Detcon 971-041170-00K User Manual
Page 5
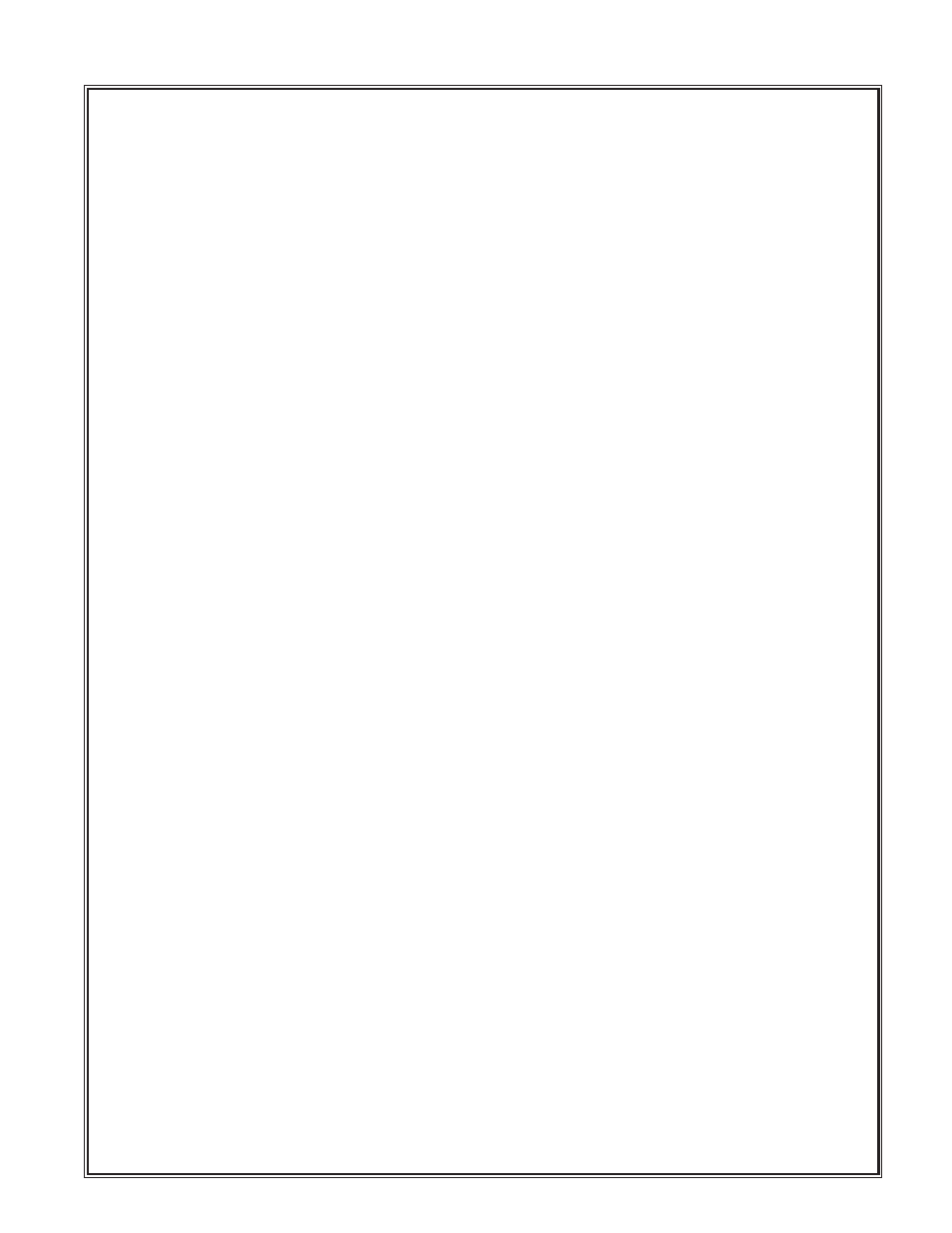
Assure that all field tubing connections are secure by obstructing the end of the sample line and observing that the
flow meter decreases to “0” flow.
1.3 FLOW FAULT DETECTION
Flow fault detection consists of a flow fault circuit assembly located inside the enclosure and a door mounted fault indi-
cator lamp. If the air flow falls below a predetermined set point the following will occur: the flow fault alarm relays will
energize; an LED indicator mounted on the flow fault PCB will illuminate; the door mounted flow fault lamp will illu-
minate; the 4-20mA signal will be opened via relay #1 on the flow fault circuit board (this will allow for flow fault pro-
gramming at the remote recording device or computer).
Because the pressure inside the sample and vent flow tubing differs according to the tubing length , the flow fault
circuit will require calibration after installation.
To calibrate the flow fault circuit, first determine at what point it is desired that the flow fault circuit is activated.
Typically, air flow should range between 500 and 1000 ml/min. (milliliters per minute) as seen on the flow meter located
on the left of the enclosure. It is recommended that the flow fault circuit be set to activate at a flow of approximately
200 ml/m.
To adjust the flow fault first set the air flow at the point where you want the fault condition to activate. Next turn
the flow fault adjust potentiometer (PT1 as seen in the illustration on the previous page) clockwise until the flow fault
LED illuminates and its relays fire. Make adjustments as necessary by increasing and decreasing airflow until the flow
fault function occurs at the desired set point. Once the flow fault circuit has been set, return the air flow to between 500
and 1000 ml/m.
NOTE: Because sample and vent tubing can become congested over a period of time, the flow fault function should be
checked periodically and adjusted as necessary.
1.4 CALIBRATION
Model 971-041170-00K sensor assemblies are calibrated prior to shipment and should therefore require minimal adjust-
ment at time of commissioning. However, it is recommended that a complete calibration be performed on a periodic
basis to assure optimum system performance. Refer to the sensor instruction manual for gas type, range and sensor spe-
cific calibration instructions.
Note that the sensor instruction manual requires the removal of rain/splash guards for the application of gas. This
requirement will be superceded by the instructions below. The calibration adapter attached to the sensor head should
not be removed during calibration.
Required material:
1. Span gas cylinder containing gas as per instructions in the sensor instruction manual.
2. 1/4" Tee tubing fitting as shown in the illustration on the following page.
To Calibrate: (refer to illustration on the following page)
1. As shown in the illustration on the following page, turn the “CAL IN” valve counter-clockwise so that the handle is in the
vertical position. Next turn the “SAMPLE VALVE” clockwise so that the handle is in the horizontal position. The sample is
now being drawn from the CAL port.
2. Using the 1/4" Tee assembly, connect the span gas cylinder to the calibration port. Note that the cylinder flow rate
should be 500 ml/m while the sample draw flow rate should be adjusted to 400 ml/m. This will assure that the sample is
not diluted.
NOTE: The 1/4'' Tee and vent tube is not necessary when using a demand flow regulator. Set flow via rotameter to 500
cc/min when using the demand flow regulator.
3. Follow the calibration instructions given in the sensor instruction manual.
4. Close cylinder valve to allow clearing/zero stability. Note that zero and span functions may interact slightly with one
another on a 400 series sensor. If using a 400 series sensor, zero and span tests may be repeated 2 or 3 times as necessary.
Detcon Model 971-041170-00K Gas Detection System PG.5