Operation, Idealarc, Dc-1500 – Lincoln Electric IM318 IDEALARC DC1500 User Manual
Page 13: Table b.3
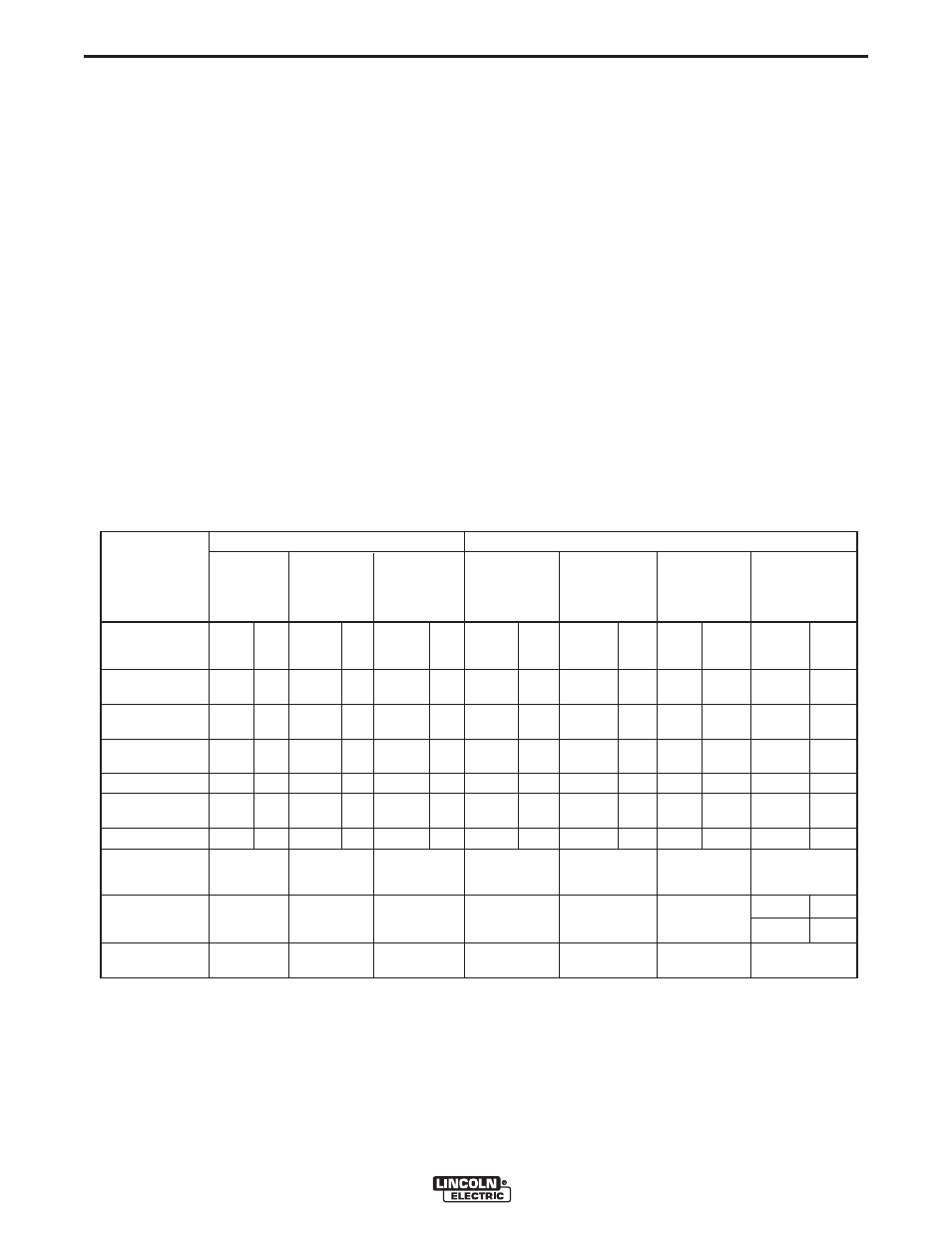
B-4
OPERATION
B-4
IDEALARC
®
DC-1500
INNERSHIELD
SUBMERGED ARC
Single
Single
Innershield
Innershield
High Current
Equipment and
Stickout
Stickout
Twinarc
Single
Tiny Twin
Very Large
Control Settings
under 1 3/4”
over 1 3/4”
Innershield
Solid Wire
Tiny Twin 1/16”
(1)
Over 1/16”
Puddle
Wire Feed Type
NA-3S
NA-3S
NA-3S
Control
or
NA-5
or
NA-5
or
NA-5
NA-3S
NA-5
NA-3S
NA-5 NA-3S
NA-5
NA-3S
NA-5
NA-3N
NA-3N
NA-3N
NA-3S VV Board
Mode Switch
CV
—
CV
—
CV
—
CV
—
CV
—
CV
—
VV
—
NA-3 Inch Speed
Dial Setting
(5)
2
—
2
—
2
—
2
—
2
—
2
—
2
—
NA-5 Arc Striking
—
(4)
—
(4)
—
(4)
—
(4)
—
(4)
—
(4)
—
(4)
Wire Speed
(5)
NA-3 OCV Control
(5)
(6)
—
(6)
—
(6)
—
(6)
—
(6)
—
(6)
—
6.5 - 7.0
—
NA-5 Arc Striking
(4)
(4)
(4)
(4)
(4)
(4)
(4)
Volts Control
—
—
—
—
—
—
—
NA-3 Start Board
(2)
—
Req’d
(2)
—
Req’d
(2)
—
(2)
—
(2)
—
(2)
—
(2)
—
DC-1500 Output
Control Switch —
Remote
Remote
Remote
Remote
Remote
Remote
Remote
Machine or Remote
DC-1500
CV
CV
CV
CV Submerged
CV
CV Submerged
NA-3S
NA-5
Mode
Innershield
Innershield
Innershield
Arc
(3)
Innershield
Arc
(3)
CC
CVS
Switch
DC-1500 Output
Inoperative
Inoperative
Inoperative
Inoperative
Inoperative
Inoperative
Inoperative
Control
For initial test welds, set the NA-5 arc striking
wire speed control to 1/2 the weld wire feed
speed and the arc striking voltage control 4
volts above the weld voltage.
•
If striking is still not satisfactory, see the NA-5
operating manual for information on the feed
motor acceleration.
•
If installed, adjust the “Start Controls” to set the
welding procedures for the time set on the timer
to provide the bead size, penetration, or other
factor as needed for the application. If not used,
this board should be disconnected and the
jumper plug replaced.
•
If installed, adjust the “Crater Controls” to set
the welding procedures for the set time after the
stop button is pressed to provide the bead size
or fill the crater as needed for the application. If
