KROHNE OPTIMASS Sensors Corrosion guidelines EN User Manual
Page 14
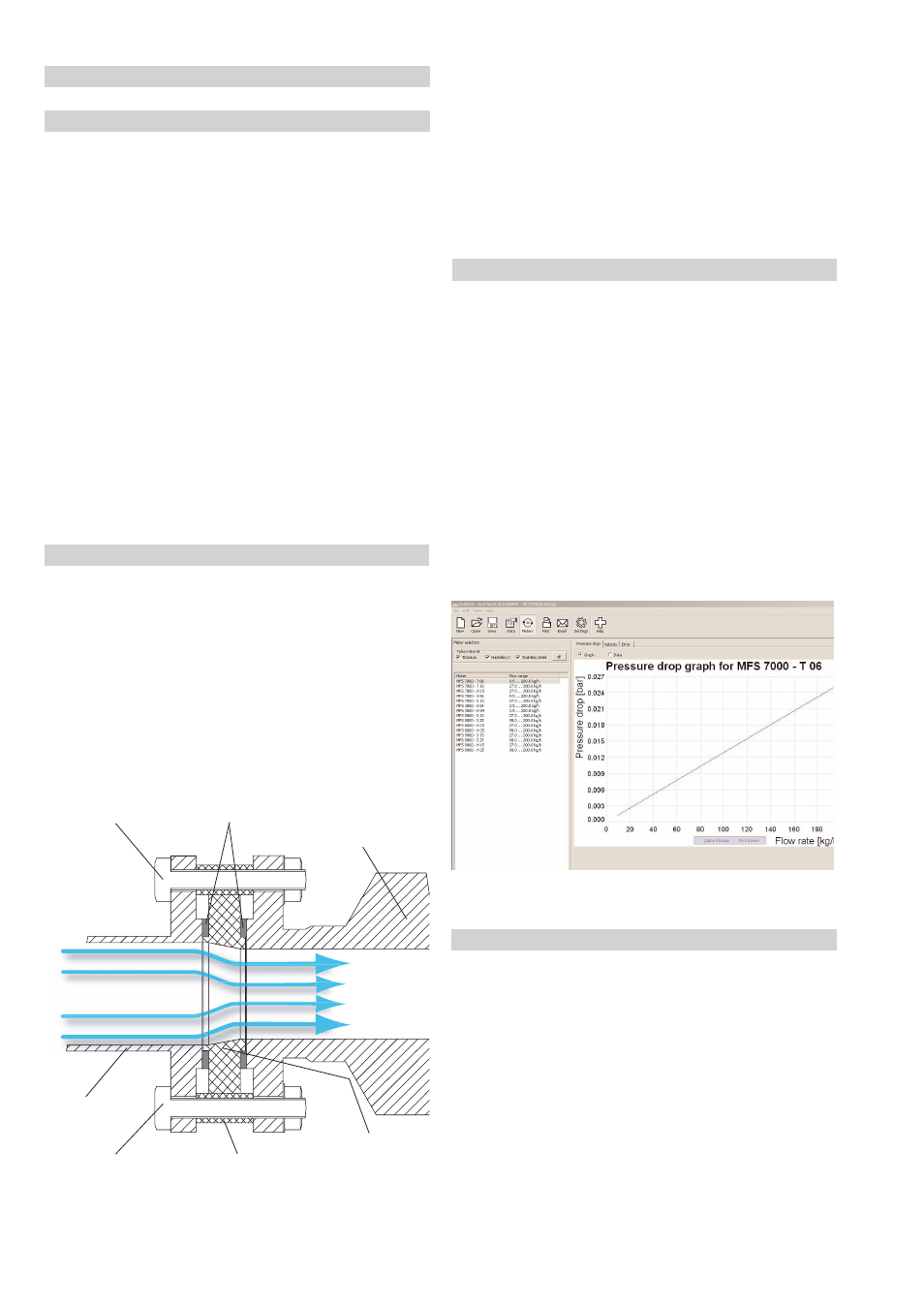
14
Corrosion Guide Rev 1.05 Jan 2006
Flow
Flange Bolt
Centralising
Sleeves
Gaskets
Transition
Piece
Pipe Work
Flow Meter
Flange Bolt
Typical Transition Piece Application
2. Abrasion Guidelines & information.
2.1 Introduction
For almost 10 years, the Krohne Corimass G Class
and Optimass 7000 series Coriolis mass flow meters
have been successfully used on abrasive fluids such as
slurries (mineral and metal mining) as wella as sand &
water mixtures.
In these applications, a single straight measuring tube
will always offer clear advantages over other designs
with tube geometries that suffer erosion and premature
failure of flow dividers and bends in the abrasive fluid
stream. Notwithstanding this, even a meter with a sin-
gle straight tube will suffer some erosion unless simple
precautions are taken.
Other specific problems with abrasive fluids are typified
by their tendency to separate out with the heavier parti-
cles falling to the bottom of the pipeline and the carrier
fluid flowing above in a stratified flow.
The purpose of this application guidance is to highlight
potential problems so that they can be mitigated
against during the planning and installation of the
meter.
2.2 Protecting Flanges with Transition Pieces
Since the meter measuring tube will typically have a
different internal diameter than the process pipework, a
“step change” will occur where the flanges are connect-
ed. This edge presents a very obvious erosion point
and after a period, the weld between the flange raised
face and measuring tube could fail causing a leak path.
Transition pieces are stainless steel (although Hastelloy
can be used) discs that are sandwiched between the
two flanges, secured by through bolts and centred by
rubber sleeves around the bolts.
The taper on the internal diameter of the disc is manu-
factured to correct the difference between the meter
and process pipe, thus providing a gradual transition
for the abrasive fluid into the meter.
They must be considered as “sacrificial wear parts”,
and should be removed periodically for inspection of
the internal taper dimension and replacement if neces-
sary.
Prices for these parts are available from Krohne.
2.3 Managing fluid velocity
There are two considerations here based on the fluid
flow rate and density:
Maximum velocity
To prevent excessive erosion this should be never be
more that 4 m/sec (12 ft/sec).
Minimum velocity
So the particles and carrier are homogeneous mixed
this should be at least 1 m/s (3 ft/sec).
The Optimass sizing software will assist you in calculat-
ing these limits. For abrasive slurries always size
according to these velocity limits, and not lowest meas-
uring error which tends towards a smaller meter size
and hence a higher velocity.
2.4 Titanium as the standard material
Titanium should always be used as the standard mate-
rial for measuring tubes. This is because size-for-size,
a titanium measuring tube has a greater wall thickness
than either stainless steel or Hastelloy. Simply put, this
tube has more material to erode before failure, so
extending the working lifetime of the meter.
Optimass Sizing Software Screen Shot