SANDPIPER PULSE OUTPUT KIT User Manual
Page 2
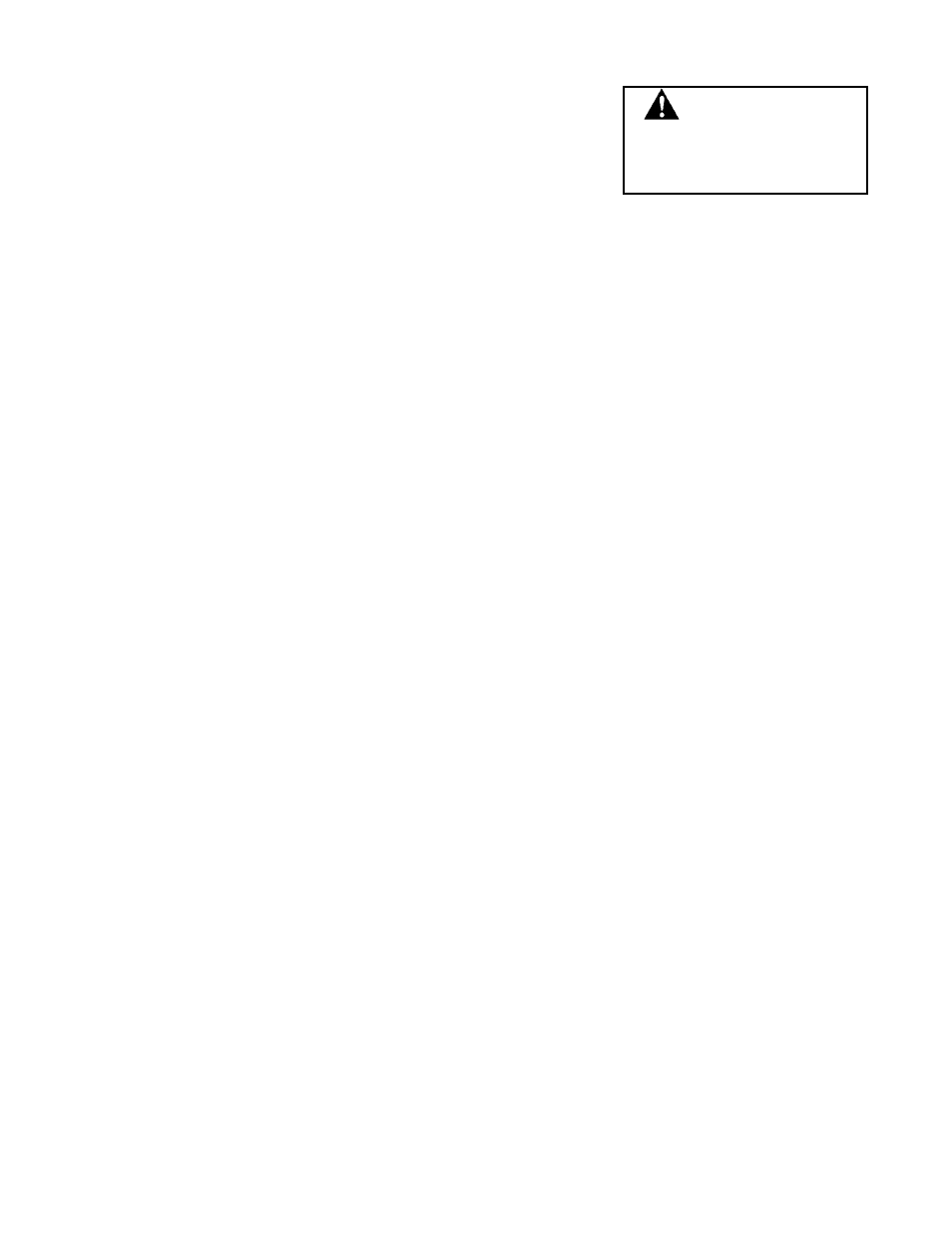
pokdl5sm-rev0614
Pulse Output Kit Page 2
Pump Selection & Installation
Air-operated, double diaphragm pumps (AODD) are semi-positive displacement pumps designed with flexible diaphragms.
AODD have successfully been applied in metering and batching applications where system design allows for minimal variation of:
•
Air Inlet Pressure
•
Suction Head/Lift
•
Discharge Head
•
Pump Speed (Stroke Rate)
•
Product Viscosity
•
NPSH(a)
Variations of any of the above can result in variable, volumetric displacement per pumping stroke which normally holds to
+/- 1% to 3% repeatability. To verify actual displacement in your application, it is essential to follow a calibration procedure. This
allows the batch control to be set for the actual average displacement per pump stroke. The larger the calibration volume, the
more precise the average.
Sizing
Follow the normal pump sizing procedures using published data. DO NOT OVERSIZE THE PUMP. Select the smallest pump
suitable for your use to ensure greater accuracy. The batch size from a SANDPIPER pump will be within +/- one stroke.
Installation
To ensure consistent repeating of the batch size, keep the suction piping short, straight, simple, and as large a diameter as
is practical.
Differential pressure across the check valves of the pump will insure that the check valves seat properly and consistently.
Discharge pressure must always be greater than the suction pressure in the application.
For consistent fluid displacement and system accuracy it is mandatory to keep the discharge line full of product from the pump
to the point of discharge. A one-way check valve installed in the end of the discharge line will accomplish this.
In suction lift applications the pump must be kept primed at all times. Suction lift must be kept to a minimum and a foot valve
may be required in the suction line to keep the pump primed.
In flooded suction applications a back pressure device located in the discharge line may be required to insure sufficient differential
pressure across the pump check valves. The one-way check valve mentioned above may provide sufficient back pressure to
properly seat the pump check valves although additional means may be necessary in some applications.
Install an air line pressure regulator. This ensures a constant air pressure feed to the pump eliminating low to peak usage
pressure spikes which will increase and or decrease the stroke rate of the pump resulting in variable (non-controlled) flow.
CAUTION!
Safety clip locks pump for
security or service. Pump
will NOT operate with safety
clip in place.
Replacing Proximity Sensors
• Shift the main air valve spool toward the sensor being replaced.
• Lock the spool in place by inserting the safety clip
(included in the kit) through the small hole of the opposite end cap.
• Disconnect the sensors from terminal junction.
• Loosen the hex nut holding the proximity sensor in place.
• Remove the sensor from the end cap. Install the replacement sensor.
• Set the clearance between the sensor and the actuator pin to .015" (.38mm), using a feeler gauge or shim stock. The gauge
or shim stock should slide freely, while making contact.
• Tighten the hex nut provided with the replacement proximity sensor to lock in place.
• Reattach terminal juction to proximity sensor
• Remove the safety clip from the end cap. The pump is now ready for use.