KROHNE OPTIMASS Sensors Corrosion guidelines EN User Manual
Page 15
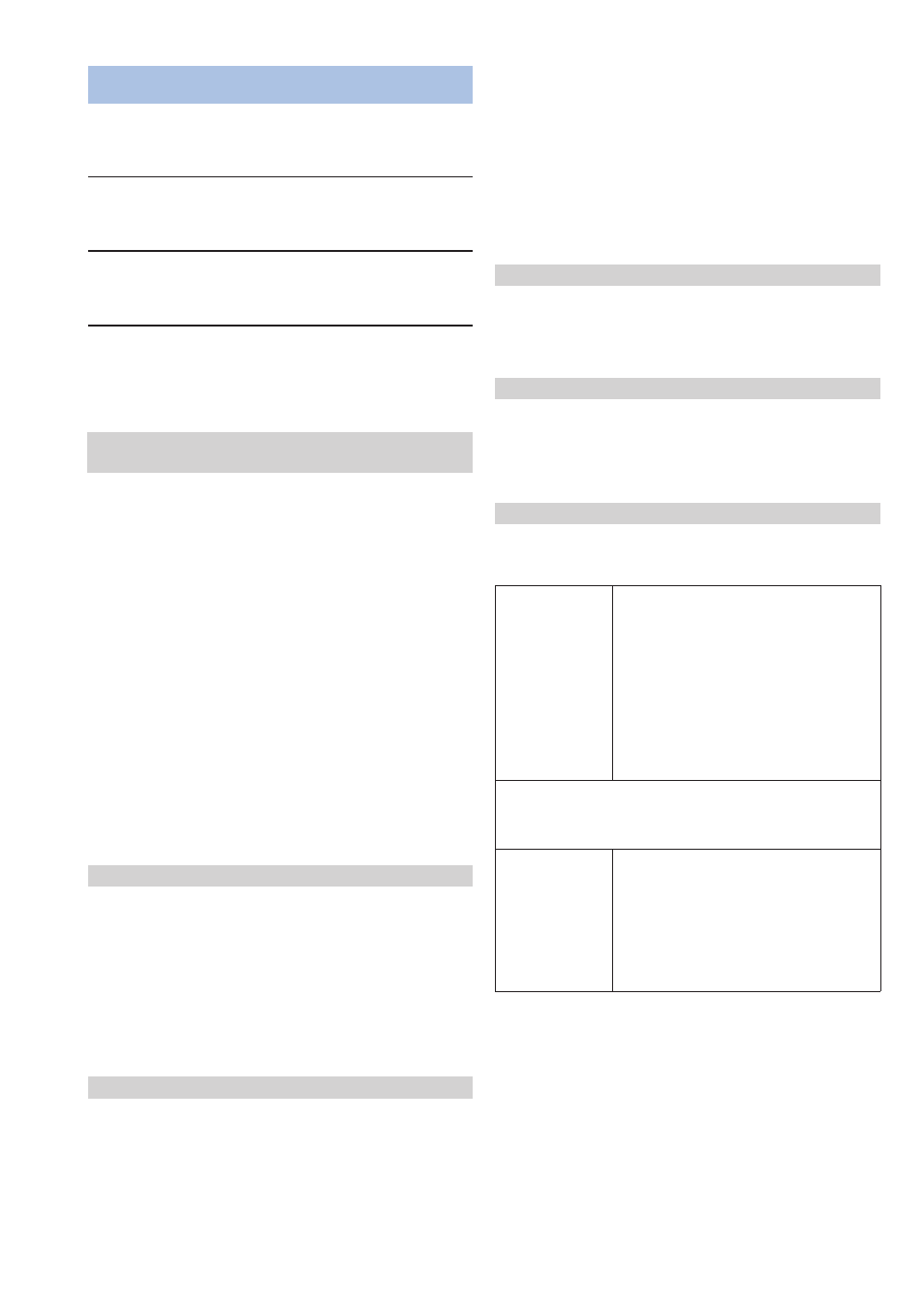
15
Corrosion Guide Rev 1.05 Jan 2006
Meter
size
Material
Outside dia.
