Figure 2. rear connector pin assignments, Figure 3. typical alarm circuit diagrams – KEPCO HSF 100W Series User Manual
Page 3
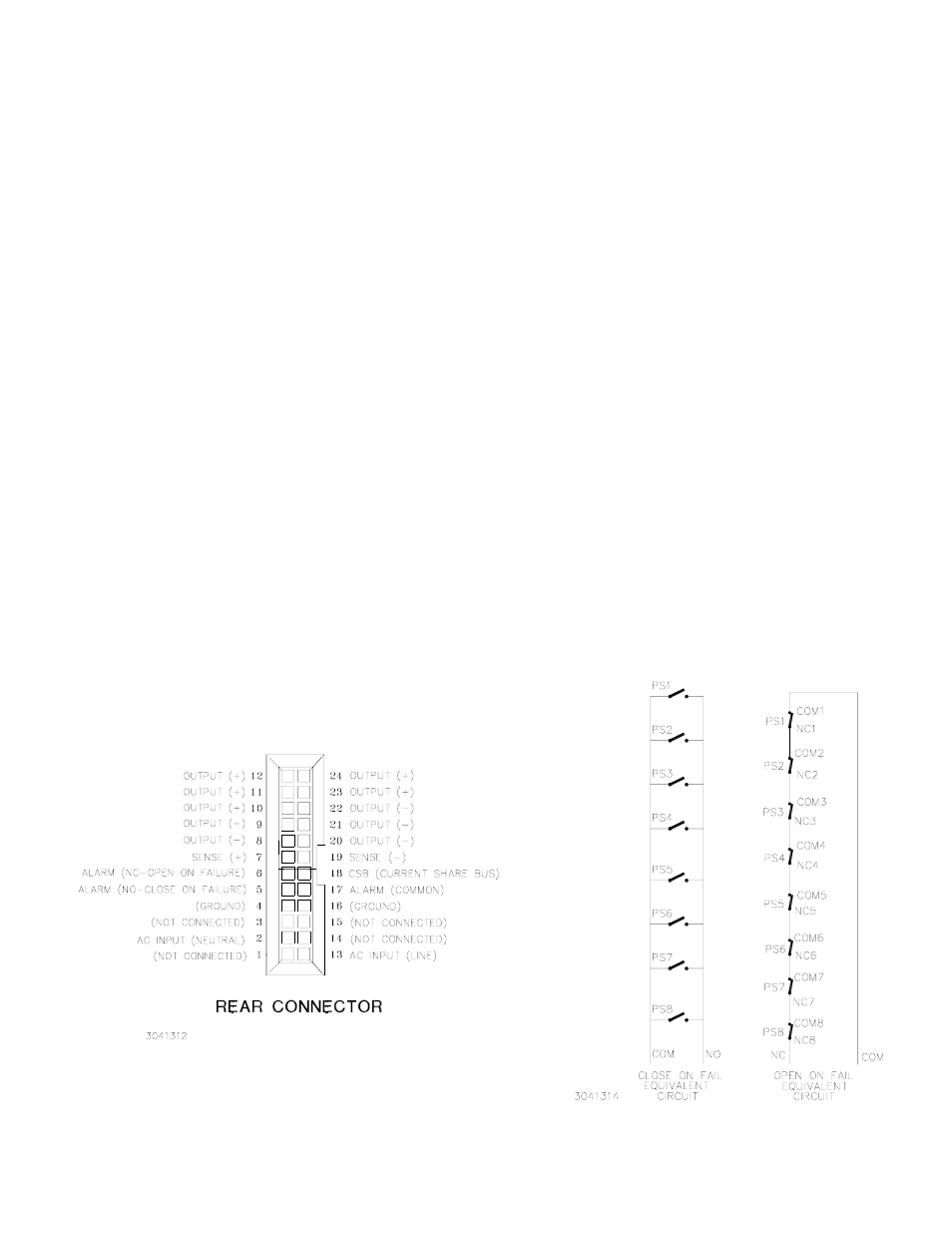
082306
228-1300 REV 5
3
KEPCO, INC. " 131-38 SANFORD AVENUE " FLUSHING, NY. 11352 U.S.A. " TEL (718) 461-7000 " FAX (718) 767-1102
http://www.kepcopower.com " email: [email protected]
SAFETY: Units designed to meet UL60950 3rd Edition, CSA 22.2 No. 60950 and EN 60950 and are CE marked per the Low
Voltage Directive (LVD), 73/23/EEC and 93/68/EEC. [The standards do not apply with DC input operation.]
I/O CONNECTOR: The 24-pin I/O connector (Figure 2) is designed to mate with the corresponding connector in the Series
RA 19-(X)B Rack Adapter.
#
(+) SENSE, (–) SENSE: These lines are provided to compensate for voltage drops in the load connecting wires. The
Sense lines must be connected to their respective (+) and (–) output terminals, either at the load or at the rack adapter
(see Rack Adapter Manual). The connection ensures the most accurate error tracking. Error compensation in the connect-
ing wires is up to 0.25 Volts per lead for all models.
NOTE:
The Sense lines must be connected for the HSF Power supply to work properly!
#
OUTPUT (+), OUTPUT (–): HSF power supply d-c output.
#
CURRENT SHARE BUS (CSB): Connecting the CSB lines of HSF power supplies operating in a parallel configuration
causes output current to be shared equally. (See Rack Adapter Manual for additional information on parallel configura-
tions.). For current sharing to work properly the outputs of all paralleled units must be within 250 mV (max) of each other
and each unit must be operating at between 10% to 100% of rated output. If current to the load goes below 10% for each
unit in current share mode, all MASTER ON lights may go on (see load effect specifications); this indicates that forced cur-
rent share is no longer working, units are simply in current share mode. (If forced current sharing at less than 10% nominal
current per supply is needed, contact Kepco application engineering.) Remote sensing is recommended. For master/slave
operation to work properly each unit should be adjusted to 40 mV (optimum) less than the next paralleled unit (unit 1 is
adjusted to VOUT, unit 2 to VOUT – 40mV, and unit 3 to VOUT – 80mV, etc. If the master fails, the unit 2 will become the
new master). The 40 mV difference can be reduced to a minimum of 25 mV as needed to parallel many units and still keep
all units within 250 mV of each other. Adjust the outputs using Vadj trimmer on front panel.
• Optimum difference among output voltages of paralleled units: 40mV
• Maximum difference among output voltages of paralleled units: 250 mV
• Minimum difference among output voltages of paralleled units: 25 mV
#
ALARM: The Alarm NC (normally closed) - Open on Failure and Alarm NO (normally open) - Close on Failure lines are
relay contacts referenced to Alarm Common. If the unit fails, the path between Alarm NC - Open on Failure and Alarm
Common opens, the path between Alarm NO - Close on Fail and Alarm Common is a short circuit. Figure 3 illustrates typ-
ical Close on Fail and Open on Fail circuits to give a failure indication if any one of a number of power supplies fail.
#
INPUT POWER: Line (either a-c or d-c source power), Neutral and Ground (chassis)
FIGURE 3. TYPICAL ALARM CIRCUIT DIAGRAMS
FIGURE 2. REAR CONNECTOR PIN ASSIGNMENTS