not used, this board should be disconnected
and the jumper plug replaced.
•
Set the “Burnback Time” to provide the stopping
characteristics needed.
General Set-Up Procedures When Using DC-1500 and
Lincoln Automatic Head NA-5
(See Table B.3)
1. Install the NA-5 per the information in the NA-5 oper-
ating manual (IM-305). Connect the NA-5 to the DC-
1500 as described on the connection diagram.
2. Place the DC-1500 mode switch in the proper position
according to the process and procedure to be used.
3. Place the machine/remote switch in remote.
4. Connect the work lead to the work or a suitable piece
of scrap. Clip the end of the electrode to a sharp
point.
5. Preset the Start (if used), Weld and Crater (if used)
Controls to the wire speed and voltage specified in
the procedure.
6. Make several test welds, readjusting the starting and
stopping controls in the following order:
• Set the Arc Striking Wire Speed and Volts Controls
for optimum arc striking.
RECOMMENDED SET-UP PROCEDURES FOR NA-3/DC-1500, NA-5/DC-1500
(1)
Starting is best with “hot” starting. Start button is pressed with wire above the work.
(2)
If an Na-3 start board is called for, refer to (General Set-Up Procedures When Using DC-1500 and Lincoln Automatic Head NA-3
in this Operation Section) for details on how to set the controls. If an NA-3 start board is not required, it should be electrically discon-
nected and the jumper plug replaced.
(3)
Some high speed welding procedures may perform better on the CV Innershield mode. Merely change the switch between CV Innershield
and CV Submerged arc position and select the best welding.
(4)
The NA-5 arc striking wire speed should initially be set at 1/2 the welding wire feed speed, and the NA-5 arc striking volts control 4
volts above the welding voltage. These controls can be adjusted as required for optimum arc striking.
(5)
Exact dial setting depends on cable size and length, carbon size, etc.
(6)
Set the OCV control to the same dial setting as the NA-3 voltage control. For initial test welds, choose the setting on Table B.1 in this
Operation Section.
TABLE B.3