adjust the gage pointer to zero
by means of the external adjustment screw in the face of the gage. After
zeroing, turn vent valves to “LINE” position.
*NOTE On location of static pressure tips: The location of static pressure tips
is of primary importance in securing reliable readings. For maximum accuracy, it is
essential that the influence of the velocity of the air be eliminated to permit sensing
the true static pressure. Note that some installations do not provide a straight duct
approach to the filter bank which may cause air to swirl and eddy.
Tips should be located as recommended by the specifying engineer or by the filter
manufacturer. In the absence of such recommendations, locate the tips at least 12˝
upstream and downstream from the filters in a zone of minimum turbulence.
INSTALLATION CHECK AND TROUBLE SHOOTING
Before putting your air filter gage into service or in the event of initial pressure drop
readings that do not agree with the filter manufacturer’s specified pressure drop,
make the following checks:
1. Check zero adjustment of the gage as described above.
2. Check all tubing connections for tightness from the gage to the static tip or
fitting connection.
3. Check plastic cover of gage to be sure it is securely in place and air tight.
4. Check static pressure tips or fittings to be sure they are not plugged.
5. Check installation of static tips or fittings*. Be sure static pressure tips point
directly into the air stream. A velocity pressure error can be created if the air
blows directly into the opening.
OPERATION
With vent valves in “LINE” position the gage will indicate pressure drop across the
filter. If the reading varies substantially from the filter manufacturer’s rating for a
clean filter, check the system for proper setting of controls, air balancing of system,
leakage in system and whether or not the correct filter has been installed.
When pressure drop across the filter reaches the minimum recommended by the
manufacturer, the filter should be serviced or replaced.
FILTER WALL
AIR FLOW
HIGH PRESSURE
LINE
LOW
PRESSURE LINE
12˝ BETWEEN
STATIC TIPS AND FILTER
Options Not Shown:
- Automatic signal flag integral with plastic gage cover
- Not shown Scale plate overlays in green and red
©Copyright 2013 Dwyer Instruments, Inc.
Printed in U.S.A. 5/13
FR# 12-440238-00 Rev. 4
DWYER INSTRUMENTS, INC.
Phone: 219/879-8000
www.dwyer-inst.com
P.O. BOX 373 • MICHIGAN CITY, INDIANA 46361, U.S.A. Fax: 219/872-9057
e-mail: [email protected]