Important, Caution, Warning – SANDPIPER PB2-A User Manual
Page 4: Reassembly, Troubleshooting
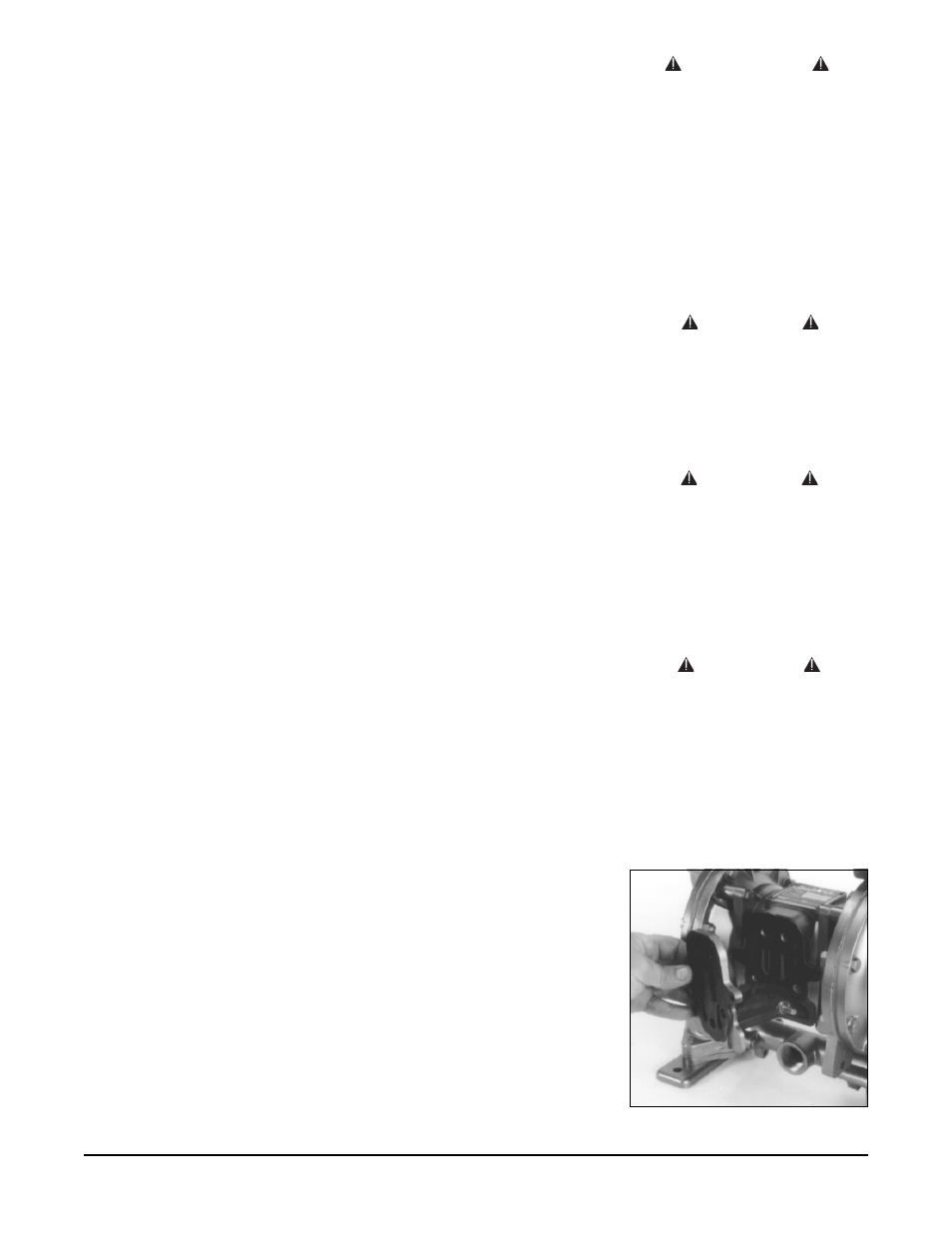
Model PB1½-A & PB2-A
Page 4
520-130-000
2/97
IMPORTANT
Before pump operation, all external
gasketed fasteners must be inspected
for looseness caused by gasket creep
after leaving the factory. Retorque loose
fasteners to insure against leakage.
Follow recommended torques where
called out. (A card is attached to each
new pump stating this fact.)
