SANDPIPER MP05D User Manual
Page 15
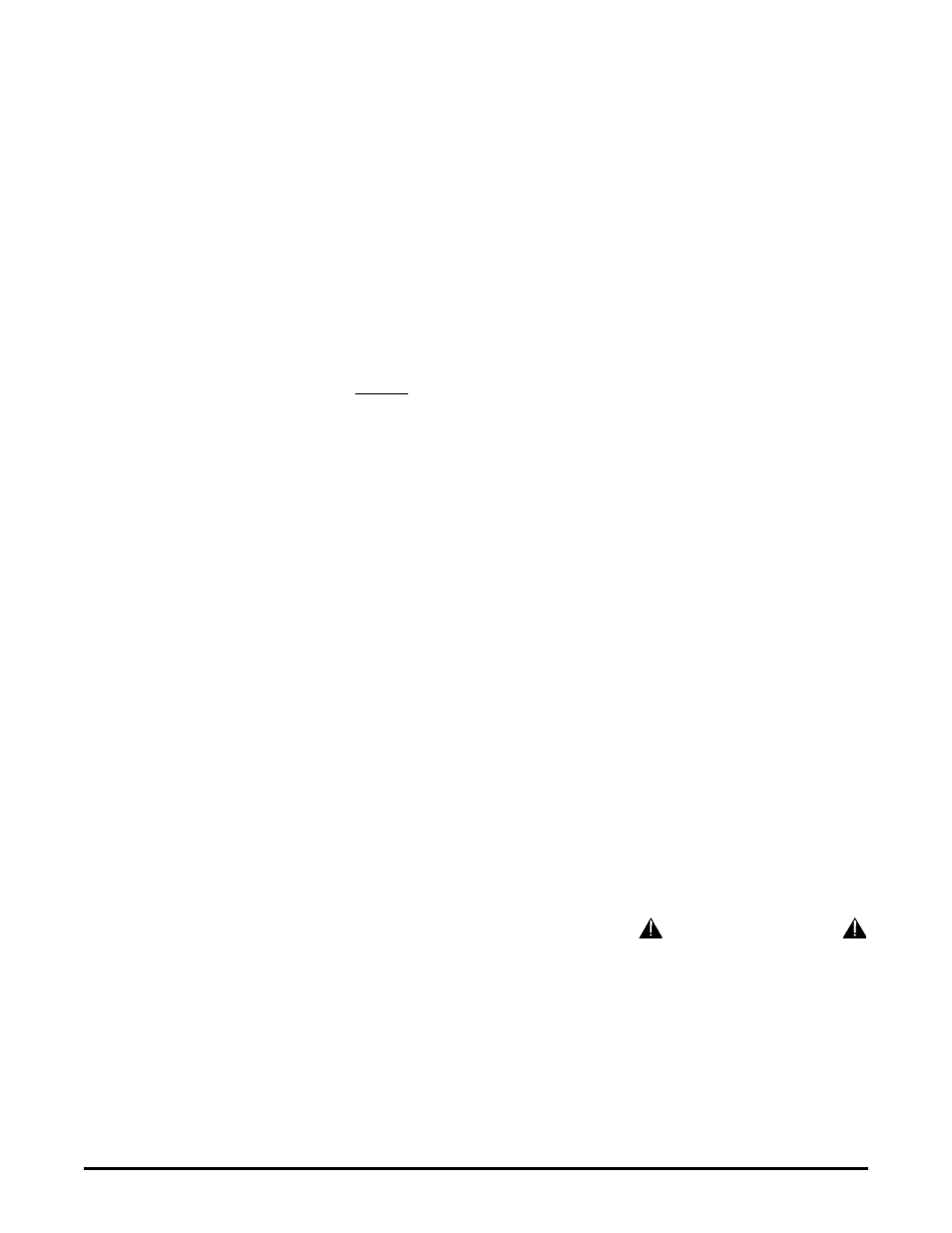
520-168 thru 171-000 3/03
Models MP05D, MP08D, MP12D and MP14D Design Level 1 Page 3
BEFORE OPERATION
Before pump operation, inspect all
gasketed fasteners for looseness
caused by gasket creep. Retorque loose
fasteners to prevent leakage. Follow
recommended torques stated in this
manual
pump operation. An accumulation of oil, dirt or other contaminants from the pump’s
air supply, or from a failed diaphragm, may prevent the spool from moving freely.
