Installation, Output cables for pulse welding, A-3 control cable connection – Lincoln Electric IM611 TIG PULSER User Manual
Page 10: Figure a.2 control cable connection
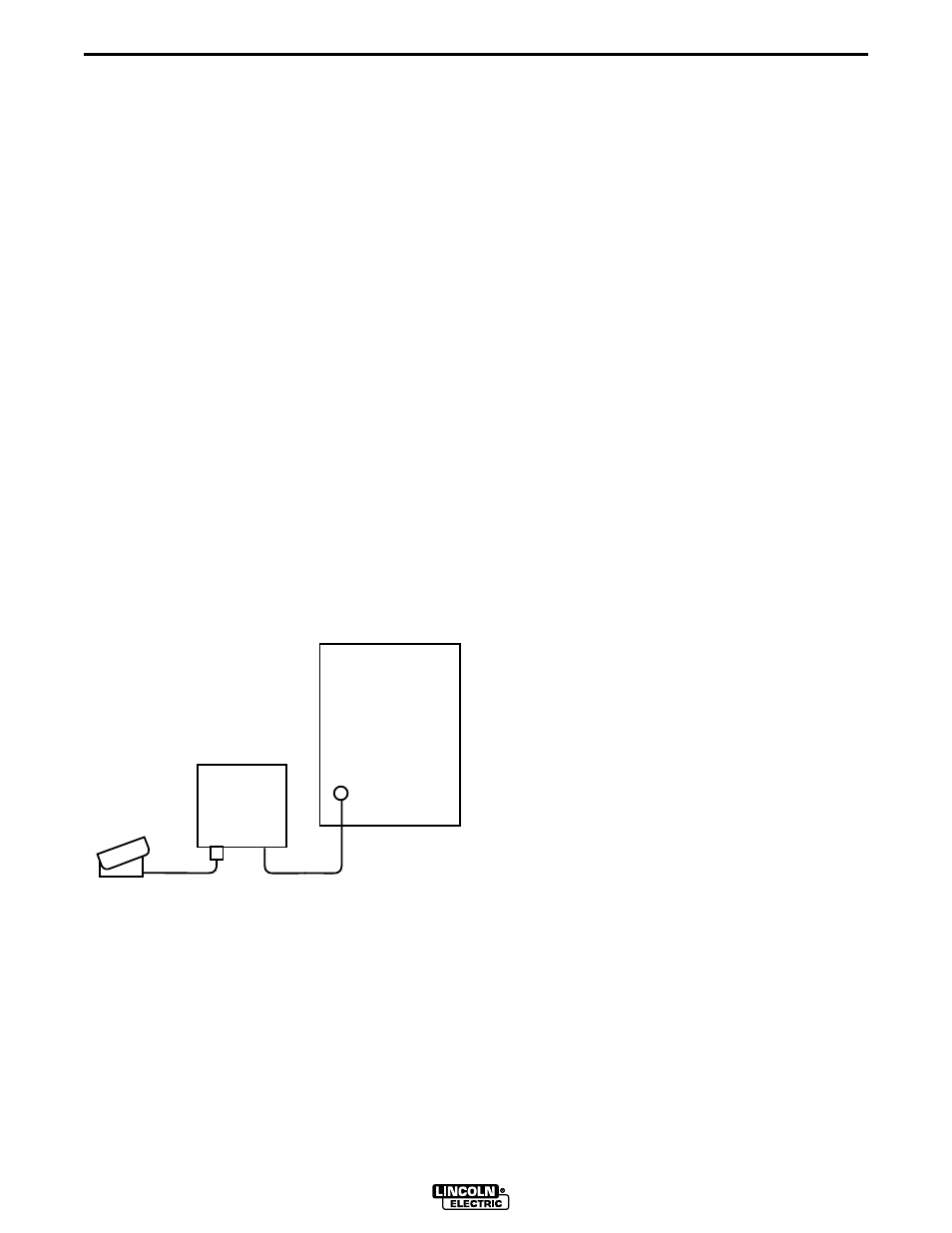
A-3
INSTALLATION
TIG PULSER
A-3
CONTROL CABLE CONNECTION
Refer to Figure A.2.
1. Connect the 6-pin cable plug of the TIG Pulser to
the Amptrol receptacle of the power source. If the
optional 25 foot Control Cable Extension is used, it
should be plugged into the Amptrol receptacle of
the power source and then into the TIG Pulser
cable. Only one control cable should be used; do
not series multiple extensions together. Using 50
foot or longer control cables may lead to poor weld-
ing performance.
2. Connect a foot Amptrol (shown), hand Amptrol or
an Arc Start Switch to the Tig Pulser see Figure A.2
Control cable connection.
3. Set the AMPERAGE control knob on the power
source to MAX position. Note: The pulser won't
properly function if the Amperage control is not
set at maximum.
4. Set the mode switch on power source to 2-step or
4-step TIG depending on the process being used.
Note: If the mode switch is set at Stick, the
Pulser won't have any control on the power
source and the power source will give maximum
output.
TIG
REMOTE
RECEPTACLE
PULSER
TIG
POWER
SOURCE
FOOT AMPTROL
(SHOWN)
OR
HAND AMPTROL
OR
ARC START
SWITCH
Figure A.2 Control Cable Connection.
OUTPUT CABLES FOR PULSE
WELDING
Pulse welding generates high peak currents, which in
turn cause large voltage drops in welding cables. It is
essential that large cables (2/0 minimum) are used and
that all connections are clean and tight.
Because of voltage drops, the total length of the weld-
ing leads (work lead length plus electrode lead length)
should not exceed 50 feet. If longer cables are used,
the welding performance may be degraded.
NOTE: Do not coil the output cables around any
metal object.