This pump is pressurized internally with
air pressure during operation. Always
make certain that all bolting is in good
condition and that all of the correct
bolting is reinstalled during assembly.
CAUTION
In the event of diaphragm rupture,
pumped material may enter the air end
of the pump, and be discharged into the
atmosphere. If pumping a product which
is hazardous or toxic, the air exhaust
must be piped to an appropriate area for
safe disposition.
CAUTION
Before maintenance or repair, shut off
the compressed air line, bleed the pres-
sure, and disconnect the air line from
the pump. The discharge line may be
pressurized and must be bled of its
pressure. When used for toxic or ag-
gressive fluids, the pump should
always be flushed clean prior to
disassembly.
WARNING
Take action to prevent static sparking.
Fire or explosion can result, especially
when handling flammable liquids. The
pump, piping, valves, containers or other
miscellaneous equipment must be
grounded.
Fig. 10
Pilot valve being removed
REASSEMBLY
Procedures for reassembling the diaphragms are the reverse of the above. The
diaphragms must be installed with their natural bulge to the outside, toward the outer
diaphragm plate. Install the inner plate with the flat face against the diaphragm.
After all components are in position in a vise and hand tight, tighten with a wrench
to approximately 35 ft. lbs. (420 in./lbs.) (47.45 Newton meters) torque (See Fig. 4).
After both diaphragm assemblies have been assembled, thread one assembly into
the shaft (hold the shaft near the middle in a vise with soft jaws, to protect the finish).
Install this sub assembly into the pump and secure by placing the outer chamber on
the end with the diaphragm. This holds the assembly in place while the opposite side
is installed. Torque the last diaphragm assembly to 25 ft. lbs. (33.90 Newton meters)
(see Fig. 5). This final torquing will lock the diaphragm assemblies together. Place the
remaining outer chamber on the open end and loosely tighten the V-Band clamps.
Replace the manifold assemblies to square the flanges before final tightening of the
V-Band clamps. Make sure necessary gaskets and o-rings are in place (see Figs.
6, 7 & 8).
TROUBLESHOOTING
1. Pump will not cycle
A. Check to make sure the unit has enough pressure to operate and that the air inlet
valve is open.
B. Check the discharge line to insure that the discharge line is neither closed nor
blocked.
C. If the spool in the air distribution valve is not shifting, check the main spool. It must
slide freely.
D. Excessive air leakage in the pump can prevent cycling. This condition will be
evident. Air leakage into the discharge line indicates a ruptured diaphragm. Air
leakage from the exhaust port indicates leakage in the air distribution valve. See
further service instructions.
E. Blockage in the liquid chamber can impede movements of diaphragm.
F. Blockage in exhaust muffler.
2. Pump cycles but will not pump
A. Suction side of pump pulling in air. Check the suction line for air leaks and be sure
that the end of the suction line is submerged. Check flange bolting. Check valve
flanges and manifold to chamber flange joints.
B. Make certain the suction line or strainer is not plugged. Restriction at the suction
is indicated by a high vacuum reading when a vacuum gauge is installed in the suction
line.
C. Check valves may not be seating properly. To check, remove the suction line and
cover the suction port with your hand. If the unit does not pull a good suction (vacuum),
the check valves should be inspected for proper seating.
D. Static suction lift may be too high. Priming can be improved by elevating the suction
and discharge lines higher than the check valves and pouring liquid into the unit
through the suction inlet. When priming at high suction lifts or with long suction lines
operate the pump at maximum cycle rate.
3. Low performance
A. Capacity is reduced as the discharge pressure increases, as indicated on the
performance curve. Performance capability varies with available inlet air supply.
Check air pressure at the pump inlet when the pump is operating to make certain that
adequate air supply is maintained.
B. Check vacuum at the pump suction. Capacity is reduced as vacuum increases.
Reduced flow rate due to starved suction will be evident when cycle rate can be varied
without change in capacity. This condition will be more prevalent when pumping
viscous liquids. When pumping thick, heavy materials the suction line must be kept
as large in diameter and as short as possible, to keep suction loss minimal.
C. Low flow rate and slow cycling rate indicate restricted flow through the discharge
line. Low flow rate and fast cycling rate indicate restriction in the suction line or air
leakage into suction.
D. Unstable cycling indicates improper check valve seating on one chamber. This
condition is confirmed when unstable cycling repeats consistently on alternate
exhausts. Cycling that is not consistently unstable may indicate partial exhaust