This can cause the spool to stick in a position that prevents the pump from operating.
If this is the case, the sleeve and spool set should be removed from the valve body for
cleaning and further inspection.
Remove the spool from the sleeve. Using an arbor press or bench vise (with an
improvised mandrel), press the sleeve from the valve body. Take care not to damage
the sleeve. At this point, inspect the o-rings on the sleeve for nicks, tears or abra-
sions. Damage of this sort could happen during assembly or servicing . A sheared or
cut o-ring can allow the pump’s compressed air supply to leak or bypass within the air
valve assembly, causing the pump to leak compressed air from the pump air exhaust
or not cycle properly. This is most noticeable at pump dead head or high discharge
pressure conditions. Replace any of these o-rings as required or set up a routine,
preventive maintenance schedule to do so on a regular basis. This practice should
include cleaning the spool and sleeve components with a safety solvent or equiva-
lent, inspecting for signs of wear or damage, and replacing worn components.
To re-install the sleeve and spool set, lightly lubricate the o-rings on the sleeve
with an o-ring assembly lubricant or lightweight oil (such as 10 wt. air line lubricant).
Re-install one end cap, and retaining ring on the valve body. Using the arbor press or
bench vise that was used in disassembly, carefully press the sleeve back into the
valve body, without shearing the o-rings. Re-install the spool, opposite end cap and
retaining ring on the valve body. After inspecting and cleaning the gasket surfaces on
the valve body and intermediate, reinstall the valve body on the pump using new
gaskets. Tighten the four hex head capscrews evenly and in an alternating cross
pattern, at 150 in./lbs. (16.94 Newton meters).
AIR SUPPLY
Do not connect the unit to an air supply in excess of 125 PSI (8.61 bars). Install a
shutoff valve in the air supply line to permit removal of the unit for servicing. When
connecting an air supply of rigid piping, mount a section of flexible line to the pump to
eliminate piping strain. In permanent installations, an air line filter is recommended.
OPERATION
This pump has been tested prior to shipment and is ready for use as received. It is
completely self priming and no initial filling with fluid is required.
If the unit is to be totally submerged, the air exhaust must be piped above the
liquid level to prevent the liquid and foreign material from entering the air distribution
valve mechanism.
Open the inlet air valve at least one turn to allow sufficient cycling rate for the
pump to prime (30 to 60 cycles per minute). After pumping starts, adjust the inlet air
valve for the desired pumping capacity. When further opening of the inlet air valve
increases cycling rate without increasing the flow rate, the pump is being starved of
liquid due to suction limitations. Further opening of the air inlet valve will waste
compressed air. Set the inlet air valve for lowest cycling rate that does not decrease
flow rate for most efficient operation.
LEAK DETECTION
Visual leak detection is standard on the MP05D, MP08D, MP12D and MP14D. If
the pumping diaphragm fails, pumped liquid enters the spill containment chamber,
displacing driver fluid. The exchange of pumpage and driver fluid displays a color
change in the sight tube. Driver fluid should be chemically compatible with the
pumped fluid, with an obvious difference in color. If a leak occurs, pumpage is con-
tained in the spill chamber. The pump will continue to work, and in many cases,
repairs can be done when the batch is completed. The air valve and work environ-
ment are protected.
AIR EXHAUST
This pump can be submerged if the materials of construction are compatible with
the liquid and the exhaust is piped above the liquid level. Piping used for the exhaust
should not be smaller than 1" pipe size. Reduced pipe size can restrict the ex-
hausted air and reduce pump performance.