Safety-related characteristics, Safety-related characteristics 7.1 assumptions – KROHNE H250 M40 Safety V1 EN User Manual
Page 11
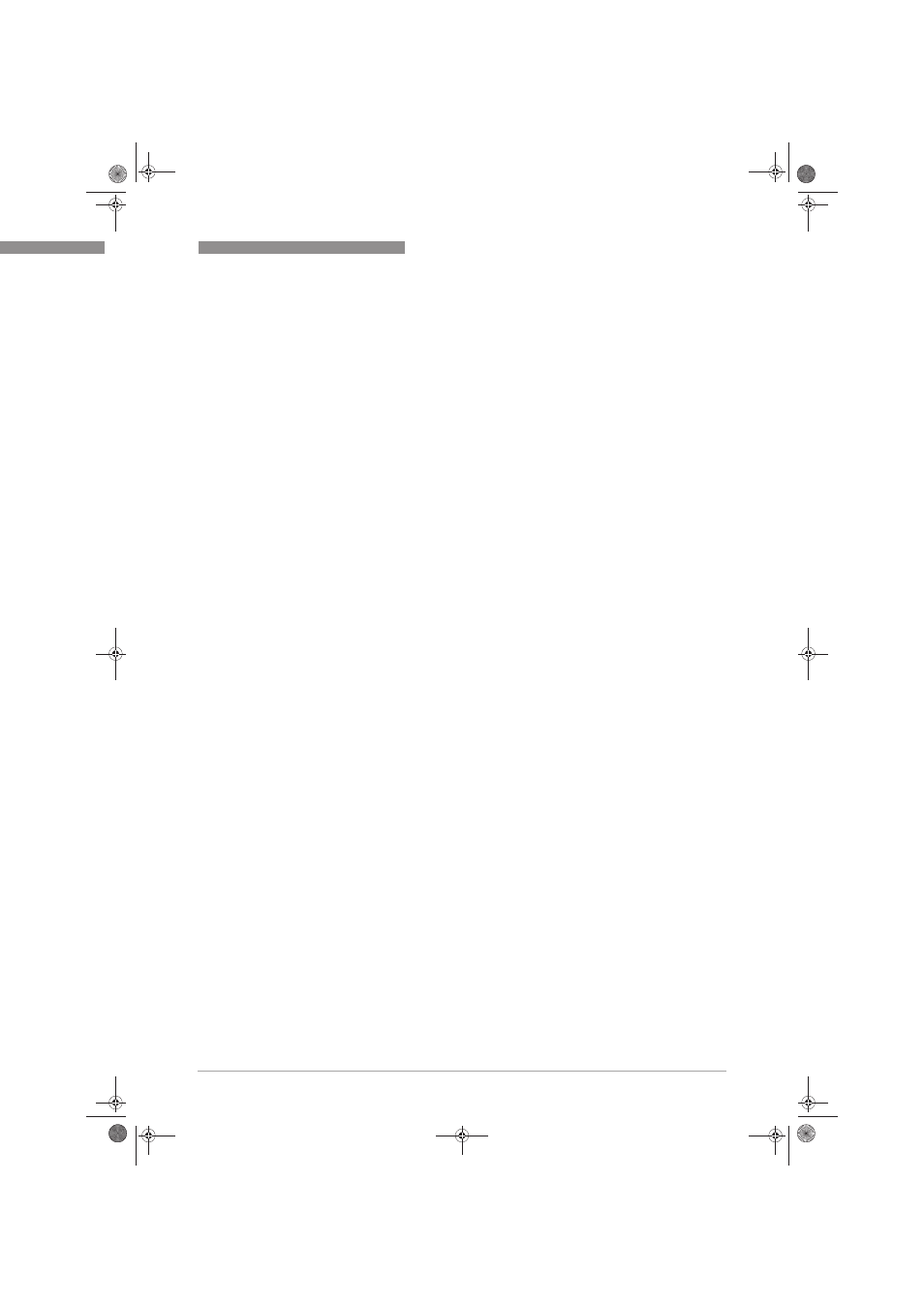
SAFETY-RELATED CHARACTERISTICS
7
11
H250 M40
www.krohne.com
02/2012 - 4000904201 MA H250 M40 SIL R01 en
Safety-related characteristics
7.1 Assumptions
The following assumptions have been made during the Failure Modes, Effects and Diagnostic
Analysis of the variable-area flowmeter H250 M40.
• Failure rates are constant, wear out mechanisms are not included.
• Propagation of failures is not relevant.
• Failures resulting from incorrect use of the flowmeters H250 M40, in particular humidity
entering through incompletely closed housings or inadequate cable feeding through the
inlets, are not considered.
• Failures during parameterization are not considered
• Sufficient tests are performed prior to shipment to verify the absence of vendor and/or
manufacturing defects that prevent proper operation of specified functionality to product
specifications or cause operation different from the design analyzed.
• The mean time to restoration (MTTR) after safe failure is 24 hours.
• All modules are operated in the low demand mode of operation.
• External power failure rates are not included.
• The HART® protocol at H250 M40 is only used for setup, calibration and diagnostics purpose,
not during safety operation mode.
• Practical fault insertion test can demonstrate the correctness of the failure effects assumed
during FMEDAs.
• The stress levels are average for an industrial outdoor environment and can be compared to
exida Profile 2 or Profile 4 with temperature limits within the manufacture’s rating. Other
environmental characteristics are assumed to be within the manufacturer’s ratings.
• The switching contact outputs are connected to a NAMUR amplifier. The failure rates of the
amplifier are not included in the listed failure rates.
• Only the current output 4...20 mA or the limit switch outputs are used for safety applications.
• Lead breakage and short circuit detection is activated.
• The application program in the safety logic solver is configured to detect under-range and
over-range failures and does not automatically trip on these failures; therefore these failures
have been classified as dangerous detected failures. The failure rates of the safety logic
solver are not included in the listed failures rates.
• No effect failures are included in the “safe undetected” failure category. Note that these
failures on its own will not affect system reliability or safety, and should not be included in
spurious trip calculations.
The variable area flowmeter H250/M40/K*
H250/M40/K*
H250/M40/K*
H250/M40/K* with inductive limit switches are classified as Type A
Type A
Type A
Type A
subsystems
subsystems
subsystems
subsystems (non-complex subsystem according 7.4.3.1.2. of IEC 61508-2) with hardware fault
tolerance HFT=0. For Type A subsystems the SFF has to be > 60% for SIL2 subsystems with a
hardware fault tolerance of 0 (table 2 of IEC 61508-2).
The variable area flowmeter H250/M40/ESK
H250/M40/ESK
H250/M40/ESK
H250/M40/ESK with 4…20mA output is classified as Type B
Type B
Type B
Type B
subsystem
subsystem
subsystem
subsystem (complex subsystem according 7.4.3.1.3. of IEC 61508-2) with hardware fault
tolerance HFT=0. For Type B subsystems the SFF has to be > 60% for SIL1 subsystems with a
hardware fault tolerance of 0 (table 3 of IEC 61508-2).
MA_H250_M40_SIL2_R01_en_904201_PRT.book Page 11 Thursday, March 1, 2012 10:08 AM