Wall
Thickness
Internal
dia.
40
T
38.10 ± 0.13
0.91 ± 0.09
36.28
H
38.10 ± 0.1
0.71 ± 0.07
36.68
S
38.10 ± 0.13
0.71 ± 0.07
36.68
50
T
50.80 ± 0.15
1.24 ± 0.01
48.32
H
50.80 ± 0.15
1.00 ± 0.01
48.80
S
48.26 ± 0.13
1.00 ± 0.01
46.26
80
T
73.00 ± 0.254
2.10 ± 0.02
68.80
H
73.03 ± 0.254
1.04 ± 0.01
70.95
S
73.00 ± 0.13
1.40 ± 0.01
70.20
All dimensions in mm
It should be noted that the exception to this is when
stainless steel or Hastelloy are required for fluid com-
patibility (corrosion resistance).
2.5 Conditioning of the fluid flow profile
(as it enters the meter)
Firstly remember that a Coriolis mass flow meter direct-
ly measures mass flow and density of the fluid. It does
not measure velocity, so from a measuring principle
standpoint there is no need for flow profile conditioning.
However with an abrasive fluid, there is the require-
ment to condition the flow so that the abrasive particles
enter the meter parallel to the tube wall. This minimises
the probability that any given abrasive particle will
strike the tube wall and remove (erode) the tube mate-
rial.
If the flow is “tumbling” or “swirling” as it enters the
meter, there is a risk that erosion will occur at the spe-
cific point where the particles preferentially impact onto
the tube wall, so causing premature failure. These
problems are always associated with using a pipework
bend or elbow very close to the meter inlet.
Therefore we recommend a straight length of inlet
process pipe equal to at least 10, or preferably 20 x
pipe internal diameters.
2.6 Installation of the flow meter
In order to keep the heavy abrasive particles evenly
dispersed in the carrier fluid as a homogenous mixture
that is required for correct meter operation, we would
recommend a vertical meter installation. Otherwise
there is the tendency, especially at lower flow veloci-
ties, for the fluid to separate out and become stratified.
Further, a flow direction vertically upwards is normally
preferred to ensure that meter is always full of liquid,
and does not “siphon” empty.
2.7 Inclusion of air or gas in the fluid
High density fluids such as mineral slurries typically
require a high drive energy due to their tendency
towards being inhomogeneously mixed.
Entrained air or gas will cause a further increase in the
required energy to drive (vibrate) the tube system. If
the inclusion is too great then the meter will not operate
correctly. This problem is particularly pronounced on
larger sized meters (T 50 & T 80), which typically are
used for abrasive fluid applications in order to reduce
the fluid velocity to acceptable levels.
So we would recommend that all efforts be made to
prevent the inclusion of air or gas in the fluid as part of
the process design, since from our experience once
entrained in the fluid it is virtually impossible to remove
prior to the metering point
2.8 Consider installing the meter in a by-pass
If the application is for density measurement only, then
often a more cost-effective solution is to install a small-
er sized meter (although size 25 is smallest recom-
mended) in a by-pass line off the main pipeline.
2.9 Conclusions
We are confident that if the seven steps above are fol-
lowed correctly, then the probability of application relat-
ed problems are greatly reduced and the operating life-
time of the meter greatly increased.
3. Environmental Protection
The materials exposed to the environment as standard
are:
MFM x050 Ex
MFM x051 Ex
MFM xo50 Ex
MFM x051 Ex
MFC 050 Ex
MFC 051 Ex
•
304L Stainless Steel for the sen-
sor body with optional
316LStainless Steel for offshore
applications.
•
Electronics housing is die cast
aluminium, powder coated.
•
The aluminium has a low copper
content (see specification table).
All above housings will be powder coated in silver and
All covers (screw-on type) will be painted in blue RAL
5005
MFC 300C
MFC 300F
MFC 300W
•
304L Stainless Steel for the sen-
sor body with optional
316LStainless Steel for offshore
applications.
•
Electronics housing in Stainless
Steel 316L.